PVD diamond refers to a type of diamond coating created using Physical Vapor Deposition (PVD) technology. Unlike CVD (Chemical Vapor Deposition) diamonds, which are grown layer by layer from carbon-rich gases, PVD diamond coatings are applied as a thin film on a substrate. This process involves vaporizing solid carbon or diamond-like carbon (DLC) material in a vacuum chamber and depositing it onto a surface. PVD diamond coatings are known for their hardness, wear resistance, and ability to enhance the durability of tools, machinery, and decorative items. While PVD diamond coatings are not bulk diamonds like CVD diamonds, they are widely used in industries requiring enhanced surface properties, such as cutting tools, medical devices, and consumer electronics.
Key Points Explained:
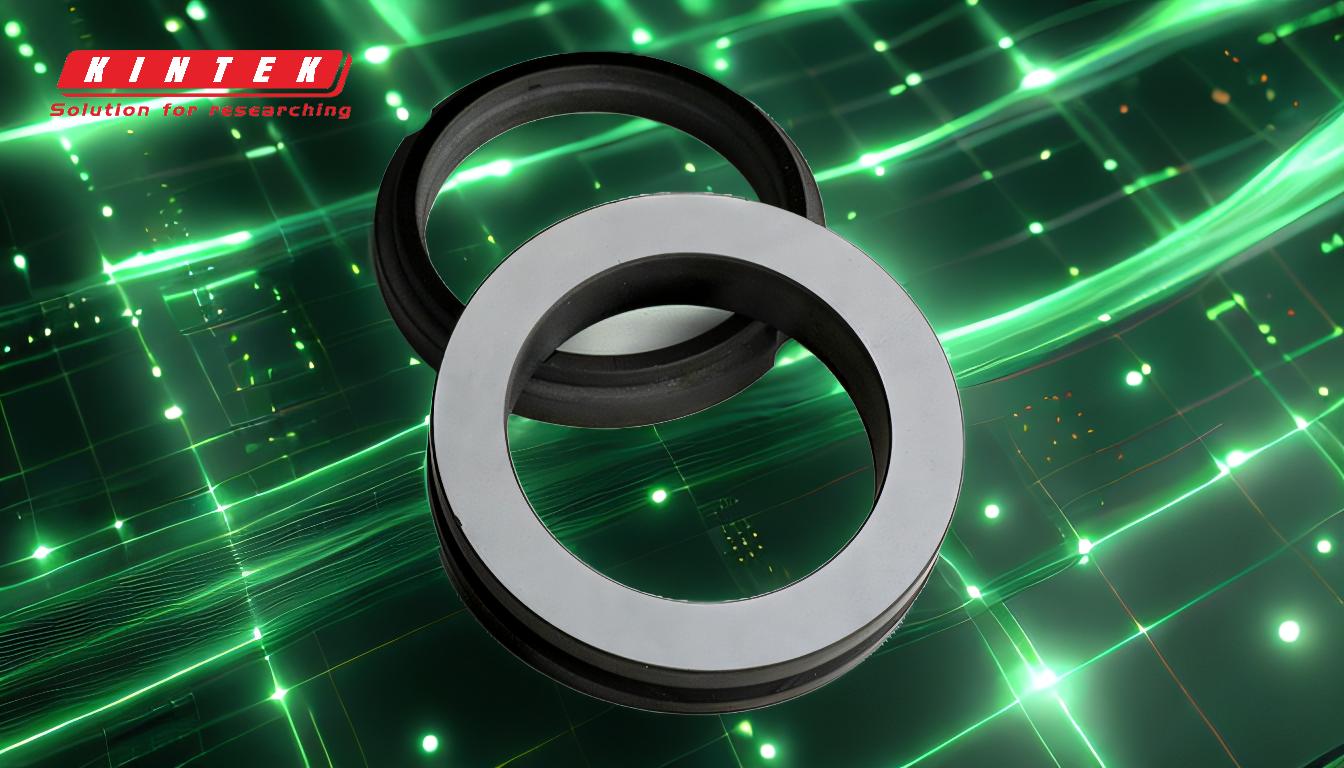
-
What is PVD Diamond?
- PVD diamond refers to a diamond-like coating created using Physical Vapor Deposition (PVD) technology. It involves vaporizing a solid carbon source and depositing it as a thin film on a substrate. This process is distinct from CVD diamond growth, which builds diamond layers from gas-phase carbon atoms.
-
How PVD Diamond is Produced
- PVD diamond coatings are created in a vacuum chamber where a solid carbon or diamond-like carbon (DLC) material is vaporized using techniques like sputtering or arc evaporation. The vaporized material then condenses onto a substrate, forming a thin, durable diamond-like coating.
-
Applications of PVD Diamond
- PVD diamond coatings are used in industries requiring enhanced surface properties, such as:
- Cutting tools: Improves wear resistance and extends tool life.
- Medical devices: Provides biocompatibility and durability.
- Consumer electronics: Enhances scratch resistance and durability.
- Decorative items: Adds a durable, aesthetically pleasing finish to jewelry, hardware, and other products.
- PVD diamond coatings are used in industries requiring enhanced surface properties, such as:
-
Comparison with CVD Diamond
- CVD Diamond: Grown layer by layer from carbon-rich gases, resulting in bulk diamond material. Used for applications like heat sinks, cutting tools, and optical components.
- PVD Diamond: Applied as a thin film coating, enhancing surface properties without creating bulk diamond. Suitable for tools, machinery, and decorative items.
-
Advantages of PVD Diamond
- High hardness and wear resistance.
- Excellent adhesion to substrates.
- Ability to coat complex geometries.
- Suitable for low-temperature processes, making it ideal for heat-sensitive materials.
-
Limitations of PVD Diamond
- PVD diamond coatings are thin and not suitable for applications requiring bulk diamond properties.
- The process is line-of-sight, meaning only surfaces directly exposed to the vapor source are coated.
-
Future Trends
- Advances in PVD technology are expected to improve coating uniformity and reduce costs, making PVD diamond coatings more accessible for a wider range of applications. Research is also exploring hybrid techniques combining PVD and CVD to leverage the benefits of both methods.
By understanding the distinct characteristics and applications of PVD diamond coatings, purchasers and engineers can make informed decisions about their use in various industries.
Summary Table:
Aspect | Details |
---|---|
Definition | Thin diamond-like coating created using Physical Vapor Deposition (PVD). |
Production Process | Vaporizes solid carbon/DLC in a vacuum chamber, depositing it as a thin film. |
Applications | Cutting tools, medical devices, consumer electronics, decorative items. |
Advantages | High hardness, wear resistance, excellent adhesion, low-temperature process. |
Limitations | Thin coatings, line-of-sight process. |
Future Trends | Improved uniformity, cost reduction, hybrid PVD-CVD techniques. |
Ready to enhance your products with PVD diamond coatings? Contact us today for expert guidance!