A two-roll mill is a versatile machine used primarily in the plastic, rubber, and chemical industries for mixing, compounding, and processing materials. It consists of two horizontally placed metal rolls that rotate towards each other, creating a gap known as the "nip." The friction ratio between the rolls generates shearing action, which is essential for mixing and processing materials like polymers, pigments, adhesives, and more. Two-roll mills are valued for their ability to provide precise temperature control, durability, and cost-effectiveness. They are widely used in applications such as formula development, color matching, quality control, and small-scale production across various industries.
Key Points Explained:
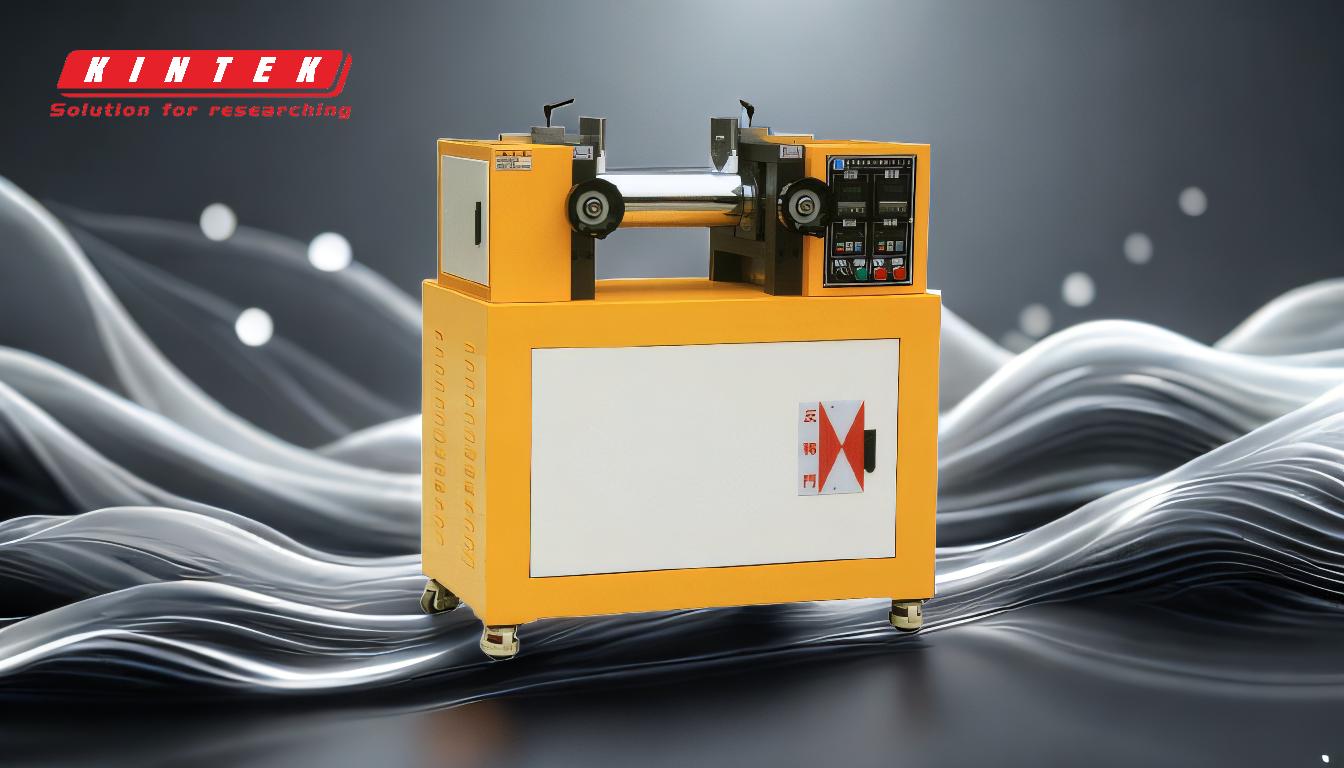
-
Basic Structure and Functionality:
- A two-roll mill consists of two horizontally placed hollow metal rolls that rotate towards each other.
- The gap between the rolls, known as the "nip," can be adjusted to control the thickness and processing of materials.
- The speed difference between the rolls, called the friction ratio, generates shearing action, which is crucial for mixing and processing materials.
-
Applications in Various Industries:
- Plastics and Rubber: Used for polymer milling, rubber mixing, and formula development.
- Chemicals and Pharmaceuticals: Suitable for mixing pigments, adhesives, sealants, and coatings.
- Food and Cosmetics: Utilized for processing food products, cosmetics, and high-performance ceramics.
- Electronics and Printing: Essential for producing electronic thick film inks, printing inks, and cable covers.
-
Key Features and Benefits:
- Temperature Control: Designed to provide optimum temperature control and cooling effects, ensuring consistent material processing.
- Durability and Customization: Built to last and can be customized to meet specific production needs.
- Cost-Effectiveness: Reduces production costs and requires minimal maintenance, making it a cost-efficient solution for industrial applications.
-
Role in Research and Development:
- Used in labs for evaluating pigments, masterbatches, and polymer mastication.
- Essential for material development, testing, and quality control in industries like plastics, rubber, and chemicals.
-
Comparison with Three-Roll Mills:
- While two-roll mills are primarily used for mixing and compounding, three-roll mills are often employed for finer grinding and dispersion of materials.
- Both types of mills are used in similar industries, but two-roll mills are more commonly associated with rubber and plastic processing.
-
Operational Process:
- Materials such as rubber, plastic, or chemicals are placed in the nip between the two rolls.
- The rolls generate heat through friction, softening the materials and allowing them to be mixed, compounded, or processed into the desired form.
-
Industrial and Educational Use:
- Widely used in industrial production for tasks like PVC powder mixing, color sampling, and small-batch testing.
- Also employed in educational settings for teaching material processing and compounding techniques.
By understanding these key points, purchasers and users of two-roll mills can better appreciate their versatility, functionality, and importance across a wide range of industries.
Summary Table:
Feature | Description |
---|---|
Structure | Two horizontally placed metal rolls with an adjustable gap (nip). |
Functionality | Generates shearing action for mixing and processing materials. |
Applications | Plastics, rubber, chemicals, food, cosmetics, electronics, and printing. |
Key Benefits | Precise temperature control, durability, customization, and cost-effectiveness. |
Use Cases | Formula development, color matching, quality control, and small-scale production. |
Industries | Industrial production, R&D labs, and educational institutions. |
Ready to enhance your material processing? Contact us today to find the perfect two-roll mill for your needs!