The acceptable pressure drop across a filter is a critical parameter in filtration systems, as it directly impacts efficiency, energy consumption, and the lifespan of the filter. Pressure drop is influenced by factors such as the type of filter material, flow rate, viscosity of the fluid, and the filter's design. For fiber filter elements and metal wire wound filters, specific formulas are used to calculate the pressure drop, which help in determining the optimal operating conditions and ensuring the filter performs within acceptable limits. Understanding these calculations and their implications is essential for maintaining system efficiency and preventing premature filter failure.
Key Points Explained:
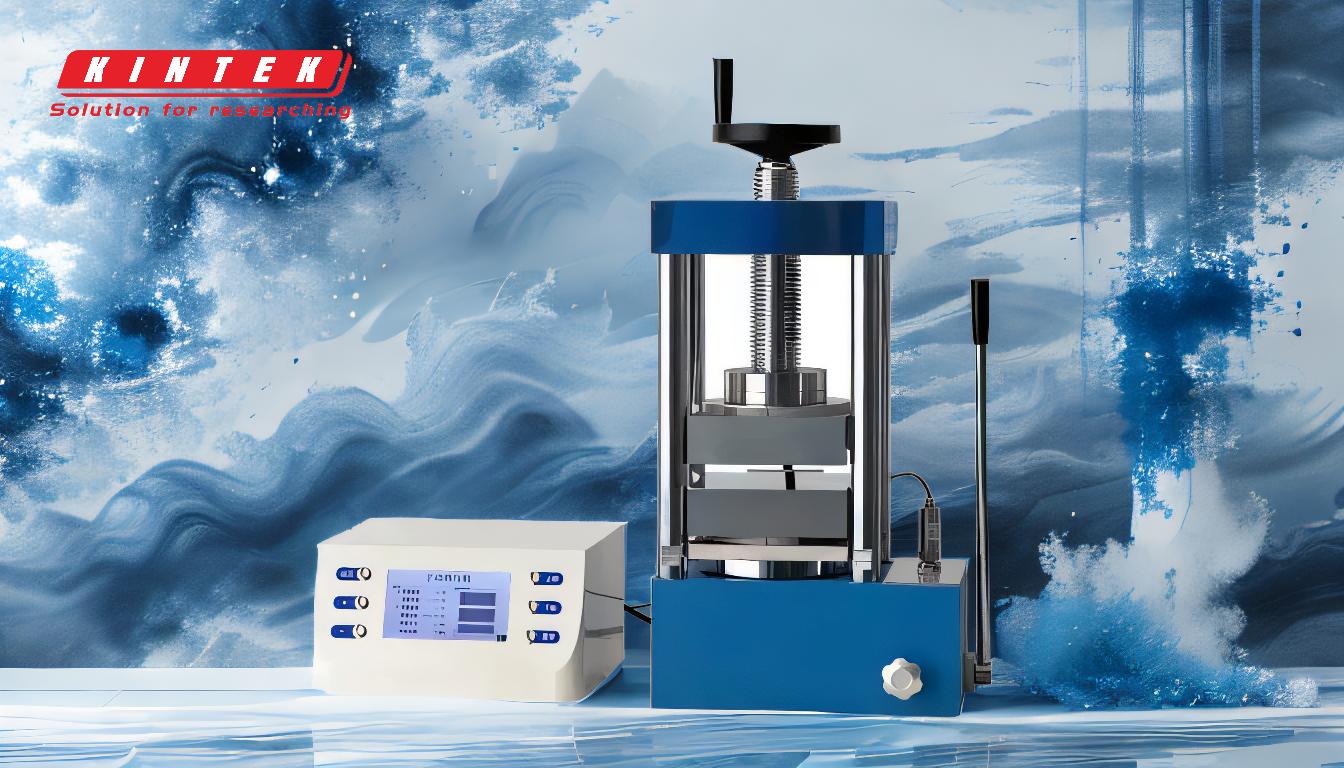
-
Understanding Pressure Drop in Filters:
- Pressure drop refers to the difference in pressure between the inlet and outlet of a filter. It is a measure of the resistance the filter offers to the flow of fluid.
- A higher pressure drop indicates greater resistance, which can lead to increased energy consumption and potential damage to the filter or the system.
- Acceptable pressure drop values vary depending on the application, filter type, and system requirements. Typically, filters are designed to operate within a specific pressure drop range to ensure optimal performance.
-
Factors Affecting Pressure Drop:
- Flow Rate (Q): Higher flow rates generally result in higher pressure drops due to increased fluid velocity through the filter.
- Viscosity (μ): Fluids with higher viscosity experience greater resistance, leading to higher pressure drops.
- Filter Material and Design: Different materials (e.g., fiber, metal wire) and designs (e.g., wound filters) have varying filtration capacities and resistance characteristics.
- Filter Area (A): A larger filter area can reduce pressure drop by distributing the flow over a greater surface area.
-
Pressure Drop Calculation for Fiber Filter Elements:
- The formula for calculating pressure drop in fiber filter elements is:
[ \triangle P1 = \frac{Q\mu}{A \times Kx \times 10^8} ] - Here, (Kx) represents the total filtration capacity of the fiber filter material, which includes materials like plant fiber, fiberglass, and non-woven fabric.
- This formula helps in determining the pressure drop based on the flow rate, viscosity, filter area, and material properties.
- The formula for calculating pressure drop in fiber filter elements is:
-
Pressure Drop Calculation for Metal Wire Wound Filters:
- The formula for metal wire wound filters is:
[ \triangle P1 = \frac{Q\mu}{\pi ds L_1 \times Kx \times 10^6} ] - In this formula, (ds) is the diameter of the outer circle of the winding frame, and (L_1) is the winding core length. (Kx) is the filtration capacity coefficient specific to the winding filter element.
- This calculation is particularly useful for understanding how the geometry and material of wound filters influence pressure drop.
- The formula for metal wire wound filters is:
-
Interpreting the Results:
- Once the pressure drop is calculated, it should be compared against the acceptable range specified by the filter manufacturer or system requirements.
- If the calculated pressure drop exceeds the acceptable limit, it may indicate the need for a larger filter area, a different filter material, or a reduction in flow rate.
- Regular monitoring of pressure drop can help in identifying clogging or fouling of the filter, enabling timely maintenance or replacement.
-
Practical Implications:
- Maintaining an acceptable pressure drop is crucial for energy efficiency. High pressure drops lead to increased pumping costs and potential system downtime.
- Filters with lower pressure drops are generally preferred, but they must also meet the required filtration efficiency and capacity.
- Understanding the relationship between pressure drop and filter performance allows for better system design and optimization.
By applying these formulas and principles, you can effectively manage the pressure drop across filters, ensuring they operate within acceptable limits and contribute to the overall efficiency and longevity of the filtration system.
Summary Table:
Key Factor | Impact on Pressure Drop |
---|---|
Flow Rate (Q) | Higher flow rates increase pressure drop due to greater fluid velocity. |
Viscosity (μ) | Higher viscosity fluids result in higher pressure drops. |
Filter Material/Design | Different materials and designs affect resistance and filtration capacity. |
Filter Area (A) | Larger filter areas reduce pressure drop by distributing flow over more surface area. |
Filtration Capacity (Kx) | Specific to filter material, influences pressure drop calculations. |
Need help calculating or optimizing pressure drop in your filtration system? Contact our experts today!