Catalytic pyrolysis of plastic waste is a specialized thermochemical process that converts plastic waste into valuable products such as liquid oil, gases, and char. Unlike conventional pyrolysis, catalytic pyrolysis incorporates a catalyst to enhance the efficiency and quality of the end products. This process involves heating plastic waste in the absence of oxygen, breaking down the long polymer chains into smaller hydrocarbon molecules. The use of a catalyst, such as modified natural zeolite, lowers the required reaction temperature and improves the yield of desirable products like high-quality pyrolysis oil. This method is considered eco-friendly as it helps reduce plastic pollution and provides an alternative to fossil fuels.
Key Points Explained:
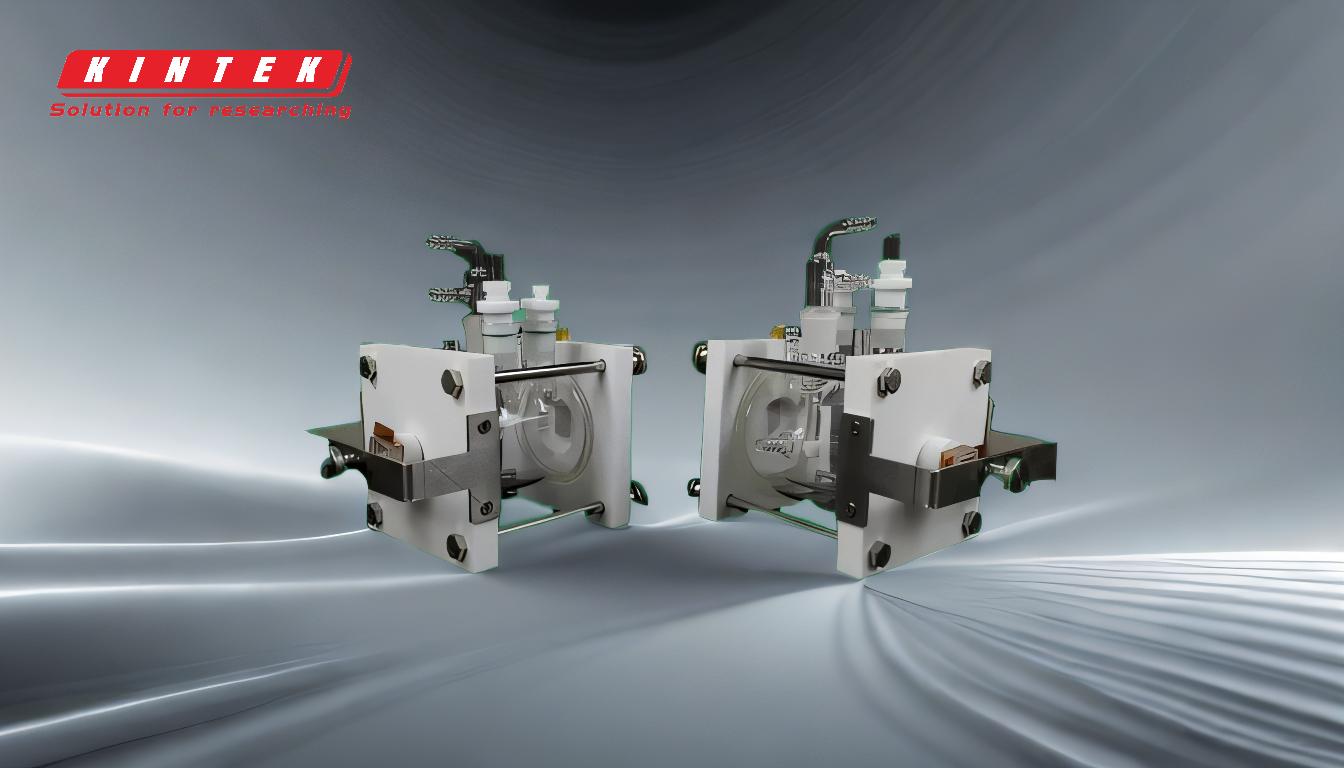
-
Definition of Catalytic Pyrolysis:
- Catalytic pyrolysis is a thermochemical decomposition process where plastic waste is heated in the absence of oxygen, aided by a catalyst.
