E-beam evaporation synthesis of nano films is a specialized physical vapor deposition (PVD) technique used to create ultra-thin, high-purity coatings on substrates. The process involves using a high-energy electron beam to heat and evaporate a source material in a vacuum chamber. The evaporated particles then condense onto a substrate, forming a thin film with thicknesses typically ranging from 5 to 250 nanometers. This method is widely used in industries such as aerospace, electronics, and energy due to its ability to produce films with excellent purity, adhesion, and tailored properties like high temperature resistance, wear resistance, and specific optical characteristics.
Key Points Explained:
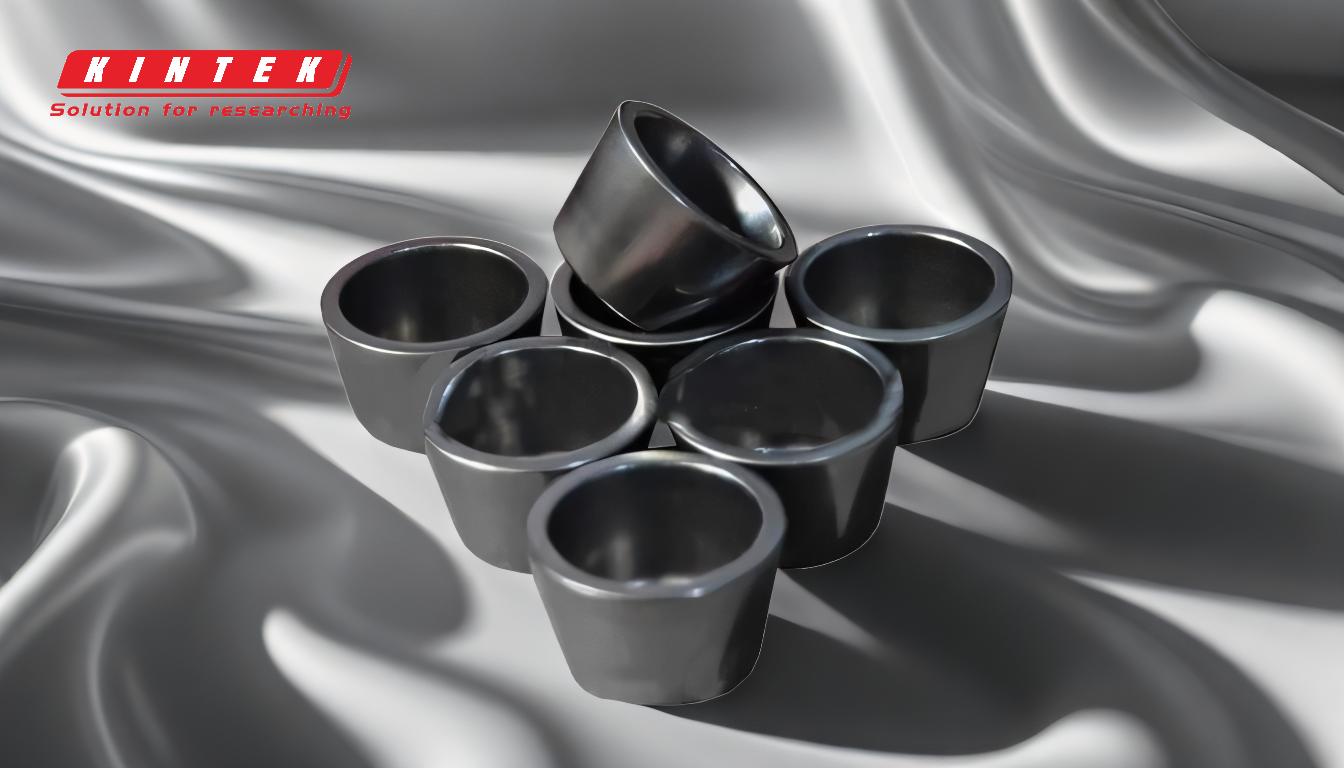
-
Mechanism of E-Beam Evaporation:
- The process begins with a high-energy electron beam directed at a source material, which is often placed in a crucible or water-cooled copper hearth.
- The electron beam generates intense heat, causing the source material to melt and evaporate.
- The evaporated particles travel upwards in the vacuum chamber and deposit onto a substrate positioned above the source material.
- This results in a thin, high-purity coating with precise thickness control, typically ranging from 5 to 250 nanometers.
-
Key Components of the Process:
- Electron Beam Source: A high-power electron beam is used to heat and evaporate the source material.
- Vacuum Chamber: The process takes place in a high-vacuum environment to minimize contamination and ensure high-purity coatings.
- Crucible or Hearth: The source material is placed in a crucible or water-cooled copper hearth to contain it during evaporation.
- Substrate: The material onto which the thin film is deposited, often positioned above the source material to allow for uniform coating.
-
Advantages of E-Beam Evaporation:
- High Purity: The vacuum environment and controlled heating process result in films with minimal impurities.
- Precision: The process allows for precise control over film thickness and uniformity.
- Material Versatility: E-beam evaporation can be used with a wide range of materials, including those with high melting points, such as gold and other refractory metals.
- Tailored Properties: The technique enables the creation of films with specific properties, such as high temperature resistance, wear resistance, and optical characteristics.
-
Applications of E-Beam Evaporation:
- Aerospace and Automotive: Used for coatings that require high temperature and wear resistance.
- Electronics: Ideal for creating conductive and insulating layers in electronic devices.
- Energy: Applied in the production of solar panels and other energy-related components.
- Optics: Used to create films with specific optical properties for lenses, mirrors, and other optical components.
- Consumer Goods: Applied in coatings for decorative and functional purposes.
-
Comparison with Other PVD Techniques:
- Unlike thermal evaporation, e-beam evaporation allows for the direct transfer of a larger amount of energy into the source material, making it suitable for materials with high melting points.
- The process does not require the source material to melt in the crucible, reducing the risk of contamination and improving film purity.
-
Process Control and Optimization:
- The thickness and properties of the deposited film can be controlled by adjusting parameters such as the electron beam power, vacuum level, and substrate temperature.
- The use of a water-cooled crucible or hearth helps to prevent overheating and contamination, ensuring consistent film quality.
-
Challenges and Considerations:
- Equipment Cost: E-beam evaporation systems can be expensive due to the need for high-power electron beam sources and vacuum chambers.
- Complexity: The process requires precise control over multiple parameters, making it more complex than some other thin-film deposition techniques.
- Material Limitations: While e-beam evaporation is versatile, some materials may still be challenging to deposit due to their properties or reactivity.
In summary, e-beam evaporation synthesis of nano films is a highly versatile and precise technique for creating thin, high-purity coatings with tailored properties. Its applications span a wide range of industries, making it a valuable tool for manufacturers looking to enhance the performance and functionality of their products.
Summary Table:
Aspect | Details |
---|---|
Mechanism | High-energy electron beam heats and evaporates source material in a vacuum. |
Key Components | Electron beam source, vacuum chamber, crucible/hearth, substrate. |
Advantages | High purity, precision, material versatility, tailored properties. |
Applications | Aerospace, electronics, energy, optics, consumer goods. |
Challenges | High equipment cost, process complexity, material limitations. |
Discover how e-beam evaporation can enhance your product performance—contact our experts today!