Plasma-enhanced chemical vapor deposition (PECVD) is a specialized technique used to deposit thin films of various materials, particularly in industries like semiconductors, solar cells, and optoelectronics. Unlike conventional chemical vapor deposition (CVD), PECVD employs plasma to activate precursor gases, enabling lower deposition temperatures and higher deposition rates. This makes it ideal for substrates that cannot withstand high temperatures. PECVD is widely used to produce materials such as silicon nitride (SiNx), silicon dioxide (SiO2), and amorphous silicon (a-Si:H), which are critical in applications like thin-film transistors (TFTs), solar cells, and protective coatings. Its ability to form uniform, high-quality films at lower temperatures has made it indispensable in modern electronics and materials science.
Key Points Explained:
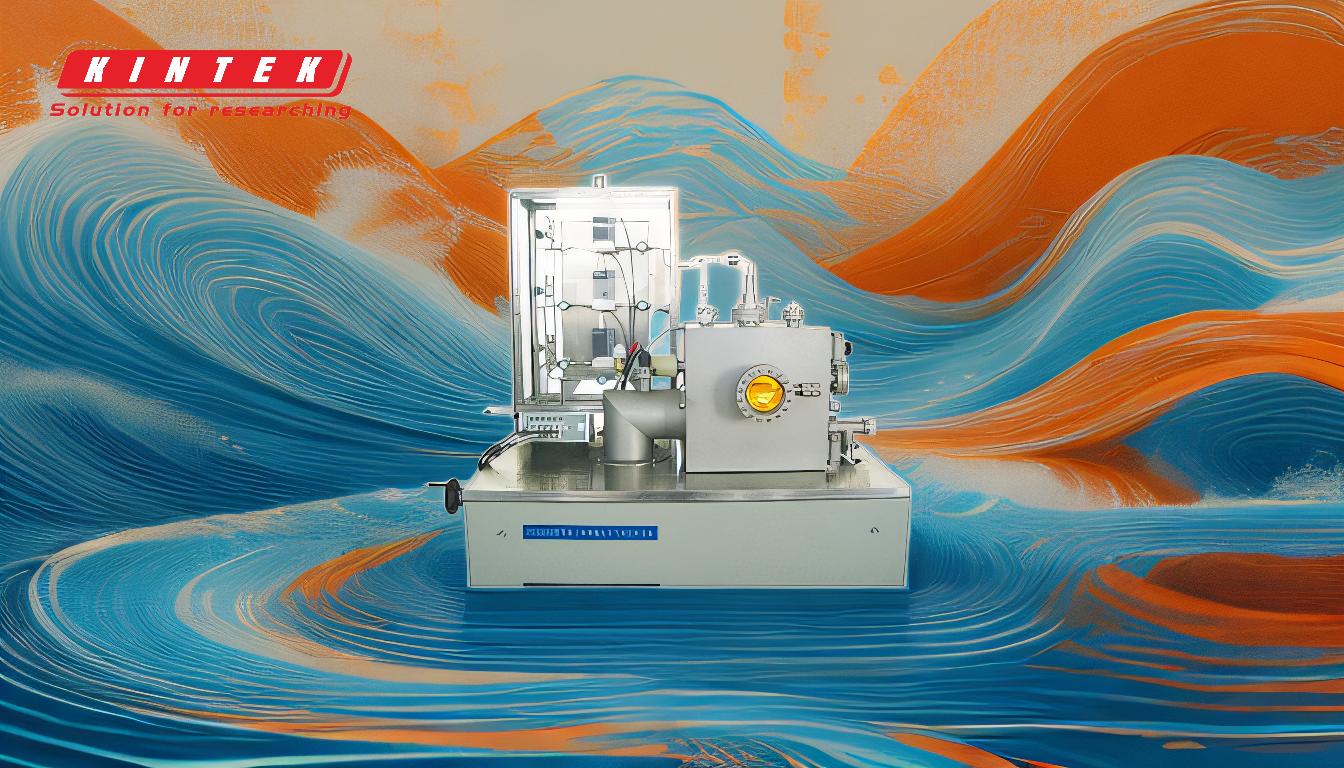
-
Definition and Mechanism of PECVD
- PECVD is a thin-film deposition technique that uses plasma to activate chemical reactions in precursor gases.