- The catalyst accelerates the breakdown of plastic polymers into smaller hydrocarbon molecules, producing liquid oil, gases, and char.
-
Key Differences from Conventional Pyrolysis:
- Catalyst Involvement: Catalytic pyrolysis uses a catalyst (e.g., modified natural zeolite) to enhance the reaction efficiency and product quality.
- Lower Temperature Requirement: The presence of a catalyst reduces the energy input needed for the reaction, making the process more energy-efficient.
- Improved Product Yield: Catalytic pyrolysis produces a higher yield of valuable products, such as high-quality pyrolysis oil, compared to non-catalytic methods.
-
Process Steps:
- Preprocessing: Plastic waste is shredded, dried, and separated from non-plastic materials to ensure uniformity and improve efficiency.
- Feeding: The preprocessed plastic is transferred to the pyrolysis reactor.
- Heating and Reaction: The plastic is heated to a specific temperature (e.g., 280°C) in an oxygen-free environment. The catalyst facilitates the breakdown of polymers into smaller molecules.
- Product Separation: The resulting products (oil, gas, and char) are separated and collected for further processing or use.
-
Role of the Catalyst:
- The catalyst, such as modified natural zeolite, plays a critical role in lowering the activation energy required for the pyrolysis reaction.
- It promotes selective cracking of plastic polymers, leading to a higher yield of liquid oil and reducing the formation of unwanted byproducts.
-
Advantages of Catalytic Pyrolysis:
- Eco-Friendly: Converts non-biodegradable plastic waste into useful products, reducing environmental pollution.
- Resource Recovery: Produces valuable products like pyrolysis oil, which can be used as an alternative to fossil fuels.
- Energy Efficiency: The use of a catalyst reduces the overall energy consumption of the process.
-
Applications of the End Products:
- Pyrolysis Oil: Can be refined and used as fuel in industrial applications or further processed into chemicals.
- Syngas: A mixture of hydrogen and carbon monoxide, which can be used as a fuel or chemical feedstock.
- Carbon Black: Used as a reinforcing agent in rubber products or as a pigment in inks and coatings.
-
Challenges and Considerations:
- Catalyst Cost and Availability: The cost and availability of effective catalysts can impact the scalability of the process.
- Feedstock Variability: The composition of plastic waste can vary, affecting the efficiency and product quality of the pyrolysis process.
- Process Optimization: Continuous research is needed to optimize reaction conditions, catalyst performance, and product separation techniques.
-
Future Prospects:
- Catalytic pyrolysis is a promising technology for sustainable waste management and resource recovery.
- Ongoing research focuses on developing more efficient and cost-effective catalysts, as well as scaling up the process for industrial applications.
By leveraging catalytic pyrolysis, plastic waste can be transformed into valuable resources, contributing to a circular economy and reducing reliance on fossil fuels. This method not only addresses the growing issue of plastic pollution but also provides a sustainable pathway for energy and material recovery.
Summary Table:
Aspect | Details |
---|---|
Definition | Thermochemical process converting plastic waste into oil, gas, and char. |
Key Difference | Uses a catalyst (e.g., modified natural zeolite) for better efficiency. |
Process Steps | Preprocessing, feeding, heating, and product separation. |
Advantages | Eco-friendly, resource recovery, and energy-efficient. |
Applications | Pyrolysis oil (fuel), syngas (chemical feedstock), and carbon black (rubber). |
Challenges | Catalyst cost, feedstock variability, and process optimization. |
Future Prospects | Promising for sustainable waste management and industrial scaling. |
Transform plastic waste into valuable resources with catalytic pyrolysis—contact us today to learn more!