PECVD (Plasma-Enhanced Chemical Vapor Deposition) silicon deposition is a process that utilizes plasma to enable chemical reactions and deposit thin films of silicon at relatively low temperatures. This method is particularly advantageous for applications requiring high-quality films with excellent electrical properties, good adhesion, and step coverage. The process involves using a glow-discharge plasma excited by an RF field, which operates at reduced gas pressures. PECVD is widely used in industries such as very large-scale integrated circuits, optoelectronic devices, and MEMS due to its low-temperature operation, high productivity, and cost-effectiveness.
Key Points Explained:
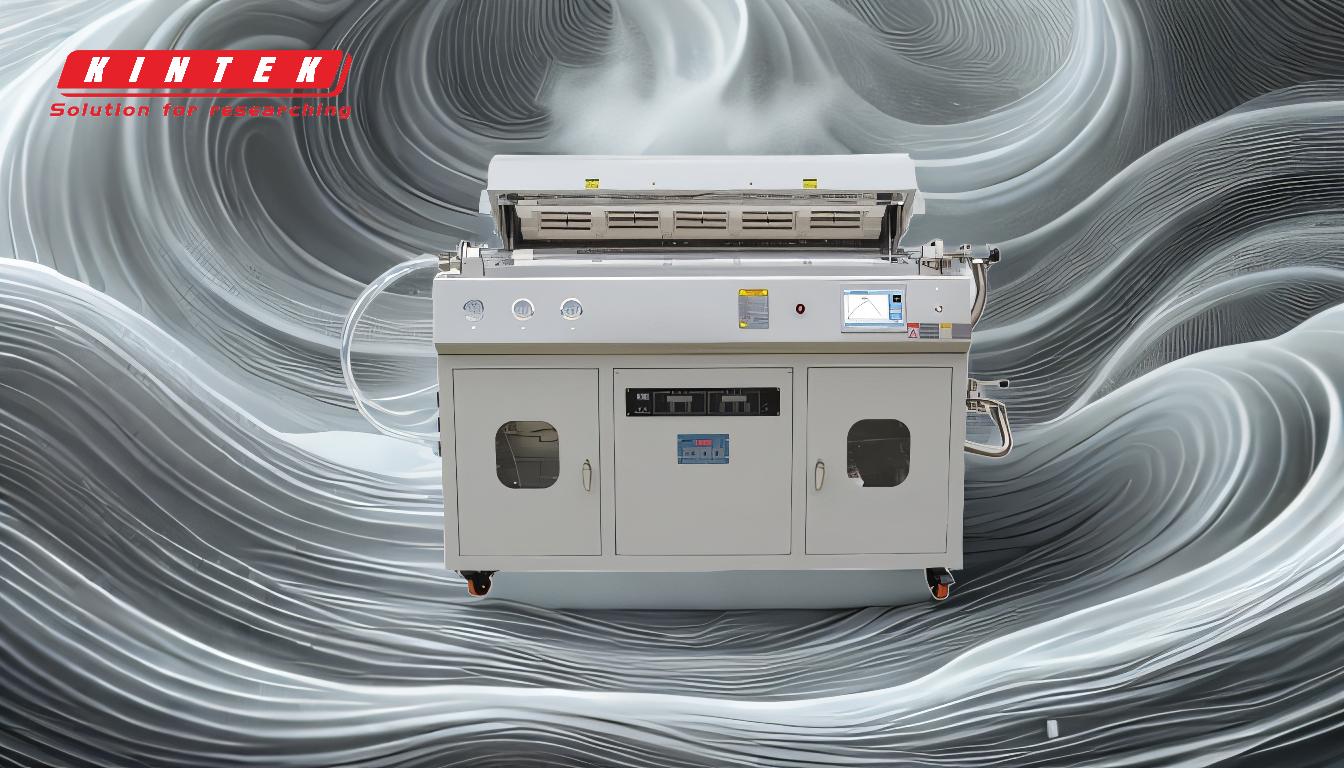
-
Definition and Mechanism of PECVD Silicon Deposition:
- PECVD is a process that uses plasma to facilitate chemical reactions for depositing silicon thin films. The plasma is typically excited by an RF field, which ionizes the gas molecules, creating reactive species that enable deposition at lower temperatures compared to traditional CVD methods.
- The process operates in a reduced gas pressure environment (50 mtorr to 5 torr), where electron and positive ion densities range from 10^9 to 10^11/cm^3, and average electron energies range from 1 to 10 eV.
-
Advantages of PECVD Silicon Deposition:
- Low-Temperature Deposition: PECVD allows for deposition at much lower temperatures, reducing thermal damage to the substrate and making it suitable for temperature-sensitive materials.
- High Productivity: The fast deposition rate of PECVD improves production efficiency, making it a preferred choice for high-volume manufacturing.
- In-Situ Doping: PECVD enables doping directly during the deposition process, simplifying the overall manufacturing process.
- Cost-Effectiveness: Compared to other methods like LPCVD, PECVD can be more cost-effective in certain applications, reducing both material and operating costs.
-
Applications of PECVD Silicon Deposition:
- Very Large-Scale Integrated Circuits (VLSI): PECVD is used to deposit high-quality silicon films with excellent electrical properties, which are crucial for the performance of VLSI.
- Optoelectronic Devices: The good substrate adhesion and step coverage of PECVD films make them ideal for optoelectronic devices.
- MEMS (Micro-Electro-Mechanical Systems): PECVD's ability to deposit films at low temperatures is particularly beneficial for MEMS applications, where thermal damage to the substrate must be minimized.
-
Components of a PECVD Deposition System:
- Radio Frequency Power Supply: This component ionizes the reactive gas, creating the plasma necessary for the deposition process.
- Water Cooling System: Provides cooling for various pumps and other components to maintain the system's temperature during operation.
- Substrate Heating Device: Heats the sample to the required temperature and helps remove impurities, ensuring high-quality film deposition.
In summary, PECVD silicon deposition is a versatile and efficient method for depositing high-quality silicon films at low temperatures. Its advantages, such as low-temperature operation, high productivity, and cost-effectiveness, make it a preferred choice for various industrial applications, including VLSI, optoelectronic devices, and MEMS. The system's components, including the RF power supply, water cooling system, and substrate heating device, work together to ensure optimal performance and film quality.
Summary Table:
Aspect | Details |
---|---|
Definition | Uses plasma to deposit silicon films at low temperatures. |
Advantages | Low-temperature deposition, high productivity, in-situ doping, cost-effective. |
Applications | VLSI, optoelectronic devices, MEMS. |
Key Components | RF power supply, water cooling system, substrate heating device. |
Interested in how PECVD silicon deposition can benefit your project? Contact our experts today!