Physical Vapor Deposition (PVD) is a critical process in electronics, particularly in semiconductor manufacturing and the production of thin-film photovoltaic cells. It involves the deposition of thin films of materials onto substrates through physical means, such as sputtering or ion plating. In semiconductor manufacturing, PVD is used to deposit metals like platinum, tungsten, or copper onto microchips, often in multilayered structures. For thin-film photovoltaic cells, materials such as copper, indium, gallium, or tellurium are deposited onto glass or plastic substrates. These processes are essential for creating high-performance electronic devices and renewable energy technologies.
Key Points Explained:
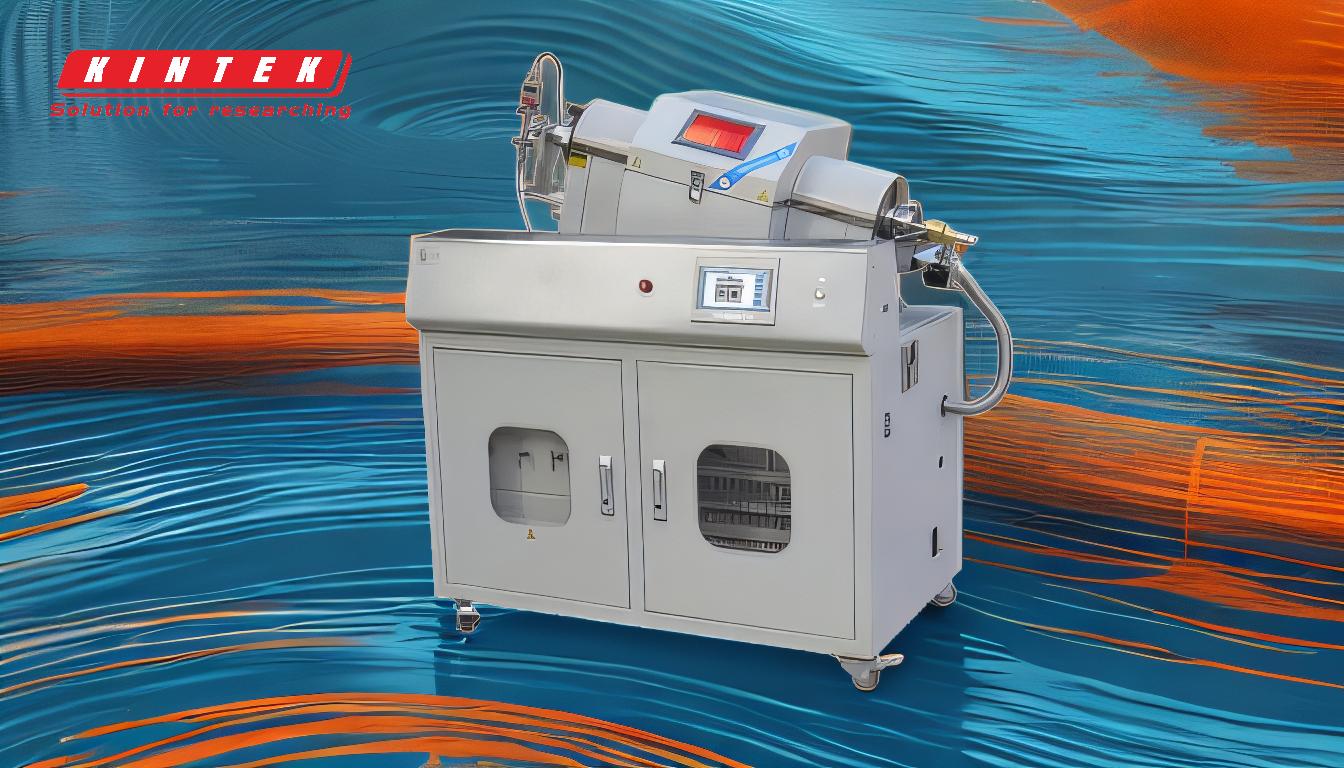
-
Definition and Purpose of PVD:
- PVD (Physical Vapor Deposition) is a process used to deposit thin films of materials onto substrates. It is widely used in electronics, particularly in semiconductor manufacturing and the production of thin-film photovoltaic cells.
- The primary purpose of PVD is to create high-quality, durable, and precise thin films that are essential for the functionality of electronic devices and renewable energy technologies.
-
Applications in Semiconductor Manufacturing:
- In semiconductor manufacturing, PVD is used to deposit metals such as platinum, tungsten, or copper onto microchips. These metals are often deposited in multilayered structures to create the complex circuitry required for modern microchips.
- The precision and control offered by PVD techniques are crucial for the miniaturization and performance enhancement of semiconductor devices.
-
Applications in Thin-Film Photovoltaic Cells:
- PVD is also used in the production of thin-film photovoltaic cells, which are a type of solar cell. Materials like copper, indium, gallium, or tellurium are deposited onto glass or plastic substrates to create the active layers of the solar cells.
- These materials are chosen for their ability to efficiently convert sunlight into electricity, making PVD a key process in the development of renewable energy technologies.
-
Techniques Used in PVD:
- Sputter Deposition: This is one of the most common PVD techniques, where high-energy particles are used to knock atoms off a target material, which then deposit onto a substrate. This technique is widely used in both semiconductor manufacturing and photovoltaic cell production.
- Ion Plating: Another PVD technique, ion plating involves the use of ionized gas to enhance the adhesion and density of the deposited film. This technique is particularly useful for creating highly durable and uniform coatings.
-
Materials Used in PVD:
- The choice of materials in PVD depends on the specific application. For microchips, metals like platinum, tungsten, or copper are commonly used due to their excellent electrical conductivity and durability.
- For thin-film photovoltaic cells, materials such as copper, indium, gallium, or tellurium are used because of their ability to efficiently convert sunlight into electricity.
-
Advantages of PVD:
- Precision: PVD allows for the deposition of very thin and precise layers of material, which is essential for the miniaturization of electronic components.
- Durability: The films created through PVD are highly durable and resistant to wear and corrosion, making them ideal for use in harsh environments.
- Versatility: PVD can be used with a wide range of materials and substrates, making it a versatile process for various applications in electronics and renewable energy.
-
Challenges and Considerations:
- Cost: PVD equipment and processes can be expensive, particularly for high-precision applications in semiconductor manufacturing.
- Complexity: The process requires careful control of parameters such as temperature, pressure, and deposition rate to achieve the desired film properties.
- Material Limitations: While PVD is versatile, not all materials are suitable for deposition using this method, and some may require alternative techniques.
In summary, PVD is a vital process in the electronics industry, enabling the production of high-performance semiconductor devices and thin-film photovoltaic cells. Its precision, durability, and versatility make it an indispensable technology in the advancement of modern electronics and renewable energy solutions.
Summary Table:
Aspect | Details |
---|---|
Definition | PVD deposits thin films onto substrates using physical methods like sputtering. |
Applications | - Semiconductor manufacturing (e.g., platinum, tungsten, copper). |
- Thin-film photovoltaic cells (e.g., copper, indium, gallium). | |
Techniques | - Sputter deposition. |
- Ion plating. | |
Materials | - Metals like platinum, tungsten, copper. |
- Solar cell materials like copper, indium, gallium, tellurium. | |
Advantages | - Precision for miniaturization. |
- Durable and corrosion-resistant films.
- Versatile for various materials and substrates. | | Challenges | - High cost and complexity.
- Material limitations for certain applications. |
Discover how PVD can revolutionize your electronics production—contact our experts today!