Electron beam coating is a sophisticated thin-film deposition technique that utilizes a focused beam of high-energy electrons to vaporize a target material, which then condenses onto a substrate to form a thin, uniform layer. This method is widely used in industries such as optics, electronics, and aerospace due to its ability to produce high-purity coatings with precise control over thickness and composition. The process involves generating an electron beam in a vacuum environment, directing it toward a target material, and depositing the vaporized material onto the substrate. This technique is particularly valued for its ability to coat complex geometries and create films with exceptional adhesion and durability.
Key Points Explained:
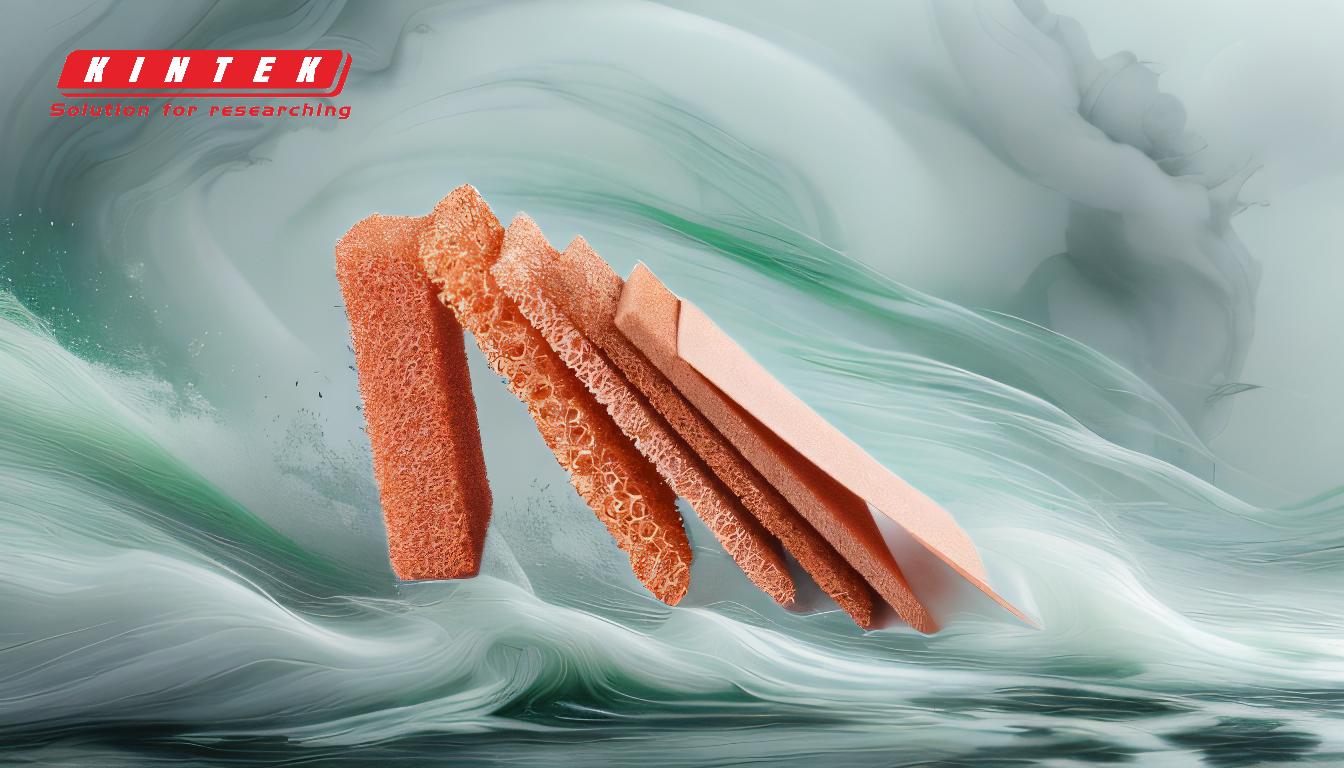
-
Definition and Purpose of Electron Beam Coating:
- Electron beam coating is a physical vapor deposition (PVD) method used to create thin, uniform layers of material on a substrate. It is primarily employed to enhance surface properties such as reflectivity, conductivity, corrosion resistance, and wear resistance. This technique is ideal for applications requiring high precision and high-quality coatings, such as in optical lenses, semiconductors, and aerospace components.
-
How Electron Beam Coating Works:
- The process begins in a vacuum chamber to eliminate contaminants and ensure high-purity deposition. An electron gun generates a focused beam of high-energy electrons, which is directed at a target material (e.g., metals, ceramics, or alloys). The energy from the electrons heats the target, causing it to vaporize. The vaporized material then travels through the vacuum and condenses onto the substrate, forming a thin, uniform coating.
-
Advantages of Electron Beam Coating:
- High Purity: The vacuum environment prevents contamination, resulting in coatings with exceptional purity.
- Precision: The process allows for precise control over coating thickness, often down to the nanometer level.
- Versatility: It can deposit a wide range of materials, including metals, ceramics, and composites.
- Adhesion and Durability: The coatings exhibit excellent adhesion to the substrate and are highly durable.
- Complex Geometries: The technique can coat intricate shapes and uneven surfaces effectively.
-
Applications of Electron Beam Coating:
- Optics: Used to create reflective and anti-reflective coatings for lenses, mirrors, and other optical components.
- Electronics: Applied in the production of thin-film transistors, sensors, and semiconductor devices.
- Aerospace: Enhances the performance and longevity of turbine blades, engine components, and other critical parts.
- Medical Devices: Provides biocompatible coatings for implants and surgical instruments.
- Decorative Coatings: Used to create aesthetically pleasing finishes on consumer products.
-
Comparison with Other Coating Techniques:
- Compared to methods like sputtering or thermal evaporation, electron beam coating offers higher deposition rates and better control over film properties. It is particularly advantageous for materials with high melting points, which are difficult to process using other techniques.
-
Challenges and Considerations:
- Equipment Cost: The specialized equipment required for electron beam coating can be expensive.
- Maintenance: The vacuum chamber and electron gun require regular maintenance to ensure optimal performance.
- Material Limitations: While versatile, the technique may not be suitable for all materials, particularly those that are sensitive to high-energy electron bombardment.
-
Future Trends in Electron Beam Coating:
- Advances in electron beam technology are expected to improve deposition rates, reduce costs, and expand the range of materials that can be coated. Additionally, integration with other deposition techniques, such as ion beam-assisted deposition, is likely to enhance coating performance and open up new applications.
By understanding the principles, advantages, and applications of electron beam coating, manufacturers and researchers can leverage this technology to develop high-performance materials and components for a wide range of industries.
Summary Table:
Aspect | Details |
---|---|
Definition | A PVD method using high-energy electrons to deposit thin, uniform coatings. |
Key Advantages | High purity, precision, versatility, adhesion, and durability. |
Applications | Optics, electronics, aerospace, medical devices, decorative coatings. |
Challenges | High equipment cost, maintenance, and material limitations. |
Future Trends | Improved deposition rates, cost reduction, and expanded material range. |
Unlock the potential of electron beam coating for your projects—contact our experts today!