Sputtering in Physical Vapor Deposition (PVD) is a process where a target material is bombarded with high-energy ions, typically from a plasma, causing atoms to be ejected from the target. These ejected atoms then travel through a vacuum and deposit onto a substrate, forming a thin film. This method is widely used in industries for creating high-quality, durable coatings on various materials. The process is highly controllable, allowing for precise deposition of materials with specific properties.
Key Points Explained:
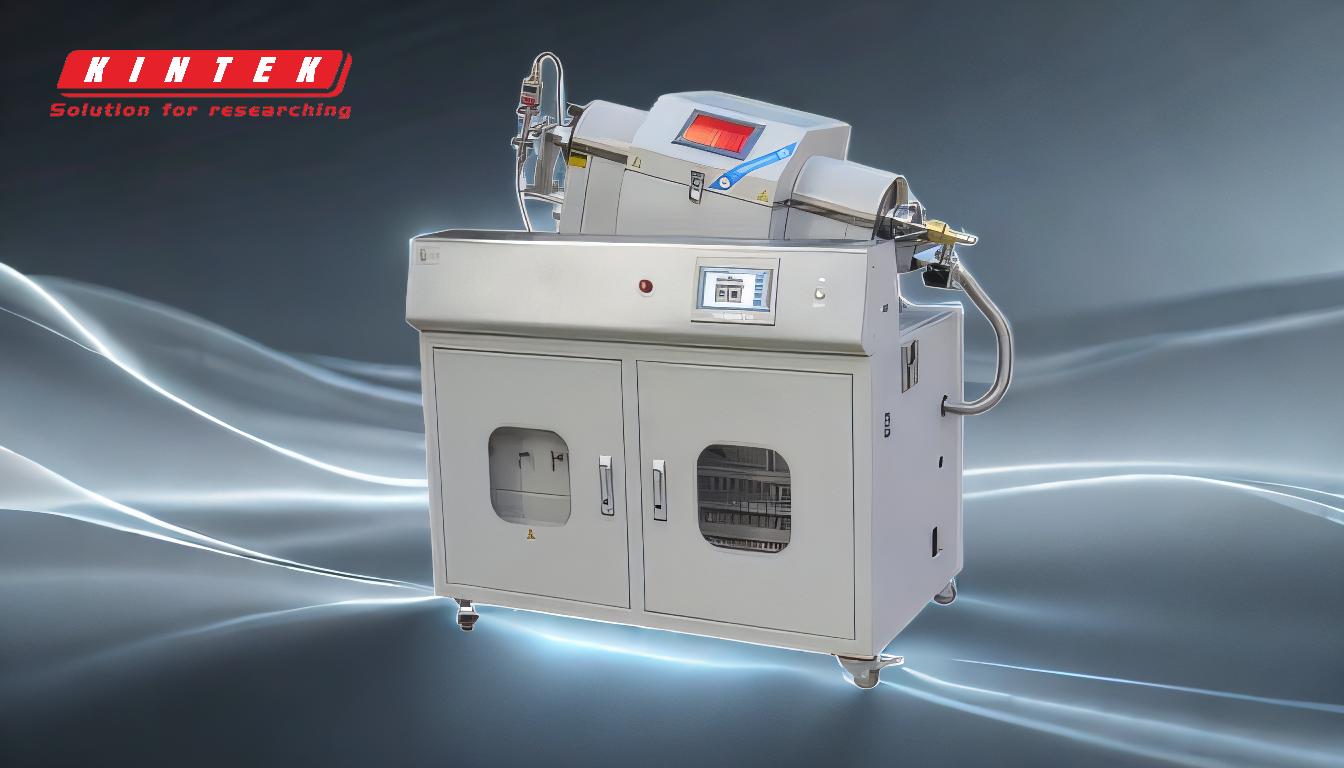
-
Definition of Sputtering in PVD:
- Sputtering is a key technique within the PVD family, which also includes methods like eBeam evaporation and thermal evaporation. It involves the ejection of atoms from a solid target material due to bombardment by high-energy ions, usually from a plasma. These ejected atoms then travel through a vacuum and deposit onto a substrate to form a thin film.
-
Role of Plasma in Sputtering:
- Plasma, typically containing argon ions and electrons, is generated to initiate the sputtering process. The argon ions are accelerated towards the target material, striking it and causing atoms to be ejected. This plasma is crucial as it provides the energy needed to dislodge atoms from the target.
-
Importance of Vacuum Environment:
- The sputtering process occurs in a high-tech vacuum chamber. The vacuum environment is essential to minimize contamination and ensure that the ejected atoms travel unimpeded to the substrate. It also helps in maintaining the purity and quality of the deposited film.
-
Process Parameters:
- Pressure: The chamber pressure is a critical parameter in sputter deposition. It affects the mean free path of the ejected atoms, influencing their energy distribution upon reaching the substrate. Proper control of pressure ensures the desired film properties.
- Temperature: Deposition temperature also plays a significant role. It affects the mobility of atoms on the substrate surface, influencing the film's microstructure and properties.
-
Applications and Advantages:
- Sputtering is used to create thin film coatings on a wide variety of materials, including metals, semiconductors, and insulators. It allows for the deposition of materials with diverse compositions, making it versatile for various industrial applications.
- The process is highly controllable, enabling precise control over film thickness, composition, and properties. This makes it suitable for applications requiring high-quality, durable coatings.
-
Comparison with Other PVD Methods:
- Thermal Evaporation: In thermal evaporation, the target material is heated to its evaporation point, and the vapor condenses on the substrate. This method is simpler but may not be suitable for materials with high melting points.
- eBeam Evaporation: This method uses an electron beam to heat the target material, allowing for higher evaporation rates and the ability to deposit high-melting-point materials. However, it requires more complex equipment compared to sputtering.
By understanding these key points, one can appreciate the complexity and precision involved in the sputtering process within PVD, making it a preferred method for high-quality thin film deposition.
Summary Table:
Aspect | Details |
---|---|
Definition | Ejection of atoms from a target via high-energy ion bombardment. |
Role of Plasma | Argon ions in plasma dislodge target atoms, enabling deposition. |
Vacuum Environment | Ensures minimal contamination and high-quality film deposition. |
Process Parameters | Pressure and temperature control film properties and microstructure. |
Applications | Used for coatings on metals, semiconductors, and insulators. |
Advantages | High precision, versatility, and durability in thin film deposition. |
Comparison | More controllable than thermal evaporation; less complex than eBeam. |
Discover how sputtering in PVD can enhance your material coatings—contact our experts today!