Step coverage in thermal evaporation refers to the ability of the deposited thin film to uniformly cover the surface features of a substrate, including steps, trenches, and other topographical variations. It is a critical parameter in thin-film deposition processes, as poor step coverage can lead to non-uniform film thickness, voids, or incomplete coverage, which can affect the performance and reliability of the deposited layer. In thermal evaporation, step coverage is influenced by factors such as the deposition angle, substrate temperature, and the geometry of the substrate features. Achieving good step coverage is essential for applications requiring conformal coatings, such as in microelectronics and optical coatings.
Key Points Explained:
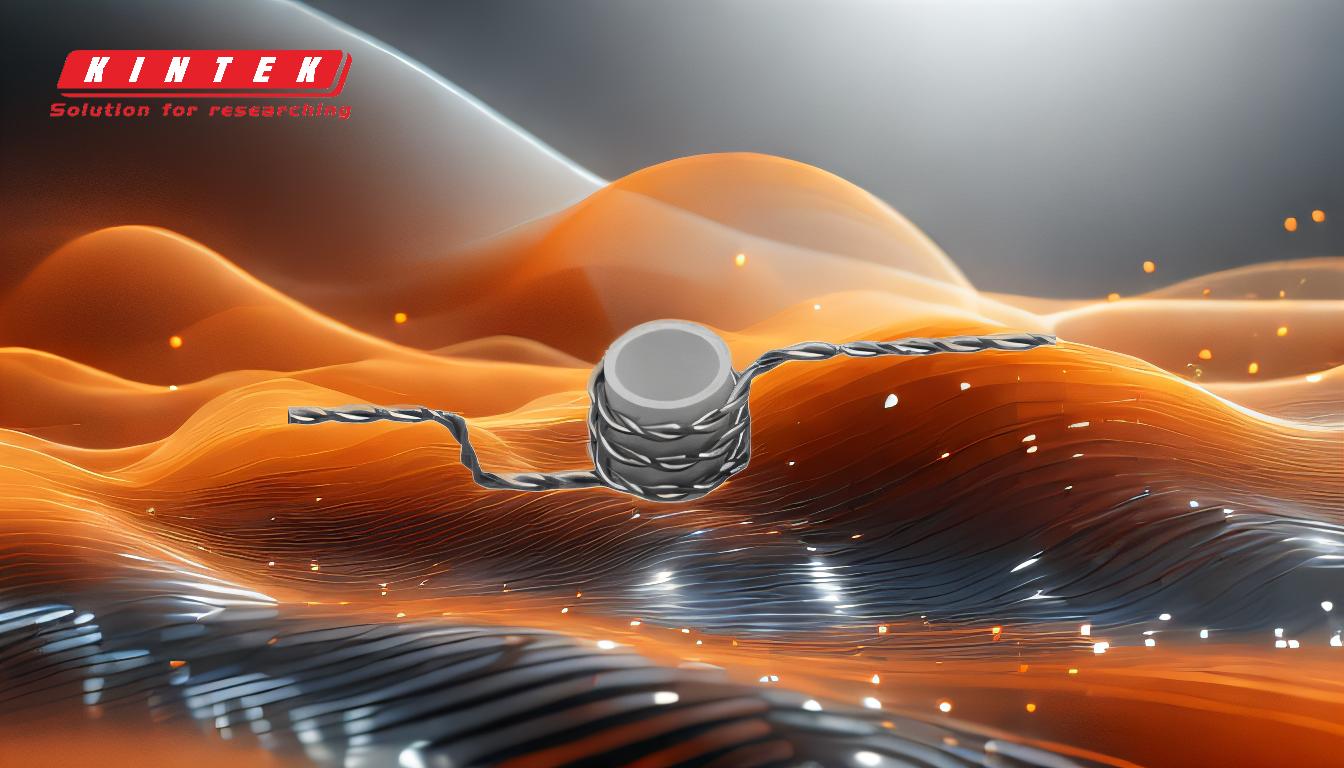
-
Definition of Step Coverage:
- Step coverage is a measure of how well a thin film conforms to the surface features of a substrate, particularly steps, trenches, and other three-dimensional structures.
