Pyrolysis of rubber, particularly in the context of waste tires, is a thermochemical decomposition process that breaks down rubber into smaller molecules and chemical compounds in the absence of oxygen. This process generates valuable products such as liquid oil, gas, and solid residues like carbon black and steel. The process involves heating rubber waste to high temperatures (typically between 200°C and 900°C), causing it to melt, vaporize, and decompose. The resulting vapors are condensed into liquid oil, while non-condensable gases are cleaned and stored for further use. Pyrolysis is an effective method for recycling rubber waste, reducing environmental pollution, and producing useful outputs for energy and industrial applications.
Key Points Explained:
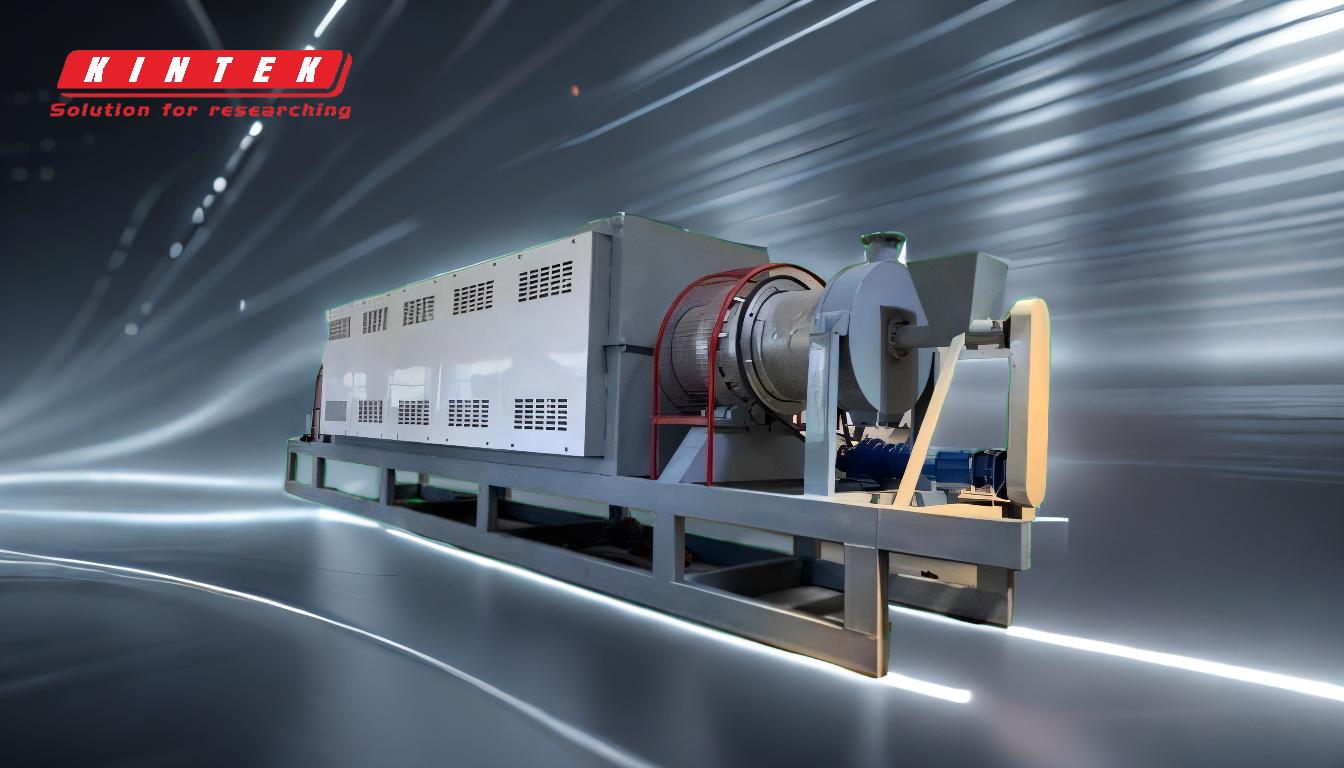
-
Definition of Pyrolysis:
- Pyrolysis is a thermochemical decomposition process that occurs in the absence of oxygen.
- It involves heating materials, such as rubber, to high temperatures, causing them to break down into smaller molecules and chemical compounds.
