Catalytic upgrading of pyrolysis is a process that enhances the quality of pyrolysis products, particularly bio-oil, by using catalysts to remove undesirable components such as oxygen and nitrogen. This process improves the stability, reduces corrosiveness, and increases the economic feasibility of bio-oil, making it more suitable for commercial use as a fuel. By optimizing selectivity and removing oxygenated groups, catalytic upgrading transforms raw pyrolysis products into higher-quality, more stable, and economically viable fuels that can be used as drop-in replacements for conventional hydrocarbon fuels.
Key Points Explained:
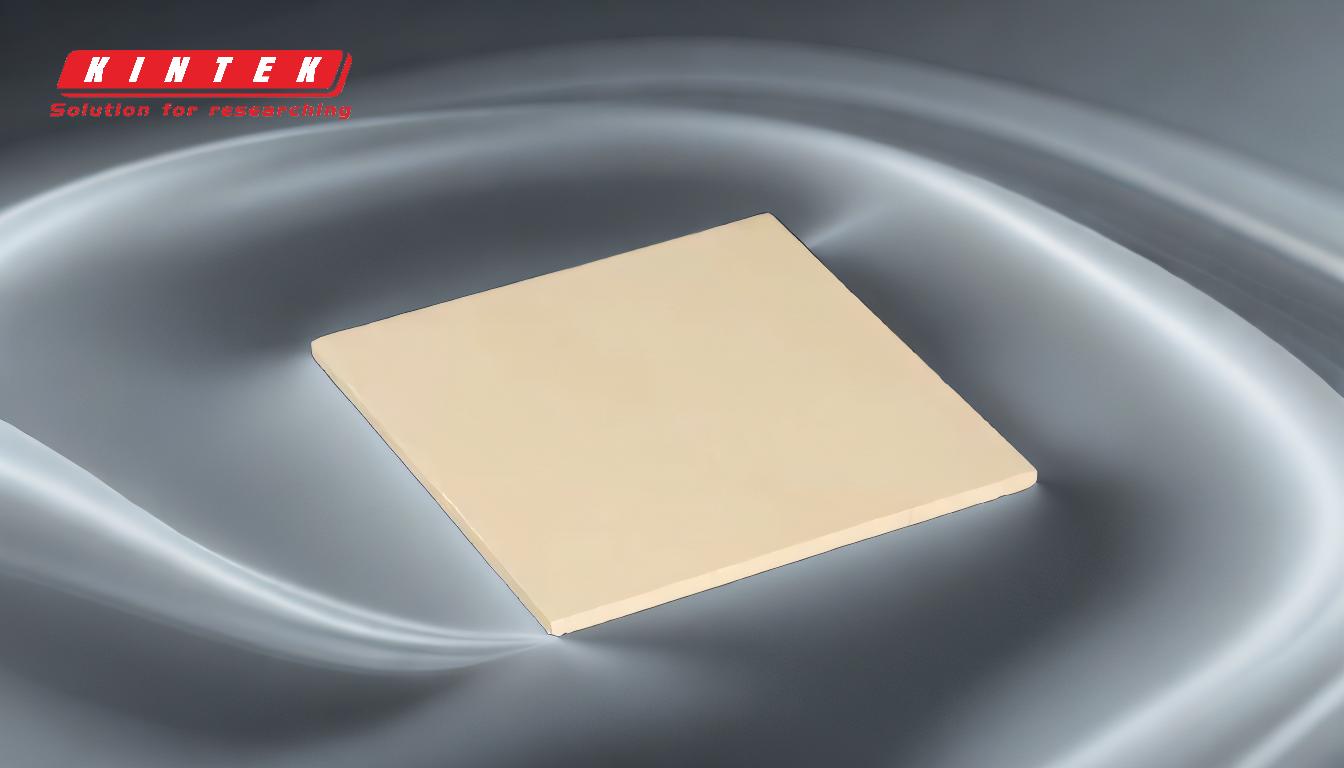
-
Definition of Catalytic Upgrading of Pyrolysis:
- Catalytic upgrading refers to the use of catalysts during or after the pyrolysis process to improve the quality of the resulting bio-oil.
- Pyrolysis itself is a thermal decomposition process that breaks down biomass in the absence of oxygen, producing bio-oil, biochar, and syngas.
-
Purpose of Catalytic Upgrading:
- The primary goal is to remove oxygenated groups and other undesirable components (e.g., nitrogen) from bio-oil.
- This process enhances the properties of bio-oil, making it more stable, less corrosive, and more suitable for use as a fuel.
-
Key Benefits of Catalytic Upgrading:
- Improved Stability: Reduces the acidic and oxygen content, which decreases the reactivity and instability of bio-oil.
- Reduced Corrosiveness: Lower oxygen content minimizes the corrosive nature of bio-oil, making it safer to handle and store.
- Enhanced Economic Feasibility: Upgraded bio-oil is more commercially viable, as it can be used as a drop-in fuel in existing infrastructure without significant modifications.
-
Mechanism of Catalytic Upgrading:
- Catalysts are used to selectively break down oxygenated compounds (e.g., phenols, aldehydes, and ketones) into simpler hydrocarbons.
- This process can occur during pyrolysis (in-situ upgrading) or after pyrolysis (ex-situ upgrading).
- Common catalysts include zeolites, metal oxides, and supported metals, which promote reactions such as deoxygenation, cracking, and hydrogenation.
-
Impact on Bio-Oil Quality:
- Catalytic upgrading results in bio-oil with a higher energy density and lower viscosity.
- The upgraded bio-oil contains fewer oxygenated compounds, which improves its compatibility with conventional fuels and reduces the need for further refining.
-
Applications of Upgraded Bio-Oil:
- Upgraded bio-oil can be used as a renewable fuel in transportation, heating, and power generation.
- It can also serve as a feedstock for producing drop-in fuels, which are chemically identical to petroleum-based fuels and can be used in existing engines and infrastructure.
-
Economic and Environmental Advantages:
- Catalytic upgrading makes bio-oil production more economically viable by increasing the market value of the product.
- It contributes to sustainability by providing a renewable alternative to fossil fuels and reducing greenhouse gas emissions.
-
Challenges and Future Directions:
- Challenges include the high cost of catalysts, catalyst deactivation, and the need for efficient separation and recovery processes.
- Future research focuses on developing more cost-effective and durable catalysts, as well as optimizing the upgrading process to maximize yield and quality.
By addressing these key points, catalytic upgrading of pyrolysis emerges as a critical process for transforming raw biomass into a high-quality, renewable fuel that can compete with traditional fossil fuels in terms of performance and economic viability.
Summary Table:
Aspect | Details |
---|---|
Definition | Use of catalysts during/after pyrolysis to improve bio-oil quality. |
Purpose | Remove oxygenated groups and undesirable components for better fuel quality. |
Key Benefits | Improved stability, reduced corrosiveness, enhanced economic feasibility. |
Mechanism | Catalysts break down oxygenated compounds into simpler hydrocarbons. |
Impact on Bio-Oil | Higher energy density, lower viscosity, fewer oxygenated compounds. |
Applications | Renewable fuel for transportation, heating, and power generation. |
Advantages | Economic viability, sustainability, reduced greenhouse gas emissions. |
Challenges | High catalyst costs, deactivation, and separation/recovery efficiency. |
Discover how catalytic upgrading can revolutionize your bio-oil production—contact our experts today!