Powder metallurgy (PM) is a versatile and efficient manufacturing process with numerous advantages, such as high precision, cost-effectiveness, and minimal material waste. However, it also has several limitations and disadvantages that can impact its suitability for certain applications. These include size restrictions due to press capacity, challenges in producing complex shapes, and lower mechanical strength and ductility compared to traditional methods like casting or forging. Additionally, secondary finishing processes may be required, adding time and cost to production. Understanding these limitations is crucial for selecting the right manufacturing method for specific applications.
Key Points Explained:
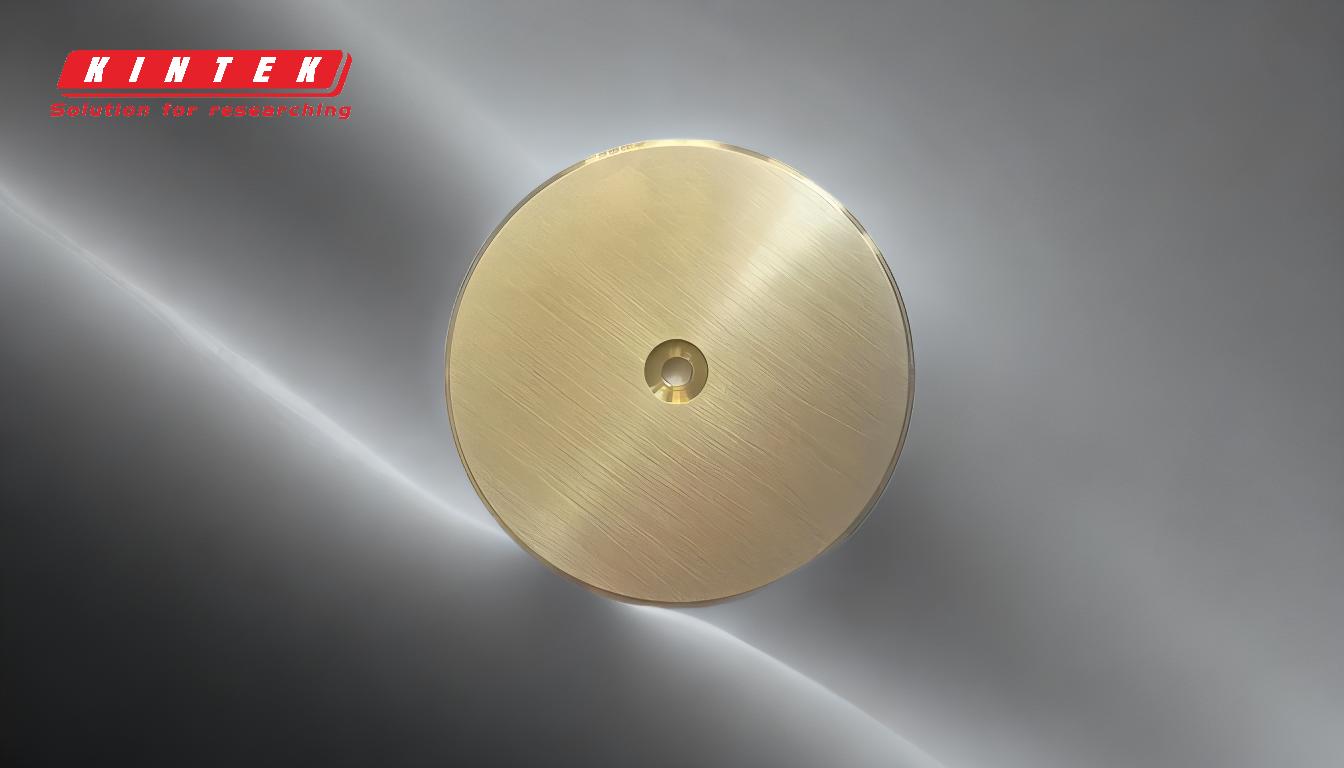
-
Size Limitations:
- Explanation: The size of parts produced through powder metallurgy is constrained by the capacity of the presses used in the process. The largest presses available in the industry are about 1,500 tons, which limits the practical planar area of parts to approximately 40-50 square inches. This makes PM less suitable for manufacturing large components.
- Implications: For industries requiring large parts, such as heavy machinery or large-scale construction, powder metallurgy may not be feasible. Alternative methods like casting or forging might be necessary.
-
Challenges with Complex Shapes:
- Explanation: Producing complex-shaped parts can be difficult with powder metallurgy. While skilled manufacturers can overcome some of these challenges, the process inherently struggles with intricate geometries compared to other manufacturing methods.
- Implications: For applications requiring highly complex or intricate designs, additional machining or secondary processes may be needed, increasing production time and costs.
-
Lower Mechanical Strength and Ductility:
- Explanation: PM parts generally do not achieve the same level of strength or ductility as parts produced through casting or forging. This is due to the inherent porosity and microstructure of PM materials.
- Implications: In applications where high mechanical performance is critical, such as in aerospace or automotive structural components, PM may not be the best choice. Engineers must carefully consider material properties when selecting manufacturing methods.
-
Secondary Finishing Requirements:
- Explanation: Powder metallurgy often requires secondary finishing processes to achieve the desired surface quality and dimensional accuracy. This can include machining, grinding, or coating.
- Implications: The need for secondary finishing adds to the overall production time and cost, which can be a disadvantage for projects with tight budgets or deadlines.
-
Material Limitations:
- Explanation: While powder metallurgy is versatile and can be used with a wide range of metals, there are still some limitations. Certain materials may not be suitable for PM due to their properties or the complexity of the required processing.
- Implications: Material selection is crucial, and some high-performance alloys or specialized materials may not be feasible for PM, limiting its application in certain high-tech industries.
-
Economic Considerations:
- Explanation: Although PM is generally cost-effective for high-volume production, the initial setup costs for tooling and equipment can be high. Additionally, the need for secondary finishing can further increase costs.
- Implications: For low-volume or custom production runs, the economic benefits of PM may not be as pronounced, making other manufacturing methods more attractive.
In summary, while powder metallurgy offers many advantages, including precision, efficiency, and material savings, it also has significant limitations. These include size constraints, challenges with complex shapes, lower mechanical properties, secondary finishing requirements, material limitations, and economic considerations. Understanding these factors is essential for making informed decisions about the use of powder metallurgy in various manufacturing applications.
Summary Table:
Limitation | Explanation | Implications |
---|---|---|
Size Limitations | Press capacity limits part size to ~40-50 square inches. | Not suitable for large components; alternatives like casting/forging required. |
Complex Shapes | Struggles with intricate geometries. | Additional machining or secondary processes may be needed, increasing costs. |
Lower Mechanical Strength | PM parts have lower strength/ductility due to porosity. | Unsuitable for high-performance applications like aerospace or automotive. |
Secondary Finishing | Requires additional processes like machining or coating. | Adds time and cost to production, impacting tight budgets or deadlines. |
Material Limitations | Some materials are unsuitable due to properties or processing complexity. | Limits application in high-tech industries requiring specialized materials. |
Economic Considerations | High initial setup costs and secondary finishing increase expenses. | Less cost-effective for low-volume or custom production runs. |
Need help choosing the right manufacturing method? Contact our experts today to discuss your project!