Sinter mix is a critical material used in the sintering process, primarily in the production of iron and steel. It consists of a blend of powdered iron ore, coke (a carbon-rich fuel derived from coal), and other additives such as limestone or dolomite. This mixture is ignited and subjected to high temperatures, causing the particles to fuse into larger lumps called sinter. The resulting sinter is then used as a feedstock in blast furnaces to produce molten iron, which is further processed into steel. Sintering is also applicable in ceramics and glass manufacturing, where it helps in forming solid structures from powdered materials.
Key Points Explained:
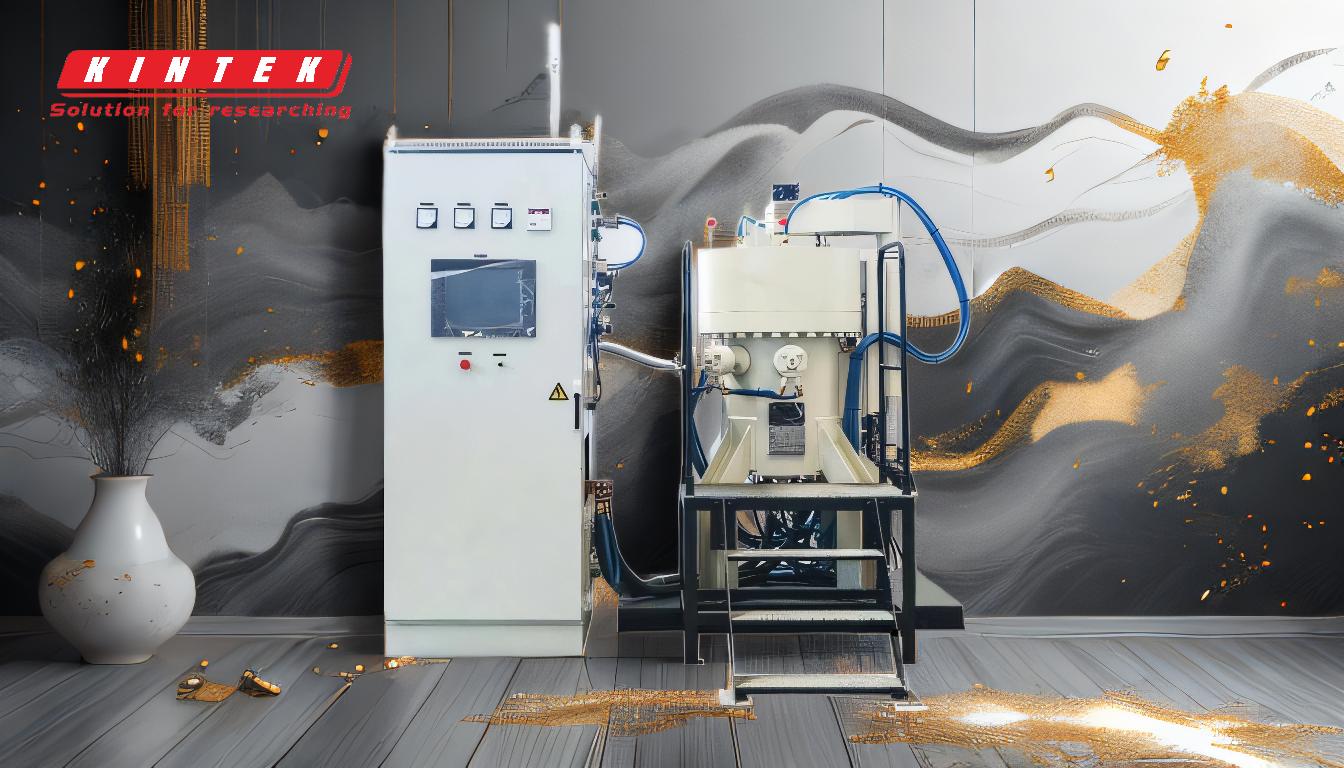
-
Composition of Sinter Mix:
- Powdered Iron Ore: The primary component, sourced from mined iron ore, is finely ground to facilitate the sintering process.
- Coke: Acts as a fuel and reducing agent, providing the necessary heat and carbon for the chemical reactions during sintering.
- Additives: Materials like limestone or dolomite are added to improve the quality of the sinter by controlling impurities and enhancing the chemical properties of the final product.
-
Sintering Process:
- Ignition: The sinter mix is spread on a traveling grate and ignited using a gas burner. Air is drawn through the bed to sustain the combustion reaction.
- Combustion and Fusion: The heat generated causes the iron ore particles to partially melt and fuse together, forming larger, porous lumps known as sinter.
- Cooling: After the sintering process, the sinter is cooled and crushed to the desired size for use in blast furnaces.
-
Role in Steel Production:
- Blast Furnace Feedstock: Sinter is a key raw material in blast furnaces, where it is melted along with coke and limestone to produce molten iron.
- Improved Efficiency: Using sinter in blast furnaces improves the efficiency of iron production by providing a consistent and high-quality feedstock.
-
Applications Beyond Steel:
- Ceramics: Sintering is used to form solid ceramic products from powdered materials, enhancing their strength and durability.
- Glass Manufacturing: Similar to ceramics, sintering helps in forming glass products by fusing powdered glass materials at high temperatures.
-
Benefits of Sintering:
- Resource Utilization: Sintering allows for the efficient use of fine iron ore particles that might otherwise be wasted.
- Environmental Impact: The process can reduce the environmental footprint of steel production by recycling waste materials and reducing emissions.
By understanding the composition, process, and applications of sinter mix, purchasers can make informed decisions about the materials they need for their specific manufacturing requirements. This knowledge is crucial for optimizing production processes and ensuring the quality of the final products.
Summary Table:
Aspect | Details |
---|---|
Composition | Powdered iron ore, coke, and additives like limestone or dolomite. |
Sintering Process | Ignition, combustion, fusion, and cooling to form sinter lumps. |
Role in Steel | Feedstock for blast furnaces, improving iron production efficiency. |
Other Applications | Used in ceramics and glass manufacturing for solid structure formation. |
Benefits | Efficient resource utilization and reduced environmental impact. |
Optimize your production process with high-quality sinter mix—contact us today for expert advice!