Biomass is organic material derived from plants and animals, which can be used as a renewable energy source. Biomass pyrolysis is a thermochemical process that converts biomass into valuable products like biochar, bio-oil, and syngas by heating it in the absence of oxygen. This process occurs at high temperatures, typically above 400°C, and involves several stages, including pre-treatment, pyrolysis, and cooling. The end products are useful for energy generation, soil improvement, and chemical extraction. Biomass pyrolysis is gaining attention due to its ability to reduce biomass volume, lower costs, and produce high-value outputs, making it a sustainable alternative to traditional energy sources.
Key Points Explained:
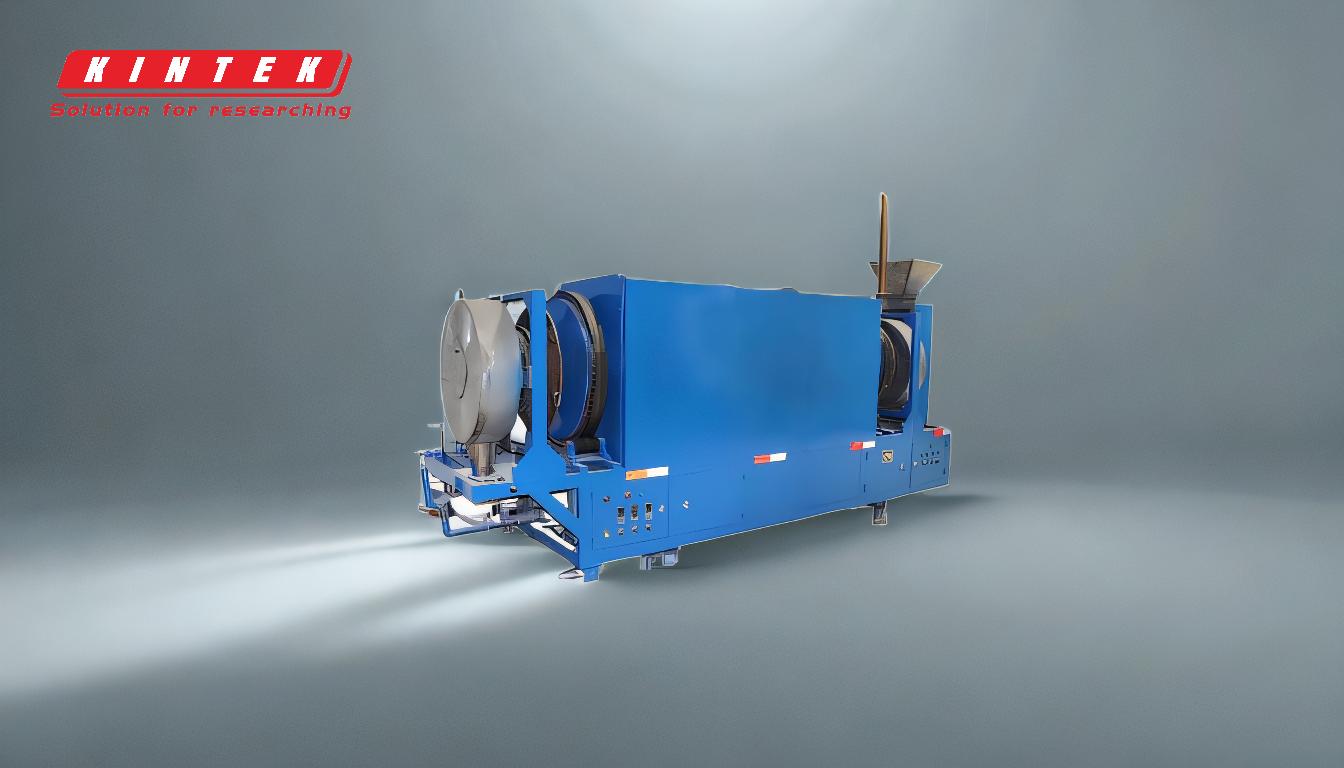
-
What is Biomass?
