Physical Vapor Deposition (PVD) is a versatile coating technique used across various industries to apply thin films with specific mechanical, optical, chemical, or electronic properties. It is widely employed in aerospace for temperature-resistant coatings, in semiconductor manufacturing for optical films, and in tooling for hard, corrosive-resistant coatings. PVD is also used in the production of reflective films, food packaging materials, and biomedical devices. The process enhances durability, resistance to extreme conditions, and performance of materials, making it indispensable in industries requiring high-performance coatings.
Key Points Explained:
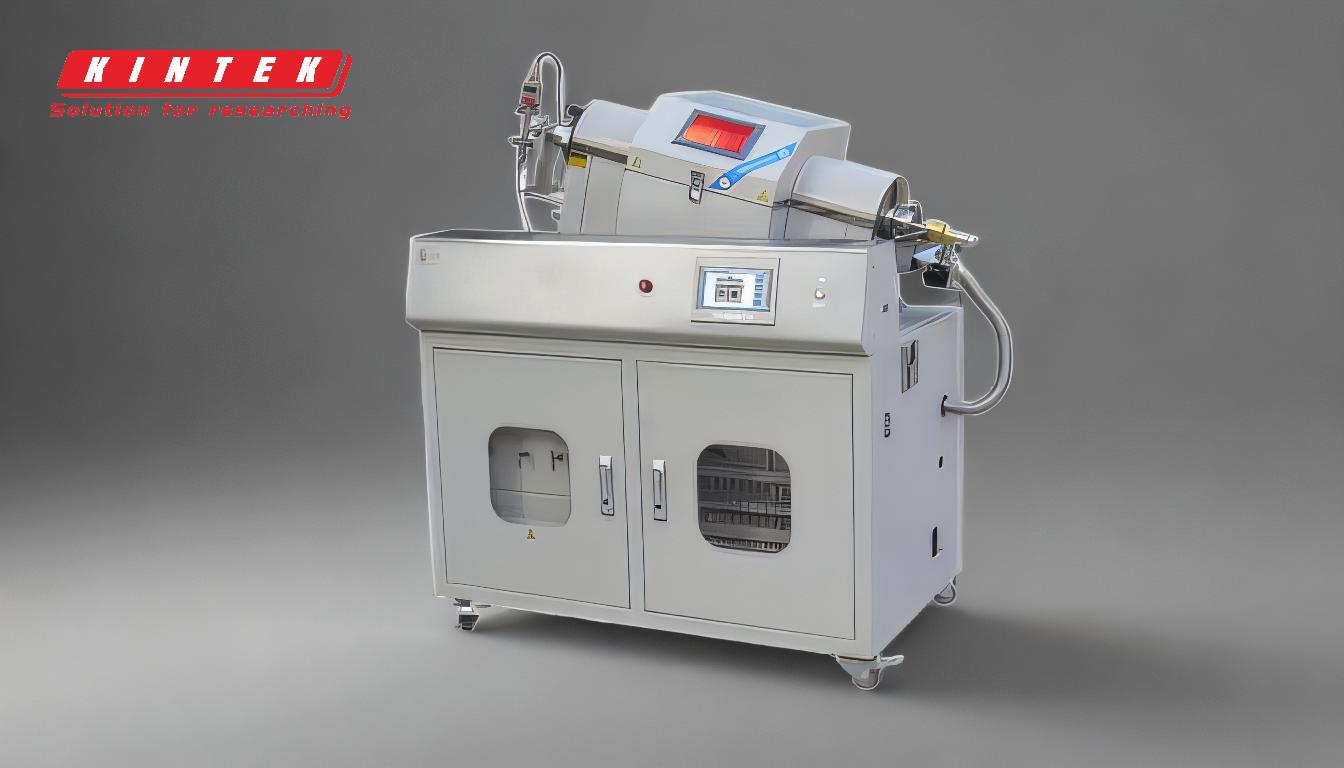
-
Aerospace Industry Applications:
- PVD is used to apply dense, temperature-resistant coatings to aerospace components.
- These coatings enhance the ability of components to withstand extreme temperatures and improve durability.
- Example: E-beam evaporation is a common PVD technique used in aerospace for such applications.
-
Semiconductor and Optical Applications:
- PVD is crucial in the manufacture of semiconductor devices, such as thin-film solar panels.
- It is used to apply optical films that improve the efficiency and functionality of solar panels and other optical devices.
- Example: E-beam evaporation is employed to deposit optical films on semiconductors.
-
Tooling and Industrial Applications:
- PVD is used to apply hard, corrosive-resistant coatings to cutting tools and other industrial products.
- These coatings protect tools from wear and extend their lifespan in harsh environments.
- Example: Titanium nitride coatings applied via PVD are commonly used in metalworking tools.
-
Decorative and Reflective Coatings:
- PVD is used to produce highly reflective films and decorative coatings.
- These coatings are used in various applications, including mirrors, architectural glass, and consumer electronics.
- Example: Aluminized PET film created using PVD is used in food packaging and balloons.
-
Biomedical Applications:
- PVD is employed in the biomedical field to coat medical devices and implants.
- These coatings can improve biocompatibility, reduce wear, and enhance the performance of biomedical devices.
- Example: PVD coatings are used on surgical instruments and orthopedic implants.
-
Food Packaging:
- PVD is used to create thin, barrier films for food packaging.
- These films help in preserving the freshness and extending the shelf life of food products.
- Example: Aluminized PET film produced via PVD is widely used in food packaging.
-
General Industrial Coatings:
- PVD is used to apply various types of coatings that improve the hardness, wear resistance, and corrosion resistance of materials.
- These coatings are essential in industries where materials are subjected to demanding applications.
- Example: PVD coatings are used in the manufacturing of cutting tools, molds, and dies.
By understanding these key points, it becomes clear that Physical Vapor Deposition is a critical technology across multiple industries, providing essential enhancements to materials and products through the application of specialized thin films.
Summary Table:
Industry | Applications | Examples |
---|---|---|
Aerospace | Temperature-resistant coatings for components | E-beam evaporation for aerospace parts |
Semiconductors & Optics | Optical films for solar panels and devices | E-beam evaporation for semiconductor films |
Tooling & Industrial | Hard, corrosive-resistant coatings for cutting tools | Titanium nitride coatings for metalworking tools |
Decorative & Reflective | Reflective films for mirrors, glass, and electronics | Aluminized PET film for food packaging and balloons |
Biomedical | Biocompatible coatings for medical devices and implants | PVD coatings for surgical instruments and orthopedic implants |
Food Packaging | Barrier films to preserve freshness and extend shelf life | Aluminized PET film for food packaging |
General Industrial | Coatings for hardness, wear resistance, and corrosion resistance | PVD coatings for cutting tools, molds, and dies |
Learn how PVD can transform your materials—contact us today for expert guidance!