Planar magnetron sputtering is a highly efficient vacuum coating technique used to deposit thin films of metals, alloys, and compounds onto various substrates. It operates by creating a plasma of inert gas (typically argon) in a vacuum chamber, where a magnetic field confines electrons near the target surface. This confinement increases the ionization of gas atoms, leading to a higher sputtering rate. Positively charged ions are accelerated toward the negatively charged target, ejecting target atoms that then deposit onto the substrate to form a thin film. The process offers advantages such as high deposition rates, excellent film adhesion, and the ability to coat heat-sensitive materials uniformly.
Key Points Explained:
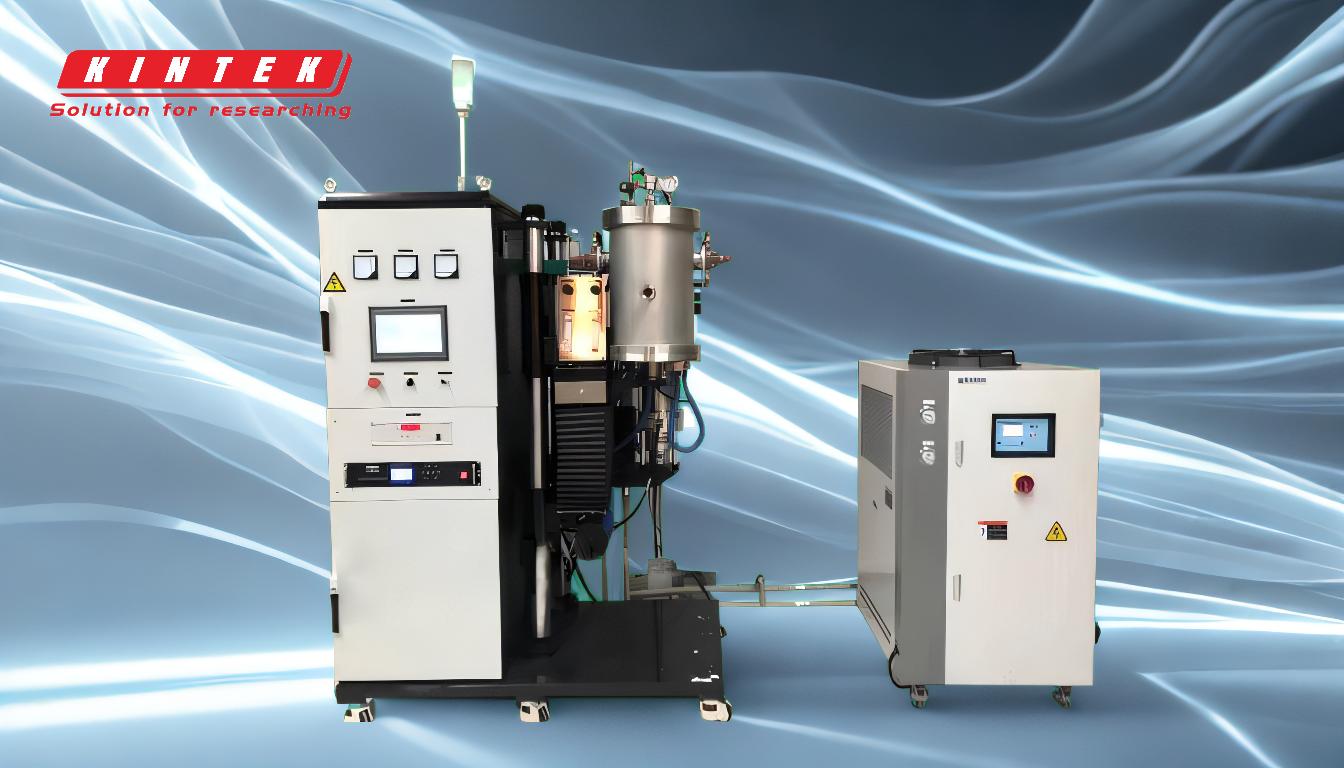
-
Basic Principle of Planar Magnetron Sputtering:
- Planar magnetron sputtering involves the use of a magnetic field to trap electrons near the target surface, enhancing the ionization of inert gas atoms (usually argon).
- A high voltage is applied to the target, creating a plasma. Positively charged argon ions are attracted to the negatively charged target, bombarding it and ejecting target atoms.
- These ejected atoms travel through the vacuum and deposit onto the substrate, forming a thin film.
-
Role of Magnetic Fields:
- The magnetic field generated by magnetrons confines electrons near the target surface, increasing the likelihood of collisions between electrons and gas atoms.
- This confinement leads to a higher plasma density, which enhances the sputtering rate and improves the efficiency of the deposition process.
-
High Deposition Rates:
- Planar magnetron sputtering achieves significantly higher deposition rates compared to other sputtering techniques, such as three-pole sputtering or RF sputtering.
- Deposition rates can range from 200 to 2000 nm/min, making it ideal for applications requiring thick coatings or high throughput.
-
Versatility in Materials:
- This technique can deposit a wide range of materials, including metals, alloys, and compounds, onto various substrates.
- It is suitable for creating high-purity films with excellent adhesion and uniformity, even on complex geometries or heat-sensitive substrates.
-
Advantages of Planar Magnetron Sputtering:
- High Adhesion: The energetic deposition process ensures strong bonding between the film and the substrate.
- Uniformity: The technique provides excellent coverage of steps and small features, making it suitable for complex geometries.
- Automation: The process is easily automated, enabling consistent and repeatable results in industrial applications.
- Heat Sensitivity: It can coat heat-sensitive substrates without causing thermal damage.
-
Process Steps:
- The substrate is placed in a vacuum chamber, and the air is evacuated.
- The target material is introduced into the chamber, and an inert gas (argon) is flowed in.
- A high voltage is applied to the target, generating a plasma and initiating the sputtering process.
- Ejected target atoms deposit onto the substrate, forming a thin film.
-
Applications:
- Planar magnetron sputtering is widely used in industries such as electronics, optics, and automotive for depositing functional and decorative coatings.
- It is particularly valuable for applications requiring high-quality, durable films, such as semiconductor devices, solar panels, and anti-reflective coatings.
By leveraging the principles of plasma physics and magnetic confinement, planar magnetron sputtering offers a robust and versatile solution for thin-film deposition, meeting the demands of modern manufacturing and advanced material science.
Summary Table:
Aspect | Details |
---|---|
Basic Principle | Uses magnetic fields to trap electrons, enhancing ionization and sputtering of target atoms. |
Deposition Rate | 200–2000 nm/min, ideal for high-throughput applications. |
Materials | Metals, alloys, and compounds on various substrates. |
Advantages | High adhesion, uniformity, automation, and heat-sensitive coating capabilities. |
Applications | Electronics, optics, automotive, semiconductors, solar panels, and anti-reflective coatings. |
Discover how planar magnetron sputtering can enhance your manufacturing process—contact our experts today!