- Biomass refers to organic materials derived from plants and animals, such as wood, agricultural residues, and animal waste. It is a renewable energy source because it can be replenished through natural processes. Biomass is used for energy production, as it contains stored energy from the sun, captured through photosynthesis.
-
Definition of Biomass Pyrolysis
- Biomass pyrolysis is a thermochemical process that decomposes organic material at high temperatures (typically above 400°C) in the absence of oxygen. This process transforms biomass into three main products: biochar (a solid), bio-oil (a liquid), and syngas (a gas). These products have various applications, including energy generation, soil enhancement, and chemical production.
-
Stages of Biomass Pyrolysis
- The biomass pyrolysis process can be broken down into several key stages:
- Pre-treatment: This involves drying and crushing the biomass to reduce moisture content and increase surface area, making it easier to heat uniformly.
- Pyrolysis: The biomass is heated in an oxygen-free environment, causing it to decompose into biochar, bio-oil, and syngas. This stage typically occurs at temperatures ranging from 400°C to 800°C.
- Cooling and Discharging: After pyrolysis, the biochar is cooled and discharged for storage or further processing. The syngas and bio-oil are also collected and processed.
- De-dusting: The exhaust gases are cleaned to remove harmful substances, ensuring that the process is environmentally friendly.
- The biomass pyrolysis process can be broken down into several key stages:
-
Products of Biomass Pyrolysis
- The pyrolysis process yields three primary products:
- Biochar: A carbon-rich solid that can be used as a soil amendment to improve soil fertility and sequester carbon.
- Bio-oil: A liquid product that can be used as a fuel or further refined into chemicals and other high-value products.
- Syngas: A mixture of gases, including hydrogen, carbon monoxide, and methane, which can be used as a fuel for energy generation or as a feedstock for chemical synthesis.
- The pyrolysis process yields three primary products:
-
Advantages of Biomass Pyrolysis
- Sustainability: Biomass pyrolysis provides a renewable energy source, reducing reliance on fossil fuels.
- Volume Reduction: The process significantly reduces the volume of biomass, making it easier to store and transport.
- Cost-Effectiveness: Pyrolysis is a relatively low-cost process compared to other biomass conversion technologies.
- Versatility: The end products (biochar, bio-oil, and syngas) have multiple applications, from energy production to soil improvement and chemical extraction.
- Environmental Benefits: By converting biomass into useful products, pyrolysis helps reduce waste and greenhouse gas emissions.
-
Applications of Pyrolysis Products
- Biochar: Used in agriculture to enhance soil fertility, retain moisture, and sequester carbon, thereby reducing greenhouse gas emissions.
- Bio-oil: Can be used directly as a fuel or upgraded to produce chemicals, plastics, and other materials. It is also being explored as a potential substitute for petroleum-based fuels.
- Syngas: Used for electricity generation, heating, or as a raw material for producing synthetic fuels and chemicals.
-
Challenges and Considerations
- Temperature Control: Maintaining the right temperature during pyrolysis is crucial for optimizing the yield and quality of the end products.
- Feedstock Variability: The composition of biomass can vary widely, affecting the efficiency and output of the pyrolysis process.
- Environmental Impact: While pyrolysis is generally considered environmentally friendly, the process must be carefully managed to minimize emissions of harmful gases and particulates.
In conclusion, biomass pyrolysis is a promising technology for converting organic waste into valuable energy and chemical products. It offers a sustainable, cost-effective, and versatile solution for managing biomass resources while contributing to environmental conservation.
Summary Table:
Aspect | Details |
---|---|
Biomass Definition | Organic material from plants and animals, used as a renewable energy source. |
Pyrolysis Process | Thermochemical decomposition at >400°C without oxygen. |
Main Products | Biochar (solid), bio-oil (liquid), syngas (gas). |
Applications | Energy generation, soil enhancement, chemical extraction. |
Advantages | Sustainability, volume reduction, cost-effectiveness, versatility. |
Challenges | Temperature control, feedstock variability, environmental impact. |
Learn more about how biomass pyrolysis can benefit your operations—contact us today!