Catalytic pyrolysis and thermal pyrolysis are two distinct methods used to break down organic materials into smaller molecules, primarily for the production of biofuels, chemicals, and other valuable products. Thermal pyrolysis relies solely on heat to decompose the feedstock, while catalytic pyrolysis introduces a catalyst to lower the reaction temperature, improve product selectivity, and enhance the overall efficiency of the process. The choice between these methods depends on factors such as the desired end products, feedstock type, and economic considerations. Below, the key differences, advantages, and applications of both methods are explored in detail.
Key Points Explained:
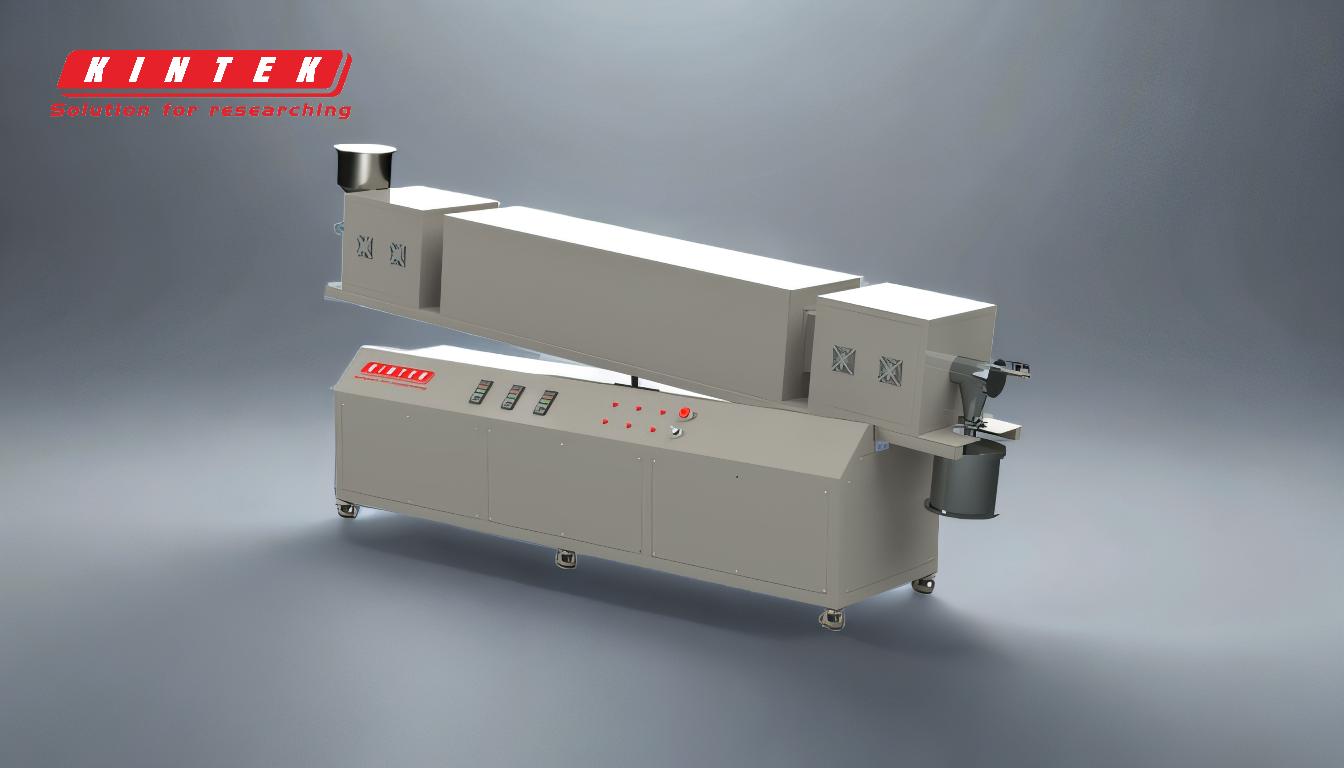
-
Definition and Mechanism:
-
Thermal Pyrolysis:
- Thermal pyrolysis involves heating organic materials (such as biomass, plastics, or waste) in the absence of oxygen to high temperatures (typically 400–800°C). This heat causes the chemical bonds in the feedstock to break, producing gases, liquids (bio-oil), and solid char.
- The process is driven solely by thermal energy, and the reaction conditions (temperature, heating rate, and residence time) determine the product distribution.
-
Catalytic Pyrolysis:
- Catalytic pyrolysis incorporates a catalyst into the pyrolysis process to facilitate the breakdown of feedstock at lower temperatures (typically 300–600°C). The catalyst accelerates the reaction, reduces energy requirements, and improves the quality and yield of desired products.
