End-of-life tyre pyrolysis is a recycling process that converts waste tires into valuable products such as fuel oil, carbon black, steel wire, and gas. This is achieved by heating waste tires in an oxygen-free environment within a pyrolysis reactor, breaking down the rubber into its constituent components. The process involves depolymerization, where the rubber's main chain cracks into smaller molecules, which then polymerize into various useful by-products. The resulting materials can be used for energy generation, industrial applications, or further processing. This method is environmentally significant as it reduces waste, provides renewable energy sources, and minimizes pollution.
Key Points Explained:
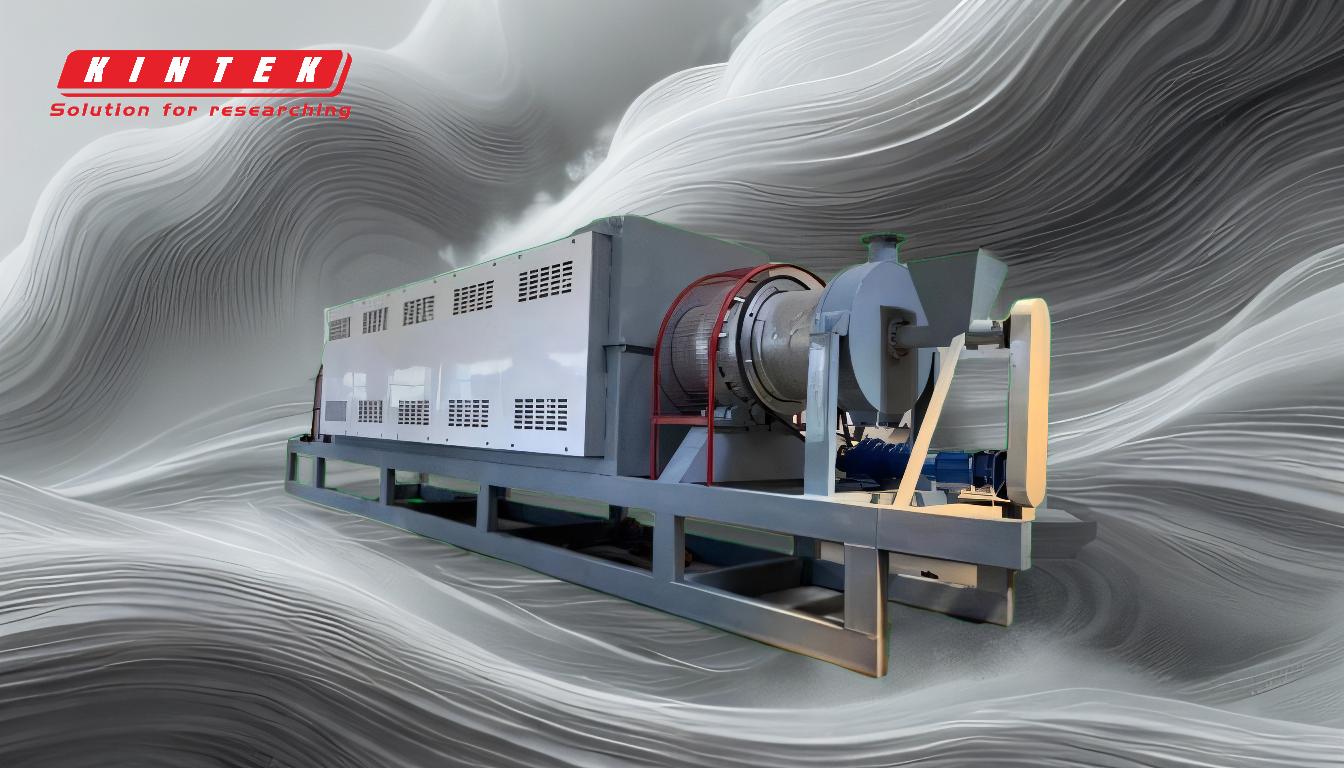
-
Definition of End-of-Life Tyre Pyrolysis:
- Pyrolysis is a thermal decomposition process that occurs in the absence of oxygen.
- End-of-life tyre pyrolysis specifically refers to the recycling of waste tires using this method.
- The process breaks down the complex rubber polymers in tires into simpler, reusable components.
-
Process Overview:
- Step 1: Preparation: Whole or shredded waste tires are loaded into a pyrolysis reactor.
- Step 2: Heating: The reactor is placed in a furnace and heated to high temperatures (typically 300-900°C) in an oxygen-free environment.
- Step 3: Depolymerization: The heat causes the rubber's main chain to crack into smaller molecules (monomers, biopolymers, and fragments).
- Step 4: Separation: The resulting gases are passed through a heat exchanger to separate condensable hydrocarbons (pyrolysis oil) from non-condensable gases.
- Step 5: Collection: The oil is collected for use as fuel, while the non-condensable gases are cleaned and stored for energy generation.
- Step 6: Recovery: Solid residues, such as carbon black and steel wire, are recovered for reuse.
-
Key Products:
- Pyrolysis Oil: A liquid fuel that can be used for heating, power generation, or as a feedstock for hydrogen production.
- Carbon Black: A fine powder used in manufacturing rubber products, inks, and coatings.
- Steel Wire: Recovered from the tires and reused in various industrial applications.
- Non-Condensable Gas: Cleaned and stored for use as a fuel source.
-
Environmental and Economic Benefits:
- Waste Reduction: Diverts end-of-life tires from landfills, reducing environmental pollution.
- Resource Recovery: Converts waste into valuable resources, promoting a circular economy.
- Energy Efficiency: Provides a renewable energy source, reducing reliance on fossil fuels.
- Pollution Control: Emits fewer pollutants compared to traditional tire disposal methods like incineration.
-
Factors Influencing the Process:
- Temperature: Higher temperatures generally increase the yield of gas and oil but may affect the quality of carbon black.
- Reactor Design: The efficiency of the pyrolysis process depends on the reactor's ability to maintain uniform heating and oxygen-free conditions.
- Feedstock Quality: The composition and size of the tires can influence the type and quality of the end products.
-
Applications of Pyrolysis Products:
- Pyrolysis Oil: Used as a substitute for diesel or heavy fuel oil in industrial boilers and furnaces.
- Carbon Black: Used in the production of new tires, rubber goods, and as a pigment in inks and paints.
- Steel Wire: Recycled into new steel products or used in construction.
- Non-Condensable Gas: Used to power the pyrolysis plant itself, making the process self-sustaining.
-
Challenges and Considerations:
- Energy Consumption: The process requires significant energy input, which can affect its overall sustainability.
- Emission Control: Proper handling of gases and residues is essential to minimize environmental impact.
- Economic Viability: The profitability of the process depends on the market demand for the end products and the cost of operation.
By understanding these key points, a purchaser of equipment or consumables for tyre pyrolysis can make informed decisions about the technology, its benefits, and its applications. This knowledge also helps in evaluating the feasibility and environmental impact of implementing such a system.
Summary Table:
Key Aspect | Details |
---|---|
Process | Thermal decomposition of tires in an oxygen-free environment. |
Key Products | Pyrolysis oil, carbon black, steel wire, and non-condensable gas. |
Environmental Benefits | Reduces waste, provides renewable energy, and minimizes pollution. |
Applications | Energy generation, industrial use, and manufacturing of rubber products. |
Challenges | Energy consumption, emission control, and economic viability. |
Ready to explore tyre pyrolysis solutions? Contact us today for expert guidance!