Chemical vapor deposition (CVD) is a material processing technique used to create thin, high-quality coatings or films on a substrate through chemical reactions in the vapor phase. The process involves introducing volatile precursor chemicals into a reaction chamber, where they decompose or react at elevated temperatures and low pressures to form a solid film on the substrate surface. CVD is widely used in industries such as semiconductors, optics, and energy storage due to its ability to produce uniform, high-purity coatings with precise control over thickness and composition. However, it requires sophisticated equipment and controlled conditions, making it less suitable for large-scale production. The process includes steps such as precursor transport, surface adsorption, chemical reactions, film growth, and by-product removal.
Key Points Explained:
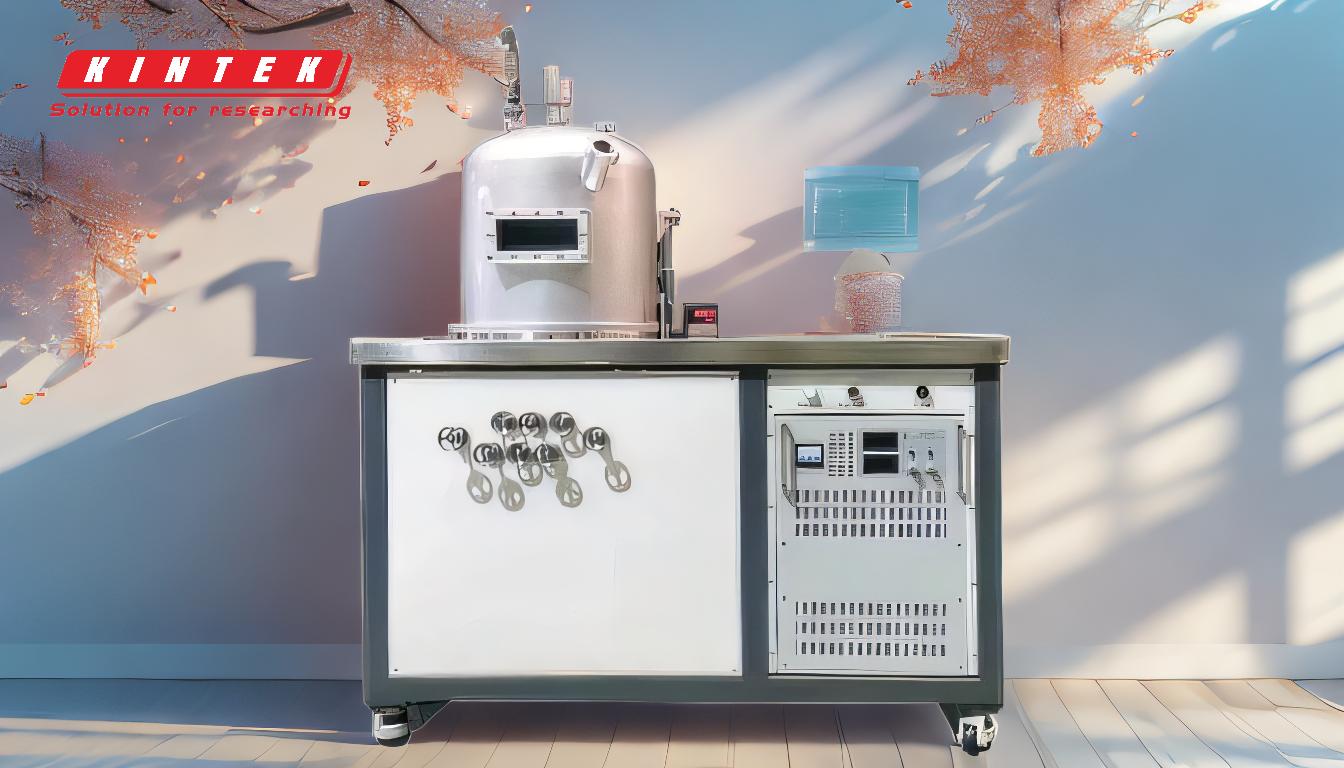
-
Definition of Chemical Vapor Deposition (CVD):
- CVD is a process used to deposit thin films or coatings on a substrate by utilizing chemical reactions in the vapor phase.
- It involves the use of volatile precursor chemicals that react or decompose under controlled conditions to form a solid film on the substrate.
-
Key Steps in the CVD Process:
- Precursor Introduction: Volatile precursor chemicals are introduced into the reaction chamber, often under vacuum or low-pressure conditions.
- Transport and Diffusion: The precursor molecules are transported to the substrate surface through fluid flow and diffusion.
- Surface Adsorption: The precursor molecules adsorb onto the substrate surface, where they remain long enough to undergo chemical reactions.
- Chemical Reactions: The adsorbed molecules react or decompose, forming a solid film on the substrate surface.
- By-product Removal: Volatile by-products desorb from the surface and are removed from the reaction chamber.
-
Conditions Required for CVD:
- Heat: Elevated temperatures are required to activate the chemical reactions or decomposition of the precursors.
- Low Pressure: CVD is often conducted under vacuum or low-pressure conditions to ensure uniform deposition and minimize contamination.
- Controlled Atmosphere: The reaction chamber is filled with the precursor gases and sometimes additional reactive gases to facilitate the desired chemical reactions.
-
Advantages of CVD:
- High-Quality Films: CVD produces uniform, high-purity coatings with precise control over thickness and composition.
- Versatility: It can deposit a wide range of materials, including metals, ceramics, and semiconductors.
- Environmental Friendliness: Some CVD processes, such as those using glucose as a precursor, are environmentally friendly and controllable.
-
Limitations of CVD:
- High Cost: The need for sophisticated equipment and controlled conditions makes CVD expensive.
- Slow Deposition Rates: The decomposition rate of precursors is often slow, leading to longer production times.
- Scalability Issues: CVD is less suitable for large-scale production due to its complexity and cost.
-
Applications of CVD:
- Semiconductors: CVD is widely used in the semiconductor industry to deposit thin films for integrated circuits and transistors.
- Optics: It is used to create anti-reflective coatings and other optical films.
- Energy Storage: CVD can enhance the performance of materials used in batteries and fuel cells, such as the carbon coating on LiFePO4 for improved rate capacity and cycling lifetime.
-
Example of CVD in Action:
- In one study, researchers used CVD to coat carbon on LiFePO4 by heating solid glucose in a quartz tube to 550 °C. The glucose decomposed into vapor, which condensed as small carbon clusters on the LiFePO4 surface, resulting in a uniform carbon layer that improved the material's performance in energy storage applications.
By understanding these key points, one can appreciate the complexity and precision of the CVD process, as well as its potential and limitations in various industrial applications.
Summary Table:
Aspect | Details |
---|---|
Definition | CVD is a process to deposit thin films via chemical reactions in the vapor phase. |
Key Steps | Precursor introduction, transport, adsorption, reactions, by-product removal. |
Required Conditions | Heat, low pressure, controlled atmosphere. |
Advantages | High-quality films, versatility, environmental friendliness. |
Limitations | High cost, slow deposition rates, scalability issues. |
Applications | Semiconductors, optics, energy storage. |
Discover how CVD can elevate your material processing—contact our experts today!