Chemical vapor deposition (CVD) is a sophisticated manufacturing process that involves depositing thin films of materials onto a substrate through chemical reactions in a vacuum environment. This process is widely used across various industries, including electronics, cutting tools, and solar cell manufacturing, due to its ability to produce high-quality, durable coatings. CVD involves several steps, such as transporting gaseous reactants to the substrate, surface adsorption, chemical reactions, and desorption of by-products. It is a versatile technique that can deposit a wide range of materials, including inorganic compounds and synthetic diamonds, making it essential for advanced material fabrication.
Key Points Explained:
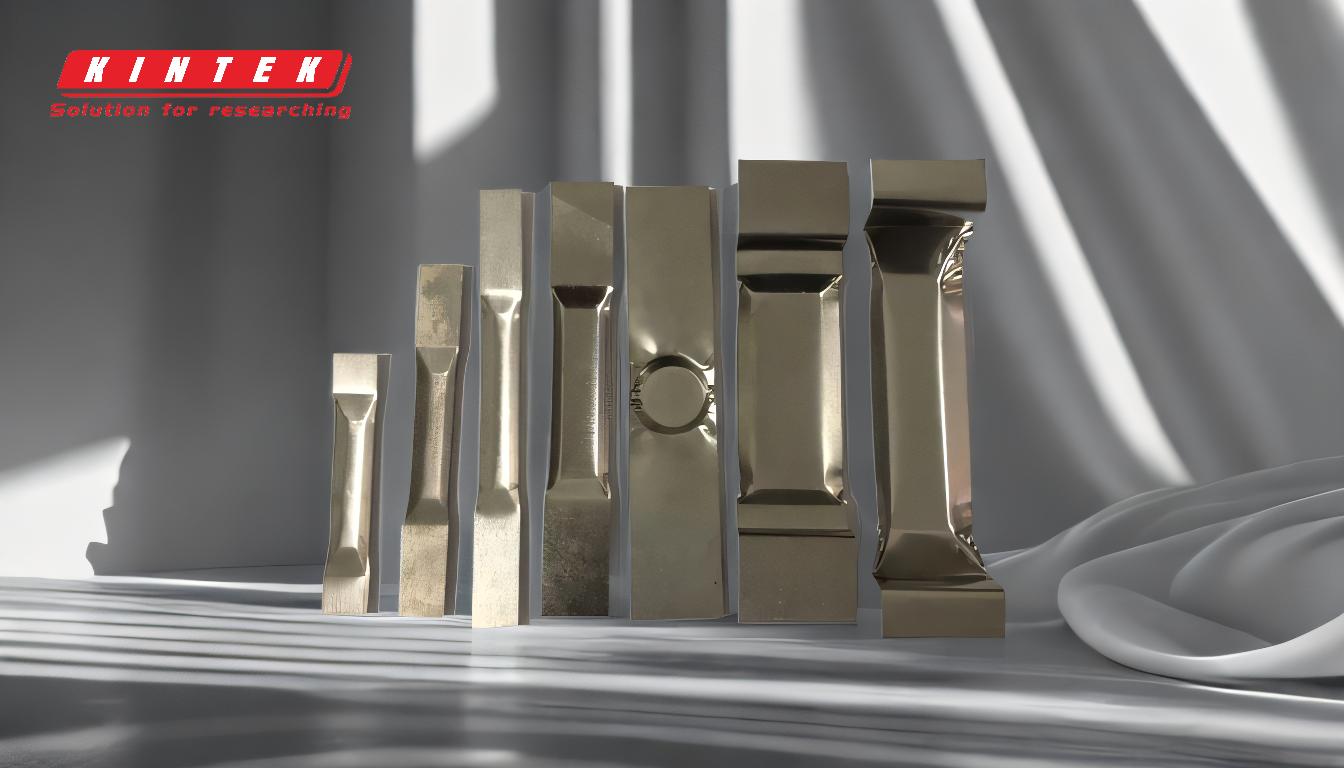
-
Definition and Purpose of CVD:
- Chemical vapor deposition (CVD) is a process used to deposit thin films of materials onto a substrate through chemical reactions in a controlled environment.
- It is widely used in industries like electronics, cutting tools, and solar cell manufacturing to create durable, high-performance coatings.
-
Steps Involved in CVD:
- Transport of Gaseous Reactants: The reacting gases are transported to the substrate surface in a vacuumed environment.
- Adsorption: The gaseous species adsorb onto the substrate surface.
- Chemical Reactions: Surface-catalyzed reactions occur, leading to the formation of the desired material.
- Nucleation and Growth: The material nucleates and grows into a thin film on the substrate.
- Desorption and By-product Removal: Gaseous by-products and unreacted species are desorbed and transported away from the surface.
-
Applications of CVD:
- Electronics: Used for depositing thin films on semiconductors, which are critical for integrated circuits and microelectronics.
- Cutting Tools: CVD coatings enhance the durability and wear resistance of cutting tools by preventing corrosion and wear.
- Solar Cells: CVD is employed to deposit photovoltaic materials on substrates for thin-film solar cells, improving energy efficiency.
-
Advantages of CVD:
- High-Quality Films: Produces uniform, high-purity, and durable thin films.
- Versatility: Capable of depositing a wide range of materials, including metals, ceramics, and synthetic diamonds.
- Scalability: Suitable for large-scale industrial applications due to its ability to coat complex geometries.
-
Challenges and Considerations:
- Complexity: Requires precise control of temperature, pressure, and gas flow rates.
- Skill Requirement: High level of expertise is needed to operate CVD equipment and optimize process parameters.
- Cost: The equipment and maintenance costs can be high, making it less accessible for small-scale applications.
-
Types of CVD Processes:
- Thermal CVD: Uses heat to drive the chemical reactions.
- Plasma-Enhanced CVD (PECVD): Utilizes plasma to enhance reaction rates at lower temperatures.
- Atomic Layer Deposition (ALD): A variant of CVD that allows for precise control of film thickness at the atomic level.
-
Historical and Modern Uses:
- Historically, CVD has been used for fabricating thin films of inorganic materials.
- Modern applications include the production of synthetic diamonds, advanced semiconductors, and energy-efficient solar cells.
By understanding the principles, steps, and applications of CVD, industries can leverage this technology to create innovative materials and products with enhanced performance and durability.
Summary Table:
Aspect | Details |
---|---|
Definition | A process to deposit thin films via chemical reactions in a vacuum. |
Key Steps | Transport, Adsorption, Reactions, Nucleation, Desorption. |
Applications | Electronics, Cutting Tools, Solar Cells. |
Advantages | High-quality films, versatility, scalability. |
Challenges | Requires precise control, high skill level, and significant costs. |
Types of CVD | Thermal CVD, Plasma-Enhanced CVD (PECVD), Atomic Layer Deposition (ALD). |
Discover how CVD can revolutionize your manufacturing process—contact our experts today!