Deposition in semiconductor manufacturing is a critical process used to create thin or thick layers of materials on a substrate, atom-by-atom or molecule-by-molecule. This process is essential for producing high-quality, high-performance solid materials and thin films that are integral to semiconductor devices. Techniques such as High Density Plasma Chemical Vapor Deposition (HDP-CVD), plasma-enhanced CVD, and CVD tungsten are commonly employed to achieve precise and controlled deposition. These methods allow for the alteration of substrate properties, enabling the creation of complex semiconductor structures with specific electrical, thermal, and mechanical characteristics.
Key Points Explained:
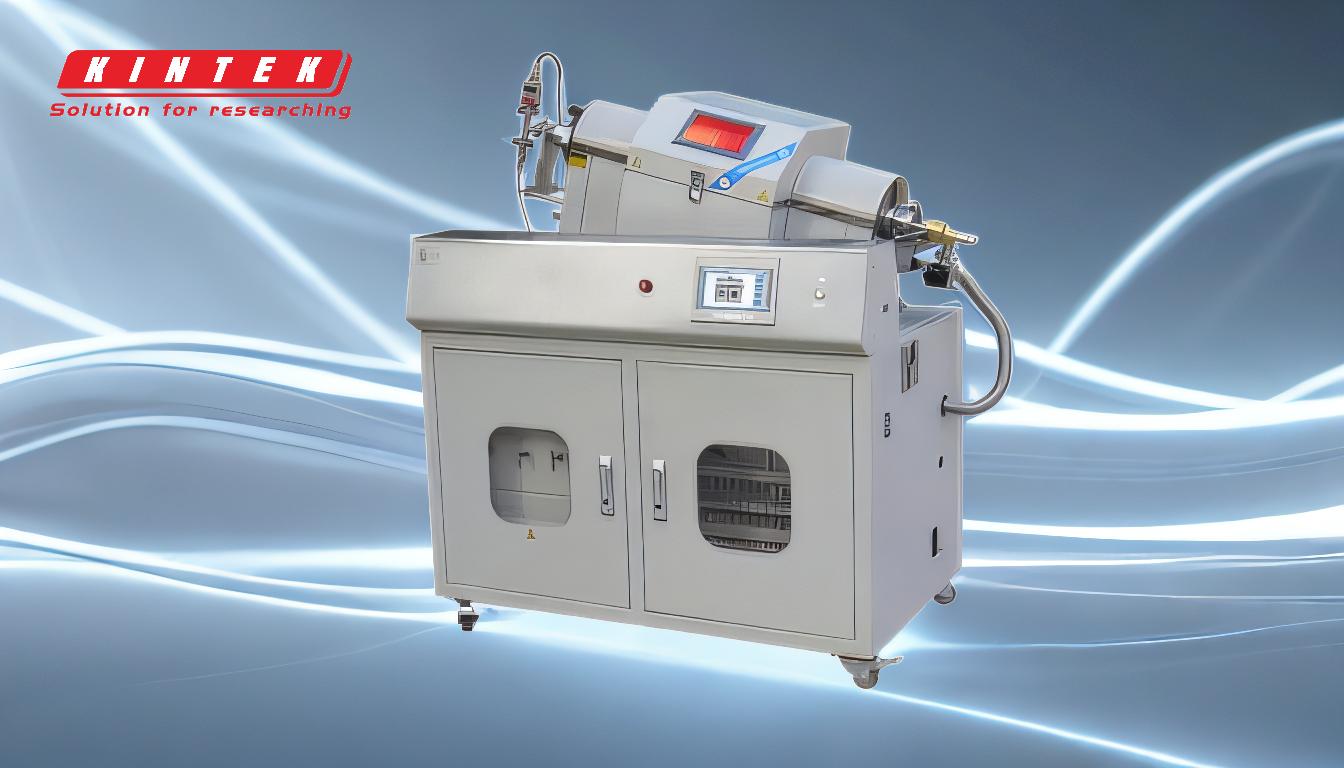
-
Definition of Deposition in Semiconductors:
- Deposition refers to the process of adding material layers onto a substrate in a controlled manner. In semiconductor fabrication, this is crucial for building the intricate layers that form the basis of electronic devices. The process can involve depositing conductive, insulating, or semiconducting materials, depending on the application.
-
Importance of Deposition in Semiconductor Fabrication:
- Deposition is a fundamental step in creating semiconductor devices. It allows for the precise formation of thin films, which are essential for the functionality of transistors, capacitors, and other components. The quality and uniformity of these films directly impact the performance and reliability of the final semiconductor product.
-
Common Deposition Techniques:
- High Density Plasma Chemical Vapor Deposition (HDP-CVD): This technique uses a high-density plasma to enhance the deposition rate and improve film quality. It is particularly useful for depositing dielectric materials in advanced semiconductor devices.
- Plasma-Enhanced CVD (PECVD): PECVD utilizes plasma to lower the temperature required for deposition, making it suitable for temperature-sensitive substrates. It is widely used for depositing silicon nitride and silicon dioxide films.
- CVD Tungsten: This method is specifically used for depositing tungsten layers, which are critical for creating interconnects in semiconductor devices. Tungsten is chosen for its excellent conductivity and ability to fill high-aspect-ratio structures.
-
Applications of Deposition in Semiconductors:
- Deposition processes are used in various stages of semiconductor manufacturing, including the creation of gate oxides, interlayer dielectrics, and metal interconnects. Each application requires specific deposition techniques to achieve the desired material properties and device performance.
-
Impact on Substrate Properties:
- The deposition process can significantly alter the properties of the substrate. For example, depositing a thin film of silicon dioxide can provide electrical insulation, while depositing a metal layer can create conductive pathways. The choice of deposition method and material directly influences the electrical, thermal, and mechanical characteristics of the semiconductor device.
By understanding and utilizing these deposition techniques, semiconductor manufacturers can produce devices with the precise characteristics needed for advanced electronic applications.
Summary Table:
Aspect | Details |
---|---|
Definition | Adding material layers onto a substrate in a controlled manner. |
Importance | Fundamental for creating high-quality thin films in semiconductor devices. |
Common Techniques | HDP-CVD, PECVD, CVD Tungsten |
Applications | Gate oxides, interlayer dielectrics, metal interconnects. |
Impact on Substrate | Alters electrical, thermal, and mechanical properties of the device. |
Discover how advanced deposition techniques can enhance your semiconductor manufacturing—contact our experts today!