- This process generates three main types of products: gases (syngas), liquids (bio-oil), and solids (bio-char or carbon black).
-
Pyrolysis of Rubber (Tires):
- Rubber pyrolysis specifically refers to the thermal decomposition of waste tires.
- The process begins by feeding whole or shredded tires into a pyrolysis reactor.
- The reactor is heated to temperatures ranging from 200°C to 900°C, depending on the desired end products.
- During heating, the rubber undergoes depolymerization, breaking down into liquid oil, gas, and solid residues.
-
Steps in the Rubber Pyrolysis Process:
- Feeding: Waste tires are loaded into the pyrolysis reactor.
-
Heating: The reactor is heated to melt and vaporize the rubber.
- At around 100°C, small molecules in the tires volatilize.
- At 140°C, the rubber melts into a liquid state.
- Between 260°C and 280°C, the process is maintained for 6-12 hours to ensure complete decomposition.
- Condensation: The vaporized gases are condensed into liquid oil.
- Separation: Non-condensable gases are desulfurized and cleaned before storage.
- Collection: Final products, including liquid oil, carbon black, and steel wire, are collected for further use.
-
Products of Rubber Pyrolysis:
- Liquid Oil: The primary product, pyrolysis oil, can be used as fuel for heating, power generation, or further refined into diesel.
- Gas: Non-condensable gases, such as syngas, can be used for energy production or hydrogen extraction.
- Solid Residues: Carbon black and steel wire are recovered and can be reused in industrial applications.
-
Applications of Pyrolysis Products:
- Pyrolysis Oil: Used as a fuel substitute in industrial boilers, furnaces, and power plants.
- Carbon Black: Used as a reinforcing agent in rubber products, pigments, and inks.
- Steel Wire: Recycled for use in construction or manufacturing.
- Syngas: Utilized for energy generation or as a feedstock for chemical production.
-
Advantages of Rubber Pyrolysis:
- Waste Reduction: Converts non-biodegradable rubber waste into useful products, reducing landfill usage.
- Resource Recovery: Recovers valuable materials like oil, carbon black, and steel.
- Energy Generation: Produces fuel and energy from waste, contributing to a circular economy.
- Environmental Benefits: Reduces pollution and greenhouse gas emissions compared to traditional waste disposal methods.
-
Challenges and Considerations:
- Energy Intensity: The process requires significant energy input to achieve high temperatures.
- Process Control: Maintaining optimal conditions (temperature, pressure, and absence of oxygen) is critical for efficiency.
- Product Quality: The quality of pyrolysis oil and other products depends on the feedstock and process conditions.
- Economic Viability: High initial investment and operational costs can be a barrier to widespread adoption.
-
Comparison with Other Pyrolysis Processes:
- Plastic Pyrolysis: Similar to rubber pyrolysis but focuses on converting plastic waste into oil and gas.
- Biomass Pyrolysis: Involves the decomposition of organic materials like wood or agricultural waste to produce biochar, bio-oil, and syngas.
- Tire vs. Plastic Pyrolysis: Tire pyrolysis yields more solid residues (carbon black and steel) compared to plastic pyrolysis, which primarily produces liquid and gas.
-
Future Prospects:
- Technological Advancements: Innovations in reactor design and process optimization can improve efficiency and reduce costs.
- Circular Economy Integration: Pyrolysis aligns with circular economy principles by converting waste into reusable resources.
- Policy Support: Government incentives and regulations promoting waste recycling can drive the adoption of pyrolysis technology.
By understanding the pyrolysis of rubber, stakeholders in waste management, energy production, and industrial manufacturing can make informed decisions to harness its potential for sustainable resource recovery.
Summary Table:
Aspect | Details |
---|---|
Process | Thermochemical decomposition of rubber in the absence of oxygen. |
Temperature Range | 200°C to 900°C, depending on desired products. |
Main Products | Liquid oil, syngas, carbon black, and steel wire. |
Applications | Fuel for energy, reinforcing agents, recycled steel, and chemical feedstock. |
Advantages | Waste reduction, resource recovery, energy generation, and environmental benefits. |
Challenges | High energy input, process control, product quality, and economic viability. |
Future Prospects | Innovations in reactor design, circular economy integration, and policy support. |
Ready to explore how rubber pyrolysis can benefit your operations? Contact us today to learn more!