Pyrolysis of biomass to biofuel is a thermochemical process that converts organic biomass materials into liquid biofuel, gases, and solid char by heating the biomass in the absence of oxygen. This process typically occurs at high temperatures (500°C–700°C), where the biomass is thermally decomposed into pyrolysis vapor, gas, and char. The vapors are then cooled and condensed into a liquid known as bio-crude oil or bio-oil, which can be further refined for use as a renewable fuel. Pyrolysis is a promising technology for producing sustainable biofuels, offering a greener alternative to fossil fuels while utilizing organic waste materials.
Key Points Explained:
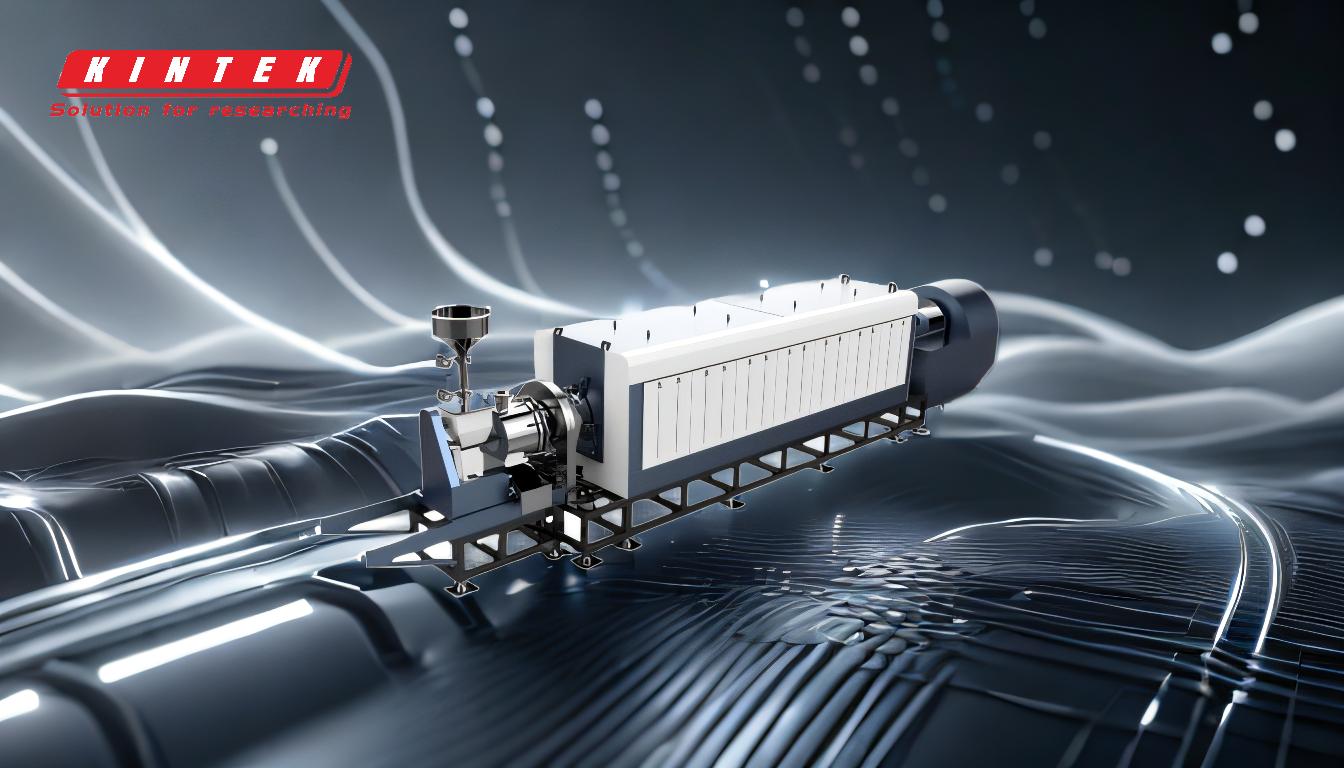
-
Definition and Process of Pyrolysis:
- Pyrolysis is a thermochemical process that decomposes biomass in the absence of oxygen at high temperatures (500°C–700°C).
