An auger reactor is a specialized type of reactor used in various industrial and chemical processes, particularly for reactions involving solid or granular materials. Unlike traditional reactors that rely on liquid or gas-phase reactions, auger reactors utilize a screw-like mechanism (the auger) to transport, mix, and process materials. This design is particularly useful for continuous processes, where materials need to be fed, reacted, and discharged in a controlled manner. The auger ensures uniform mixing, efficient heat transfer, and precise control over reaction conditions, making it ideal for applications such as pyrolysis, biomass processing, and solid-state chemical reactions.
Key Points Explained:
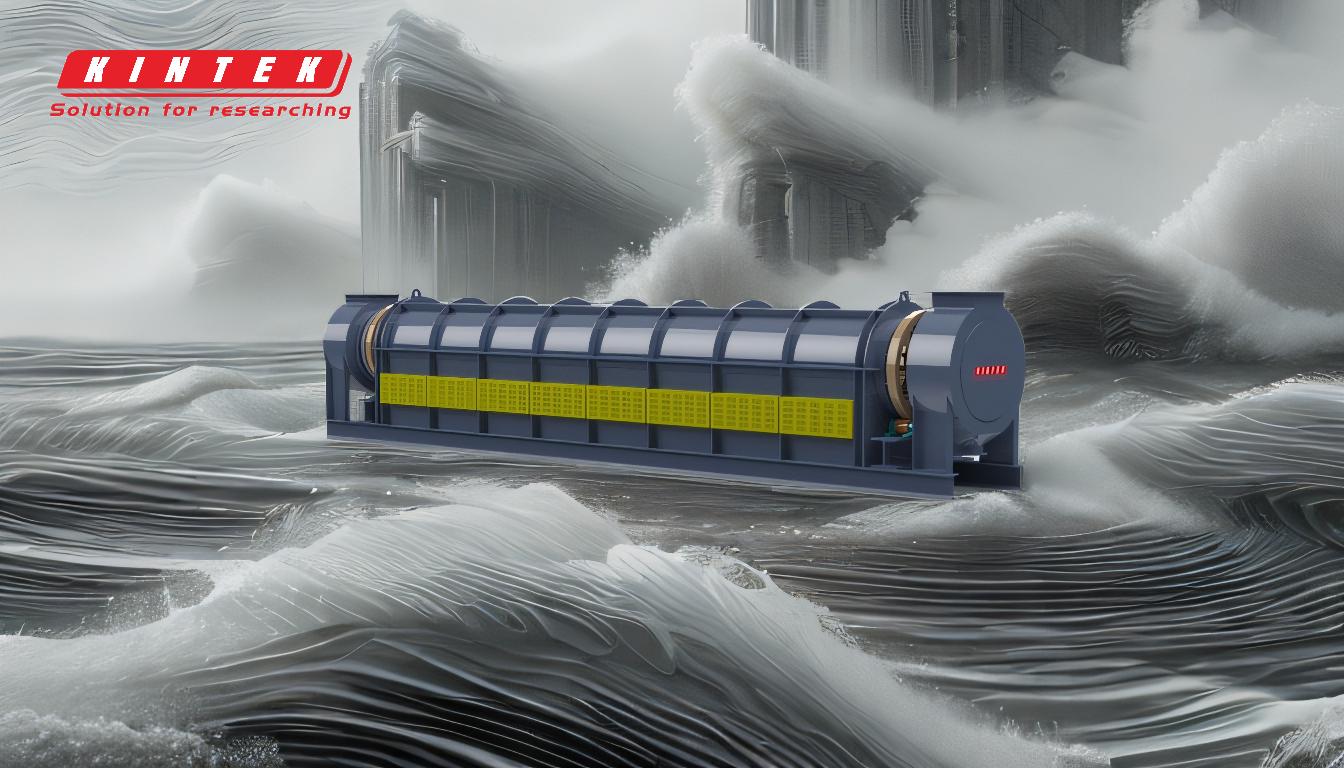
-
Definition and Purpose of an Auger Reactor:
- An auger reactor is a type of reactor designed for processing solid or granular materials. It is equipped with an auger (a screw-like mechanism) that facilitates the movement and mixing of materials within the reactor.
- The primary purpose of an auger reactor is to enable continuous processing of materials, ensuring uniform mixing, efficient heat transfer, and controlled reaction conditions. This makes it particularly suitable for applications like pyrolysis, biomass conversion, and solid-state chemical reactions.
-
Key Components of an Auger Reactor:
- Auger Mechanism: The central component of the reactor, the auger, is responsible for transporting and mixing materials. Its design ensures consistent movement and mixing, which is critical for uniform reaction conditions.
- Reactor Vessel: The vessel houses the auger and the materials being processed. It is designed to withstand the specific conditions of the reaction, such as high temperatures or pressures.
- Temperature Control System: Like other reactors, an auger reactor includes a system to regulate temperature, ensuring optimal reaction conditions.
- Feed and Discharge Ports: These ports allow for the continuous introduction of raw materials and the removal of processed products, enabling uninterrupted operation.
-
Applications of Auger Reactors:
- Pyrolysis: Auger reactors are widely used in pyrolysis processes, where organic materials are decomposed at high temperatures in the absence of oxygen. The auger ensures consistent movement of materials through the reactor, facilitating efficient decomposition.
- Biomass Processing: In biomass conversion, auger reactors are used to process organic materials like wood or agricultural waste into biofuels or other valuable products.
- Solid-State Chemical Reactions: For reactions involving solid materials, auger reactors provide the necessary mixing and transport mechanisms to ensure uniform reaction conditions.
-
Advantages of Auger Reactors:
- Continuous Processing: Unlike batch reactors, auger reactors allow for continuous operation, increasing efficiency and throughput.
- Uniform Mixing: The auger ensures that materials are thoroughly mixed, leading to consistent reaction conditions and product quality.
- Versatility: Auger reactors can handle a wide range of materials, including solids, granules, and powders, making them suitable for diverse applications.
-
Comparison with Other Reactor Types:
- Unlike high-pressure reactors, which are designed for liquid or gas-phase reactions under high pressure, auger reactors are optimized for solid or granular materials and continuous processing.
- Glass reactors, typically used for small-scale or laboratory applications, are not suitable for the high-throughput or high-temperature conditions often required in auger reactor applications.
In summary, an auger reactor is a versatile and efficient tool for processing solid or granular materials in continuous industrial processes. Its unique design, centered around the auger mechanism, ensures uniform mixing, controlled reaction conditions, and high throughput, making it indispensable in applications like pyrolysis, biomass processing, and solid-state chemical reactions.
Summary Table:
Key Aspect | Description |
---|---|
Definition | A reactor designed for processing solid or granular materials using a screw-like auger mechanism. |
Primary Purpose | Continuous processing with uniform mixing, efficient heat transfer, and controlled reaction conditions. |
Key Components | Auger mechanism, reactor vessel, temperature control system, feed/discharge ports. |
Applications | Pyrolysis, biomass processing, solid-state chemical reactions. |
Advantages | Continuous operation, uniform mixing, versatility for diverse materials. |
Comparison with Others | Optimized for solids/granules; not suitable for high-pressure or small-scale lab use. |
Discover how an auger reactor can optimize your industrial processes—contact us today for expert guidance!