Sputtering is a widely used thin film deposition technique in the Physical Vapor Deposition (PVD) category. It involves bombarding a target material with high-energy ions in a vacuum chamber filled with an inert gas, typically argon. The ions dislodge atoms or molecules from the target, which then travel through the chamber and deposit onto a substrate, forming a thin film. This process is highly controlled, allowing for precise and uniform coatings on substrates like silicon wafers or solar panels. Sputtering is valued for its ability to produce high-quality, durable films with excellent adhesion and uniformity.
Key Points Explained:
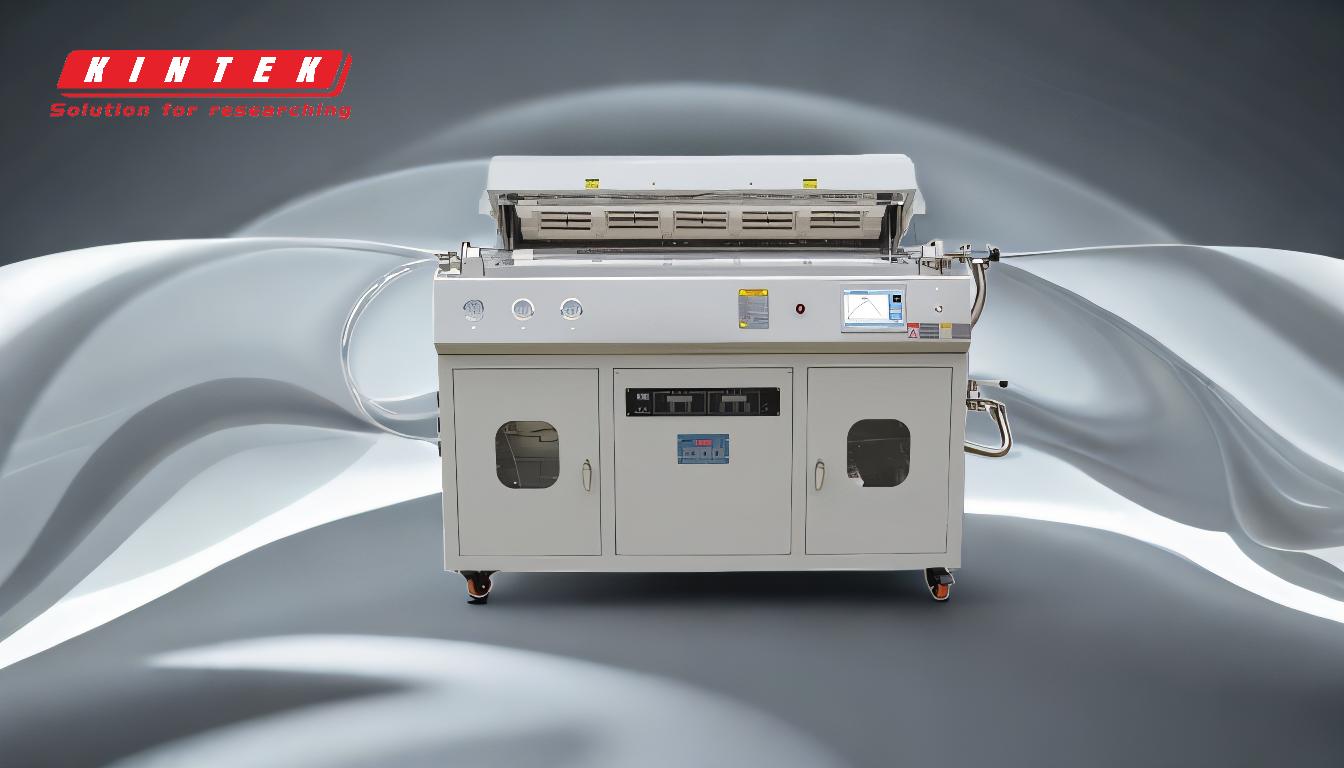
-
Definition and Purpose of Sputtering:
- Sputtering is a physical vapor deposition (PVD) technique used to deposit thin films onto substrates.
- The primary purpose is to create uniform, high-quality coatings for applications in electronics, optics, solar panels, and more.
-
Components of the Sputtering Process:
- Vacuum Chamber: The process occurs in a vacuum to minimize contamination and ensure controlled conditions.
- Inert Gas (Argon): Argon is commonly used because it is chemically inert, reducing unwanted reactions during the process.
- Target Material: The material to be deposited, which is placed on a cathode.
- Substrate: The surface onto which the thin film is deposited, such as a silicon wafer or solar panel.
-
Mechanism of Sputtering:
- Ion Generation: A high voltage is applied to the cathode, generating a plasma of positively charged argon ions.
- Ion Bombardment: These ions are accelerated toward the target material, colliding with its surface.
- Ejection of Atoms: The collisions transfer energy to the target, dislodging atoms or molecules in the form of neutral particles.
- Deposition: The ejected particles travel through the vacuum chamber and deposit onto the substrate, forming a thin film.
-
Advantages of Sputtering:
- Uniformity: Produces highly uniform and consistent coatings.
- Adhesion: Ensures strong adhesion of the film to the substrate.
- Versatility: Can deposit a wide range of materials, including metals, alloys, and ceramics.
- Precision: Allows for precise control over film thickness and composition.
-
Applications of Sputtering:
- Electronics: Used in the fabrication of semiconductors, integrated circuits, and magnetic storage devices.
- Optics: Deposits anti-reflective and reflective coatings on lenses and mirrors.
- Solar Panels: Creates thin-film solar cells with high efficiency.
- Decorative Coatings: Applied in automotive and architectural industries for aesthetic and protective purposes.
-
Types of Sputtering:
- DC Sputtering: Uses direct current to generate the plasma, suitable for conductive materials.
- RF Sputtering: Employs radio frequency for non-conductive materials.
- Magnetron Sputtering: Enhances efficiency by using magnetic fields to confine the plasma near the target.
-
Challenges and Considerations:
- Cost: Requires expensive equipment and high vacuum conditions.
- Complexity: Demands precise control over process parameters like pressure, voltage, and gas flow.
- Material Limitations: Some materials may be difficult to sputter due to low sputtering yields or reactivity.
By understanding these key points, one can appreciate the complexity and versatility of sputtering as a thin film deposition technique. It is a critical process in modern manufacturing, enabling advancements in technology and materials science.
Summary Table:
Aspect | Details |
---|---|
Definition | A PVD technique for depositing thin films onto substrates. |
Key Components | Vacuum chamber, inert gas (argon), target material, substrate. |
Mechanism | Ion bombardment ejects target atoms, which deposit onto the substrate. |
Advantages | Uniformity, strong adhesion, versatility, precise control. |
Applications | Electronics, optics, solar panels, decorative coatings. |
Types | DC, RF, and magnetron sputtering. |
Challenges | High cost, process complexity, material limitations. |
Discover how sputtering can enhance your manufacturing process—contact us today for expert advice!