- The process breaks down biomass into three main products: pyrolysis vapor (which condenses into bio-oil), combustible gases, and solid char (bio-char).
- The absence of oxygen prevents combustion, ensuring the biomass is thermally decomposed rather than burned.
-
Steps Involved in Biomass Pyrolysis:
- Pre-treatment: Biomass is dried and crushed to remove moisture and reduce particle size, ensuring efficient heating.
- Pyrolysis: The pre-treated biomass is heated in a pyrolysis chamber at high temperatures, producing biochar, gases, and vapors.
- Condensation: The pyrolysis vapors are cooled and condensed into liquid bio-crude oil.
- Post-treatment: The biochar is discharged and cooled, while exhaust gases are cleaned to reduce harmful emissions.
-
Products of Pyrolysis:
- Bio-oil (Bio-crude oil): A liquid fuel that can be refined and used as a renewable alternative to fossil fuels.
- Bio-char: A solid carbon-rich material that can be used as a soil amendment or for carbon sequestration.
- Combustible gases: These can be used to generate heat or electricity, making the process energy-efficient.
-
Applications of Bio-oil:
- Bio-oil can be used as a direct fuel in boilers or turbines for heat and power generation.
- It can be further refined into transportation fuels, such as biodiesel or renewable diesel, reducing reliance on fossil fuels.
- Bio-oil is also a feedstock for producing chemicals and other bio-based products.
-
Advantages of Biomass Pyrolysis:
- Sustainability: Utilizes renewable biomass resources, reducing dependence on fossil fuels.
- Waste Utilization: Converts agricultural residues, forestry waste, and other organic materials into valuable products.
- Carbon Neutrality: The carbon released during biofuel combustion is offset by the carbon absorbed during biomass growth, making it a carbon-neutral process.
- Versatility: Produces multiple valuable products (bio-oil, bio-char, and gases) from a single process.
-
Challenges and Considerations:
- High Energy Input: Pyrolysis requires significant energy to achieve high temperatures, which can impact overall efficiency.
- Bio-oil Quality: Raw bio-oil often contains impurities and has a high oxygen content, requiring further refining for commercial use.
- Feedstock Variability: The composition of biomass can vary, affecting the consistency and quality of pyrolysis products.
- Economic Viability: Scaling up pyrolysis technology and ensuring cost competitiveness with fossil fuels remain challenges.
-
Comparison with Other Biofuel Production Methods:
- Unlike biochemical processes (e.g., fermentation and transesterification), which produce ethanol and biodiesel, pyrolysis produces a liquid bio-oil that can be refined into various fuels.
- Pyrolysis is faster and can handle a wider range of feedstocks compared to biochemical methods, which often require specific biomass types.
-
Future Prospects:
- Advances in pyrolysis technology, such as catalytic pyrolysis and fast pyrolysis, aim to improve bio-oil yield and quality.
- Integration with other renewable energy systems, such as solar or wind, could reduce the energy input required for pyrolysis.
- Policy support and incentives for biofuel production could drive the adoption of pyrolysis as a sustainable energy solution.
In summary, pyrolysis of biomass to biofuel is a versatile and sustainable process that converts organic materials into renewable fuels and valuable byproducts. While challenges remain, ongoing advancements in technology and growing interest in renewable energy make pyrolysis a promising pathway for reducing reliance on fossil fuels and mitigating climate change.
Summary Table:
Aspect | Details |
---|---|
Process | Thermochemical decomposition of biomass at 500°C–700°C in the absence of oxygen. |
Products | Bio-oil (renewable fuel), bio-char (soil amendment), and combustible gases. |
Applications | Heat/power generation, transportation fuels, and chemical feedstocks. |
Advantages | Sustainability, waste utilization, carbon neutrality, and versatility. |
Challenges | High energy input, bio-oil quality, feedstock variability, and cost. |
Future Prospects | Catalytic pyrolysis, integration with renewables, and policy support. |
Discover how biomass pyrolysis can revolutionize renewable energy—contact us today to learn more!