- The plasma lowers the energy required for chemical reactions, allowing deposition to occur at lower temperatures compared to traditional CVD.
- This process enables the formation of high-quality, uniform films on temperature-sensitive substrates.
-
Applications of PECVD
- Semiconductors: Used to deposit silicon nitride (SiNx) and silicon dioxide (SiO2) films for insulation and passivation in very large-scale integrated circuits (VLSI, ULSI).
- Thin-Film Transistors (TFTs): Essential in the production of active matrix LCD displays, where glass substrates require low-temperature processing.
- Solar Cells: PECVD is used to produce amorphous silicon (a-Si:H) layers, which are critical for thin-film solar cells.
- Protective and Decorative Coatings: Used to create diamond-like carbon (DLC) coatings for wear resistance and decorative purposes.
- MEMS and Optoelectronics: PECVD is employed in microelectromechanical systems (MEMS) and optoelectronic devices due to its precision and versatility.
-
Advantages of PECVD Over Conventional CVD
- Lower Deposition Temperatures: PECVD can deposit films at temperatures as low as 200-400°C, making it suitable for temperature-sensitive materials like glass and polymers.
- Higher Deposition Rates: The use of plasma enhances reaction kinetics, leading to faster film growth.
- Improved Film Quality: PECVD produces films with better uniformity, surface quality, and step coverage compared to other CVD methods.
- Versatility: Can deposit a wide range of materials, including silicon-based films, metal oxides, and carbon-based coatings.
-
Key Materials Produced by PECVD
- Silicon Nitride (SiNx): Used as a protective and insulating layer in semiconductors.
- Silicon Dioxide (SiO2): Employed as an interlayer dielectric in integrated circuits.
- Amorphous Silicon (a-Si:H): Critical for thin-film solar cells and TFTs.
- Diamond-Like Carbon (DLC): Provides wear resistance and decorative properties.
- Titanium Carbide (TiC): Used for wear-resistant and corrosion-resistant coatings.
- Aluminum Oxide (Al2O3): Acts as a barrier film in various applications.
-
Technological Advancements in PECVD
- Lower Temperature Processes: With the trend toward larger-scale integrated circuits, PECVD is being optimized for even lower temperatures to prevent damage to delicate substrates.
- High Electron Energy Processes: Innovations like ECR plasma and spiral plasma technologies are improving film quality and deposition efficiency.
- Integration with Emerging Technologies: PECVD is being adapted for use in advanced fields like flexible electronics and 3D integrated circuits.
-
PECVD Equipment Components
- Plasma Generation System: Includes RF or microwave power sources to create and sustain the plasma.
- Gas Delivery System: Precise control of precursor gases and carrier gases.
- Vacuum Chamber: Maintains the low-pressure environment required for deposition.
- Substrate Holder: Ensures uniform heating and positioning of the substrate.
- Exhaust System: Removes reaction byproducts and maintains chamber cleanliness.
-
Future Trends in PECVD Technology
- Enhanced Precision: Development of more controlled plasma sources for finer film deposition.
- Eco-Friendly Processes: Reducing the use of hazardous gases and improving energy efficiency.
- Integration with AI: Using machine learning to optimize deposition parameters and improve process control.
- Expansion into New Markets: Growing applications in flexible electronics, biomedical devices, and renewable energy technologies.
In summary, PECVD is a versatile and essential technology in modern manufacturing, offering significant advantages in terms of temperature sensitivity, film quality, and deposition efficiency. Its applications span across semiconductors, solar cells, displays, and protective coatings, making it a cornerstone of advanced materials science and electronics.
Summary Table:
Key Aspect | Details |
---|---|
Definition | PECVD uses plasma to activate precursor gases for thin-film deposition. |
Applications | Semiconductors, TFTs, solar cells, protective coatings, MEMS, optoelectronics. |
Advantages | Lower deposition temps, higher rates, improved film quality, versatility. |
Key Materials | SiNx, SiO2, a-Si:H, DLC, TiC, Al2O3. |
Future Trends | Lower temps, eco-friendly processes, AI integration, new market expansion. |
Learn how PECVD can transform your manufacturing process—contact our experts today!