A plasma deposition reactor is a specialized device used in materials science and engineering to deposit thin films or coatings onto substrates using plasma, which is a state of matter where a significant portion of the gas is ionized. This process is crucial in industries such as semiconductor manufacturing, optics, and surface engineering, where precise and high-quality coatings are required. The reactor generates plasma by ionizing a gas, which then interacts with the substrate to deposit the desired material. The degree of ionization in the plasma can vary significantly, influencing the properties of the deposited material.
Key Points Explained:
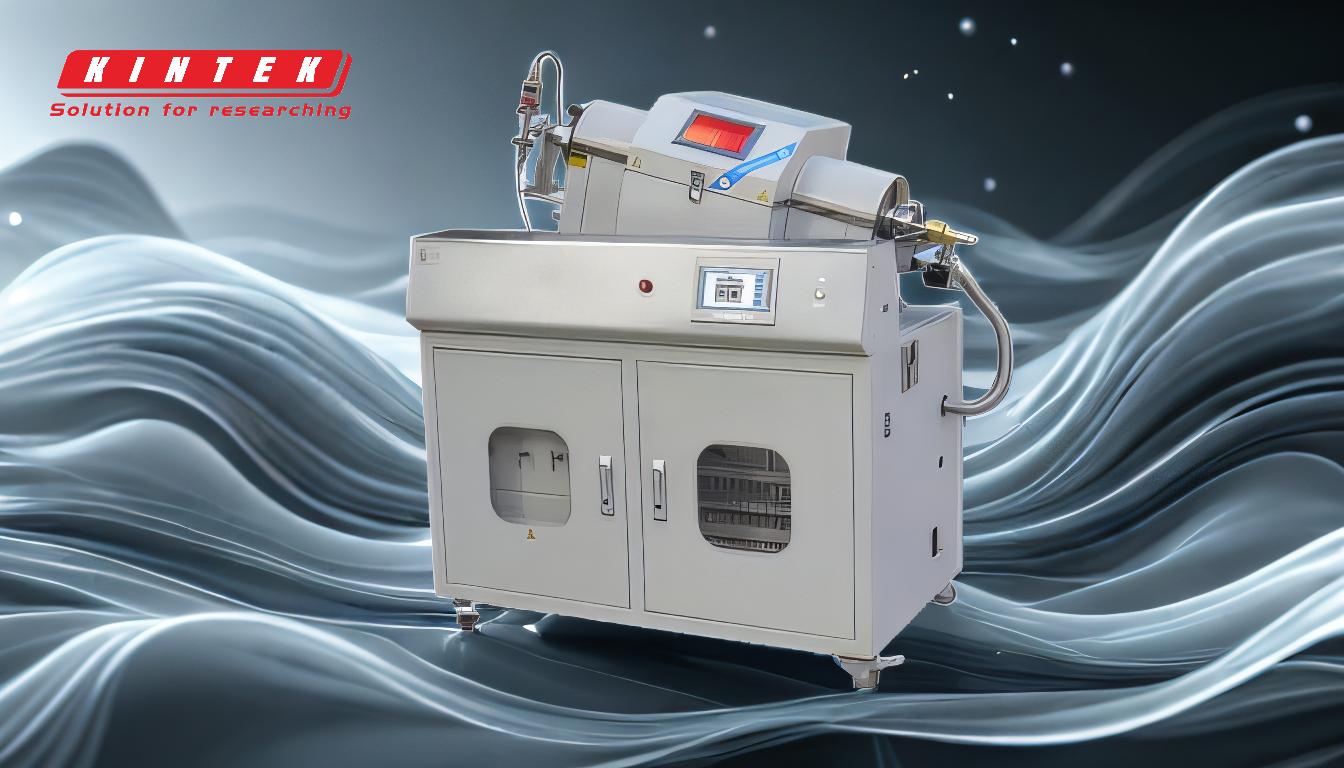
-
Definition of Plasma in Material Processing:
- Plasma is a state of matter where a significant percentage of gas atoms or molecules are ionized. This ionization can range from very low levels (around 10^-4) in capacitive discharges to much higher levels (5–10%) in high-density inductive plasmas. The level of ionization affects the energy and reactivity of the plasma, which in turn influences the deposition process.
-
Function of a Plasma Deposition Reactor:
- The primary function of a plasma deposition reactor is to create a controlled environment where plasma can be generated and used to deposit thin films or coatings onto a substrate. This is achieved by introducing a gas into the reactor, ionizing it to create plasma, and then using this plasma to deposit material onto the substrate.
-
Types of Plasmas Used:
- Capacitive Discharge Plasmas: These plasmas have a relatively low degree of ionization (around 10^-4). They are typically used in processes where a lower energy plasma is sufficient, such as in the deposition of certain types of thin films.
- High-Density Inductive Plasmas: These plasmas have a much higher degree of ionization (5–10%). They are used in applications requiring more energetic and reactive plasmas, such as in the deposition of high-quality, dense films.
-
Applications of Plasma Deposition Reactors:
- Semiconductor Manufacturing: Plasma deposition reactors are used to deposit thin films of materials like silicon dioxide, silicon nitride, and various metals onto semiconductor wafers. These films are crucial for the fabrication of integrated circuits and other semiconductor devices.
- Optics: In the optics industry, plasma deposition reactors are used to deposit anti-reflective coatings, protective layers, and other functional coatings on lenses and other optical components.
- Surface Engineering: Plasma deposition is used to modify the surface properties of materials, such as improving wear resistance, corrosion resistance, or adhesion properties.
-
Advantages of Plasma Deposition:
- Precision and Control: Plasma deposition allows for precise control over the thickness, composition, and properties of the deposited films. This is essential for applications requiring high-quality coatings.
- Versatility: Plasma deposition can be used with a wide range of materials, including metals, ceramics, and polymers, making it a versatile technique for various industries.
- Enhanced Material Properties: The use of plasma can enhance the properties of the deposited materials, such as increasing their density, hardness, or chemical resistance.
-
Challenges and Considerations:
- Complexity of Process Control: Achieving the desired film properties requires careful control of various parameters, including gas composition, pressure, power, and substrate temperature.
- Equipment Cost and Maintenance: Plasma deposition reactors can be expensive to purchase and maintain, particularly those used for high-density plasmas.
- Safety Concerns: The use of high-energy plasmas and potentially hazardous gases requires strict safety protocols to protect operators and the environment.
In summary, a plasma deposition reactor is a critical tool in modern materials processing, enabling the precise deposition of thin films and coatings with enhanced properties. Its applications span across various industries, from semiconductors to optics, and it offers significant advantages in terms of precision, versatility, and material enhancement. However, the complexity of process control and the associated costs and safety considerations are important factors to keep in mind when utilizing this technology.
Summary Table:
Aspect | Details |
---|---|
Definition | Device using ionized gas (plasma) to deposit thin films on substrates. |
Plasma Types | Capacitive discharge (low ionization) & high-density inductive (high ionization). |
Applications | Semiconductor manufacturing, optics, surface engineering. |
Advantages | Precision, versatility, enhanced material properties. |
Challenges | Process control complexity, high equipment costs, safety concerns. |
Ready to enhance your material processing with plasma deposition? Contact our experts today to learn more!