Molds in manufacturing are essential tools used to shape materials into desired forms. They are cavities or matrices into which fluid or plastic substances, such as molten metal or plastic, are poured or forced. Once the material hardens, it takes the shape of the mold, resulting in a finished product. Molds are widely used in industries like automotive, aerospace, electronics, and consumer goods to produce components with precision and consistency. Their design and material depend on the manufacturing process, the material being molded, and the desired properties of the final product.
Key Points Explained:
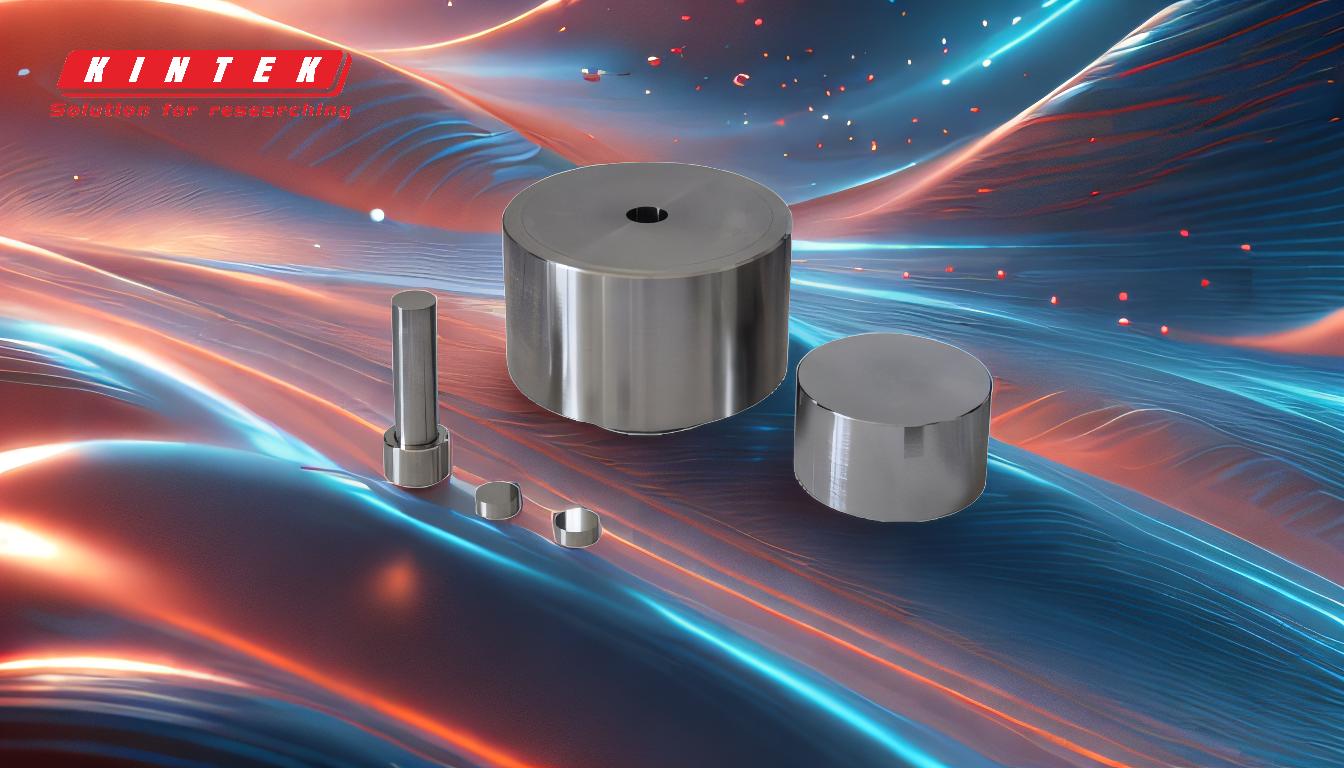
-
Definition of a Mold
- A mold is a cavity or matrix designed to shape a fluid or plastic substance into a specific form.
- It acts as a template for the final product, ensuring consistency and precision in manufacturing.
-
Materials Used in Molds
- Molds are typically made from durable materials like steel, aluminum, or ceramics, depending on the manufacturing process and the material being molded.
- The choice of mold material affects its durability, heat resistance, and ability to produce high-quality finishes.
-
Types of Molds
- Injection Molds: Used in plastic manufacturing, where molten plastic is injected into the mold cavity.
- Die-Casting Molds: Used for metals, where molten metal is forced into the mold under high pressure.
- Compression Molds: Used for materials like rubber or thermosetting plastics, where the material is compressed into the mold.
- Blow Molds: Used for creating hollow objects, such as bottles, by blowing air into a heated plastic tube inside the mold.
-
Applications of Molds in Manufacturing
- Molds are used across various industries, including automotive (e.g., engine components, dashboards), aerospace (e.g., turbine blades), electronics (e.g., casings), and consumer goods (e.g., toys, containers).
- They enable mass production of complex parts with high accuracy and repeatability.
-
Advantages of Using Molds
- Precision: Molds allow for the creation of intricate designs and tight tolerances.
- Efficiency: They enable high-volume production with minimal waste.
- Consistency: Each product produced using the same mold is identical, ensuring uniformity.
- Cost-Effectiveness: While the initial cost of mold design and fabrication can be high, the per-unit cost decreases with large-scale production.
-
Challenges in Mold Manufacturing
- Design Complexity: Creating molds for complex geometries requires advanced engineering and machining.
- Material Selection: Choosing the right mold material is critical to withstand high temperatures, pressures, and wear.
- Maintenance: Molds require regular maintenance to prevent defects and ensure longevity.
- Cost: High-quality molds can be expensive to produce, making them more suitable for large-scale manufacturing.
-
Future Trends in Mold Manufacturing
- Additive Manufacturing: 3D printing is being used to create molds with complex geometries and reduced lead times.
- Smart Molds: Integration of sensors and IoT technology to monitor mold conditions and improve quality control.
- Sustainable Materials: Development of eco-friendly mold materials to reduce environmental impact.
By understanding the role of molds in manufacturing, purchasers can make informed decisions about the types of molds needed for their specific applications, ensuring optimal performance and cost-effectiveness.
Summary Table:
Aspect | Details |
---|---|
Definition | Cavities or matrices used to shape fluid or plastic substances into forms. |
Materials | Steel, aluminum, ceramics—chosen for durability, heat resistance, and finish. |
Types | Injection, die-casting, compression, and blow molds. |
Applications | Automotive, aerospace, electronics, and consumer goods industries. |
Advantages | Precision, efficiency, consistency, and cost-effectiveness. |
Challenges | Design complexity, material selection, maintenance, and high initial costs. |
Future Trends | Additive manufacturing, smart molds, and sustainable materials. |
Ready to optimize your manufacturing process with precision molds? Contact our experts today to discuss your needs!