- It is typically expressed as the ratio of the film thickness at the bottom of a feature (e.g., a trench) to the film thickness on the top surface.
- Poor step coverage can result in non-uniform film thickness, leading to defects such as voids, cracks, or incomplete coverage in critical areas.
-
Importance of Step Coverage in Thermal Evaporation:
- In thermal evaporation, step coverage is crucial for ensuring the reliability and functionality of thin-film devices, especially in microelectronics, where conformal coatings are required for interconnects, vias, and other structures.
- Poor step coverage can lead to electrical shorts, open circuits, or reduced device performance, particularly in high-aspect-ratio structures.
- Achieving good step coverage is also important in optical coatings, where uniform thickness is necessary for consistent optical properties.
-
Factors Affecting Step Coverage in Thermal Evaporation:
- Deposition Angle: Thermal evaporation is a line-of-sight process, meaning that the deposition flux arrives at the substrate from a specific direction. This can lead to shadowing effects, where features facing away from the evaporation source receive less material, resulting in poor step coverage.
- Substrate Geometry: The aspect ratio (depth-to-width ratio) of features on the substrate plays a significant role. High-aspect-ratio features are more challenging to coat uniformly due to limited access for the evaporant flux.
- Substrate Temperature: Higher substrate temperatures can improve step coverage by enhancing surface diffusion, allowing the deposited material to migrate and fill in gaps more effectively.
- Evaporation Rate and Pressure: The rate of evaporation and the pressure in the deposition chamber can influence the mean free path of the evaporant atoms, affecting their ability to reach and coat complex features.
-
Techniques to Improve Step Coverage:
- Planarization: Pre-treating the substrate to reduce the height of steps or trenches can improve step coverage by minimizing shadowing effects.
- Rotating Substrates: Rotating the substrate during deposition can help achieve more uniform coverage by exposing all features to the evaporant flux from multiple angles.
- Heating the Substrate: Increasing the substrate temperature can enhance surface diffusion, allowing the deposited material to spread more evenly over complex features.
- Using Collimated Evaporation Sources: Collimating the evaporant flux can direct the material more precisely onto the substrate, improving coverage in high-aspect-ratio features.
-
Comparison with Other Deposition Techniques:
- Compared to techniques like chemical vapor deposition (CVD) or atomic layer deposition (ALD), thermal evaporation generally has poorer step coverage due to its line-of-sight nature.
- CVD and ALD can achieve excellent step coverage, even in high-aspect-ratio structures, because they rely on chemical reactions or self-limiting processes that enable conformal deposition.
- However, thermal evaporation is still widely used for applications where high purity, high deposition rates, or specific material properties are required, despite its limitations in step coverage.
-
Applications Requiring Good Step Coverage:
- Microelectronics: In the fabrication of integrated circuits, good step coverage is essential for depositing conductive layers in vias and trenches, ensuring reliable electrical connections.
- Optical Coatings: Uniform step coverage is necessary for depositing anti-reflective, protective, or functional optical coatings on lenses, mirrors, and other components.
- MEMS and Sensors: Microelectromechanical systems (MEMS) and sensors often require conformal coatings to ensure proper functionality and reliability.
In summary, step coverage in thermal evaporation is a critical parameter that determines the uniformity and quality of thin films deposited on substrates with complex topographies. While thermal evaporation has limitations in achieving conformal coatings, various techniques and process optimizations can be employed to improve step coverage for specific applications. Understanding and controlling the factors that influence step coverage is essential for ensuring the performance and reliability of thin-film devices.
Summary Table:
Aspect | Details |
---|---|
Definition | Measure of thin film uniformity on substrate features like steps and trenches. |
Importance | Ensures reliability in microelectronics, optical coatings, and MEMS devices. |
Key Factors | Deposition angle, substrate geometry, temperature, evaporation rate, pressure. |
Improvement Techniques | Planarization, rotating substrates, heating, collimated evaporation sources. |
Comparison with CVD/ALD | Thermal evaporation has poorer step coverage but offers high purity and rates. |
Applications | Microelectronics, optical coatings, MEMS, and sensors. |
Optimize your thin-film deposition process—contact our experts today for tailored solutions!