Film thickness uniformity refers to the consistency of a thin film's thickness across a substrate, ensuring that the film's properties, such as electrical, mechanical, and optical characteristics, are evenly distributed. It is a critical factor in industries like semiconductors, displays, and medical devices, as it directly impacts product performance. Achieving uniformity involves controlling deposition processes and optimizing geometric and environmental parameters. The uniform area is typically defined as the region where thickness variation is less than 5%. Understanding the application's requirements is essential to avoid over- or under-specifying uniformity, ensuring optimal performance and cost-effectiveness.
Key Points Explained:
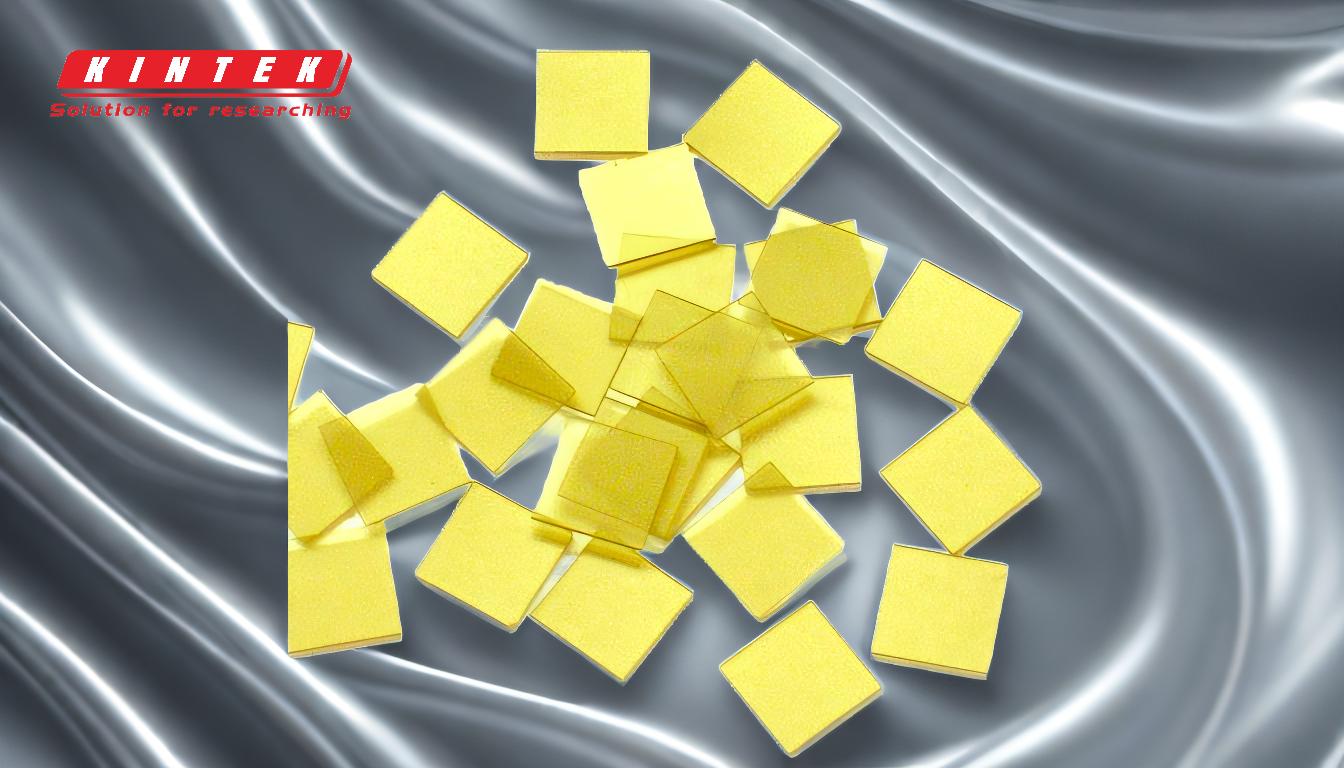
-
Definition of Film Thickness Uniformity:
- Film thickness uniformity refers to the consistency of a thin film's thickness across a substrate. This uniformity ensures that the film's properties, such as electrical conductivity, mechanical strength, and optical performance, are evenly distributed.
- Uniformity is critical in industries like semiconductors, displays, and medical devices, where even minor variations in film thickness can significantly impact product performance.
-
Importance of Uniformity:
- Uniformity affects the electrical, mechanical, and optical properties of thin films. For example, in semiconductor manufacturing, non-uniform film thickness can lead to inconsistent electrical performance, while in optical coatings, it can cause variations in light transmission or reflection.
- Achieving uniformity is essential for ensuring consistent and reproducible product quality, which is crucial for industrial applications.
-
Measurement of Film Thickness:
- Thin film thickness is typically measured using optical interference methods. Light is reflected from the top and bottom interfaces of the film, and the interference pattern is analyzed to determine the thickness.
- The refractive index of the material is also a critical factor in these measurements, as different materials have different refractive indexes, affecting the interference pattern.
-
Uniform Area Definition:
- The uniform area is defined as the region on the substrate where the thin film thickness has less than 5% non-uniformity. This means that the thickness variation within this area is minimal, ensuring consistent film properties.
- The percentage length is calculated as the ratio between the length of the uniform deposition zone on the substrate and the total substrate length.
-
Factors Affecting Uniformity:
- Geometric Parameters: In processes like magnetron sputtering, factors such as target-substrate distance, ion energy, target erosion area, temperature, and gas pressure can significantly affect film thickness uniformity.
- Process Control: Achieving consistent and reproducible thin film characteristics requires precise control over deposition processes. This includes optimizing parameters like substrate rotation, the number of satellite holders, and the initial position of the substrate face.
- Chamber Design: The design of the deposition chamber, including the space occupied by satellites and the overall chamber area, can also impact the homogeneity of the coatings.
-
Optimization Techniques:
- To improve uniformity, it is essential to optimize the deposition process. This can involve adjusting the rotation of substrates and holders, increasing the number of satellite holders, and carefully positioning the substrate face within the chamber.
- Understanding the specific requirements of the application is crucial to avoid over- or under-specifying uniformity, ensuring that the film meets performance standards without unnecessary costs.
-
Application-Specific Considerations:
- Different applications may have varying requirements for film thickness uniformity. For example, in semiconductor manufacturing, extremely high uniformity is often required to ensure consistent electrical properties, while in some optical applications, slightly higher variations may be acceptable.
- It is important to tailor the deposition process and uniformity specifications to the specific needs of the application, balancing performance requirements with cost considerations.
By understanding and controlling these factors, manufacturers can achieve the desired film thickness uniformity, ensuring that their products meet the necessary performance standards and deliver consistent quality.
Summary Table:
Aspect | Details |
---|---|
Definition | Consistency of thin film thickness across a substrate. |
Importance | Ensures even distribution of electrical, mechanical, and optical properties. |
Measurement | Optical interference methods, considering material refractive index. |
Uniform Area | Region with <5% thickness variation. |
Key Factors | Geometric parameters, process control, and chamber design. |
Optimization Techniques | Adjust substrate rotation, increase satellite holders, and optimize chamber design. |
Applications | Semiconductors, displays, medical devices, and optical coatings. |
Achieve perfect film thickness uniformity for your applications—contact our experts today!