- Catalysts can be acid-based (e.g., zeolites), base-based, or metal-based, and they influence the reaction pathways to favor specific products.
-
Thermal Pyrolysis:
-
Temperature and Energy Requirements:
-
Thermal Pyrolysis:
- Requires higher temperatures (400–800°C) to achieve effective decomposition, leading to higher energy consumption.
- The high temperatures can also result in the formation of unwanted byproducts, such as tar and char.
-
Catalytic Pyrolysis:
- Operates at lower temperatures (300–600°C) due to the presence of a catalyst, which reduces energy input and operational costs.
- Lower temperatures also minimize the formation of undesirable byproducts, improving the overall process efficiency.
-
Thermal Pyrolysis:
-
Product Selectivity and Quality:
-
Thermal Pyrolysis:
- Produces a wide range of products, including bio-oil, syngas, and char. The bio-oil often contains high levels of oxygenated compounds, making it less stable and requiring further upgrading for use as fuel.
- The product distribution is less controllable, and the quality of bio-oil can vary significantly depending on the feedstock and process conditions.
-
Catalytic Pyrolysis:
- Enhances product selectivity by favoring the formation of specific compounds, such as aromatic hydrocarbons, which are more valuable for fuel and chemical production.
- The bio-oil produced is of higher quality, with lower oxygen content and improved stability, reducing the need for extensive post-processing.
-
Thermal Pyrolysis:
-
Feedstock Flexibility:
-
Thermal Pyrolysis:
- Can process a wide variety of feedstocks, including lignocellulosic biomass, plastics, and municipal solid waste.
- However, the efficiency and product quality may vary significantly depending on the feedstock composition.
-
Catalytic Pyrolysis:
- Also versatile in terms of feedstock but requires careful selection of catalysts to match the specific feedstock properties.
- Certain feedstocks, such as plastics, may benefit more from catalytic pyrolysis due to the ability to tailor the catalyst for deoxygenation and cracking reactions.
-
Thermal Pyrolysis:
-
Economic and Environmental Considerations:
-
Thermal Pyrolysis:
- Generally simpler and less expensive in terms of initial setup and operation, as it does not require catalysts.
- However, the higher energy requirements and lower product quality can increase overall costs and environmental impact.
-
Catalytic Pyrolysis:
- While the use of catalysts adds to the initial cost, the improved efficiency, lower energy consumption, and higher-quality products can offset these expenses over time.
- The process is more environmentally friendly due to reduced emissions and better utilization of resources.
-
Thermal Pyrolysis:
-
Applications:
-
Thermal Pyrolysis:
- Commonly used for waste management and the production of biochar, which can be used as a soil amendment or for carbon sequestration.
- Bio-oil from thermal pyrolysis is often used as a fuel or feedstock for further refining.
-
Catalytic Pyrolysis:
- Primarily used for the production of high-quality biofuels and chemicals, such as benzene, toluene, and xylene (BTX), which are valuable in the petrochemical industry.
- The process is also being explored for recycling plastics into useful hydrocarbons.
-
Thermal Pyrolysis:
-
Challenges and Future Directions:
-
Thermal Pyrolysis:
- Challenges include the high energy input, variability in product quality, and the need for post-processing of bio-oil.
- Future improvements may focus on optimizing reactor designs and integrating thermal pyrolysis with other processes, such as gasification.
-
Catalytic Pyrolysis:
- Key challenges include catalyst deactivation, high catalyst costs, and the need for catalyst regeneration.
- Research is ongoing to develop more efficient, durable, and cost-effective catalysts, as well as to explore hybrid systems combining thermal and catalytic approaches.
-
Thermal Pyrolysis:
In summary, both catalytic and thermal pyrolysis have their unique advantages and challenges. The choice between the two depends on the specific application, feedstock, and desired outcomes. Catalytic pyrolysis offers greater control over product quality and efficiency but at a higher initial cost, while thermal pyrolysis is simpler and more cost-effective but may require additional processing to achieve desirable results.
Summary Table:
Aspect | Thermal Pyrolysis | Catalytic Pyrolysis |
---|---|---|
Temperature Range | 400–800°C | 300–600°C |
Energy Requirements | High | Lower |
Product Quality | Bio-oil with high oxygen content, less stable | High-quality bio-oil, lower oxygen content |
Feedstock Flexibility | Wide variety, but quality varies | Versatile, requires tailored catalysts |
Economic Cost | Lower initial cost, higher operational costs | Higher initial cost, lower operational cost |
Applications | Biochar, waste management, fuel production | High-value chemicals, biofuel production |
Discover the best pyrolysis method for your needs—contact our experts today for personalized guidance!