CVD (Chemical Vapor Deposition) coating is a widely used technique for depositing thin films on substrates, offering advantages such as good repeatability and step coverage, making it suitable for various applications like dielectric, semiconductor, and metal films. However, it also has notable disadvantages, including high processing temperatures, which limit its use to high-temperature-resistant materials, and residual tensile stress that can make coated equipment fragile. Additionally, the high energy costs and challenges in depositing onto low melting point polymers further constrain its applicability. Despite these drawbacks, CVD remains a valuable method for specific industrial and material science applications.
Key Points Explained:
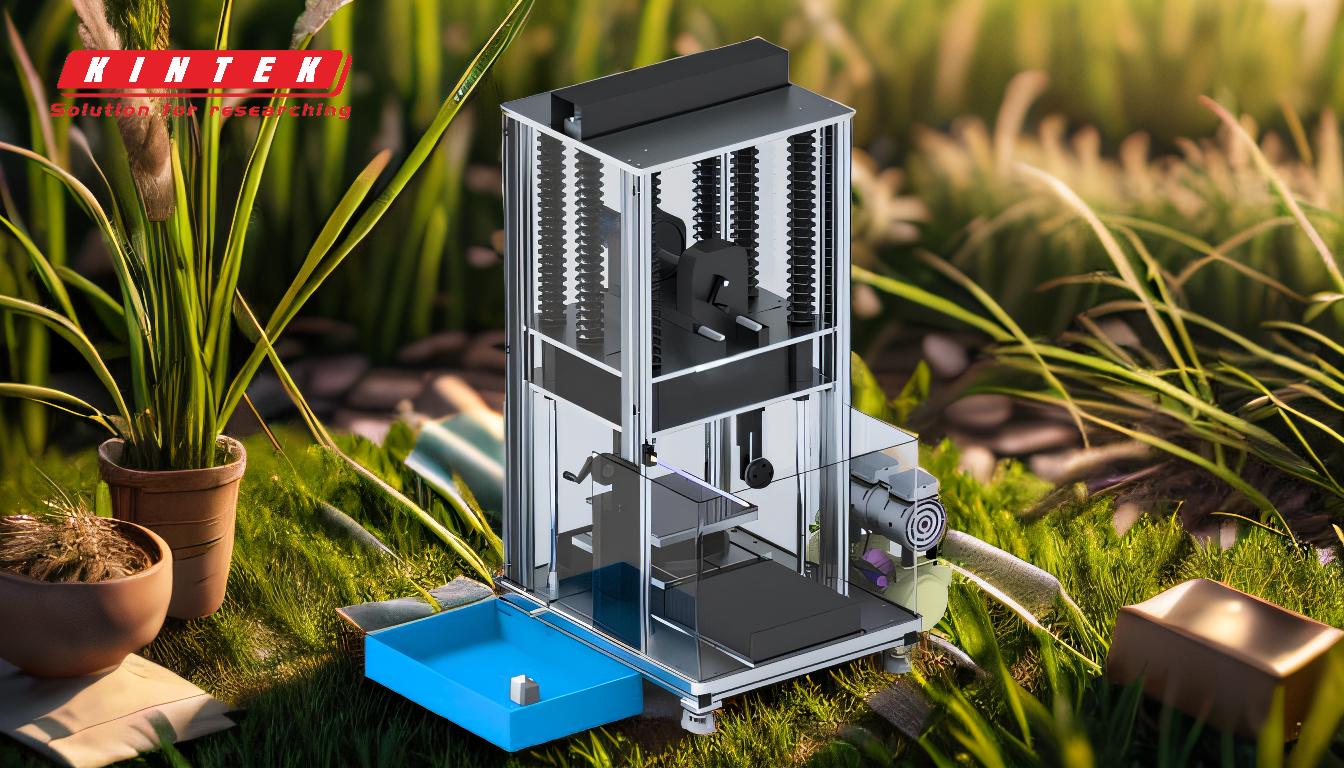
-
Advantages of CVD Coating:
- Good Repeatability and Step Coverage: CVD coating is known for its ability to produce consistent and uniform coatings, even on complex geometries. This makes it ideal for applications requiring precise and repeatable film deposition, such as in semiconductor manufacturing.
- Versatility in Material Deposition: CVD can deposit a wide range of materials, including dielectric films (e.g., SiO2, Si3N4), semiconductor films, metal films, and metal organic compounds. This versatility allows it to be used in various industries, from electronics to cutting tools.
-
Disadvantages of CVD Coating:
- High Processing Temperatures: CVD typically operates at high temperatures (800~1000 °C), which limits its use to materials that can withstand such conditions, like cemented carbide. This makes it unsuitable for low melting point polymers or other temperature-sensitive substrates.
- Residual Tensile Stress: The high temperatures involved in CVD can lead to residual tensile stress during cooling, which may cause fine cracks in the coating. These cracks can propagate under external impact, leading to coating failure, especially in applications like interrupted cutting processes (e.g., milling).
- Fragility of Coated Equipment: Due to the residual tensile stress, CVD-coated equipment tends to be more fragile compared to PVD (Physical Vapor Deposition)-coated equipment. This fragility can be a significant drawback in applications where mechanical durability is critical.
- High Energy Costs: The process of heating the gas phase to the required temperatures for CVD is energy-intensive, leading to higher operational costs. This can be a limiting factor for large-scale or cost-sensitive applications.
- Challenges with Low Melting Point Polymers: CVD is not well-suited for depositing onto low melting point polymers due to the high temperatures involved. This limits its applicability in certain industries, such as flexible electronics or polymer-based materials.
-
Applications and Limitations:
- Suitable Applications: CVD is particularly well-suited for applications requiring high-temperature-resistant materials and precise film deposition, such as in the semiconductor and cutting tool industries.
- Unsuitable Applications: Due to its high processing temperatures and the resulting residual stress, CVD is less suitable for applications involving interrupted cutting processes or materials with low melting points.
In summary, while CVD coating offers significant advantages in terms of repeatability, step coverage, and material versatility, its high processing temperatures, residual tensile stress, and associated fragility of coated equipment present notable disadvantages. These factors must be carefully considered when selecting CVD for specific applications.
Summary Table:
Aspect | Advantages | Disadvantages |
---|---|---|
Repeatability | Consistent and uniform coatings, ideal for complex geometries | High processing temperatures (800~1000 °C) limit material compatibility |
Step Coverage | Excellent for precise and repeatable film deposition | Residual tensile stress can cause fine cracks, leading to coating fragility |
Material Versatility | Deposits dielectric, semiconductor, metal films, and metal organic compounds | High energy costs due to energy-intensive heating processes |
Applications | Suitable for high-temperature-resistant materials and precise film deposition | Unsuitable for low melting point polymers or temperature-sensitive substrates |
Need help deciding if CVD coating is right for your application? Contact our experts today for tailored advice!