Chemical vapor deposition (CVD) offers several advantages over oxidation, particularly in terms of versatility, precision, and material properties. CVD allows for the production of high-purity thin films, both crystalline and amorphous, with controlled chemical and physical properties. It is highly adaptable, enabling the deposition of coatings on a wide range of materials, including ceramics, metals, and glass. CVD also provides excellent control over process parameters, such as temperature, pressure, and gas flow, ensuring uniform and durable coatings. Additionally, CVD is scalable and suitable for creating ultra-thin layers, making it ideal for applications like electrical circuits and high-stress environments.
Key Points Explained:
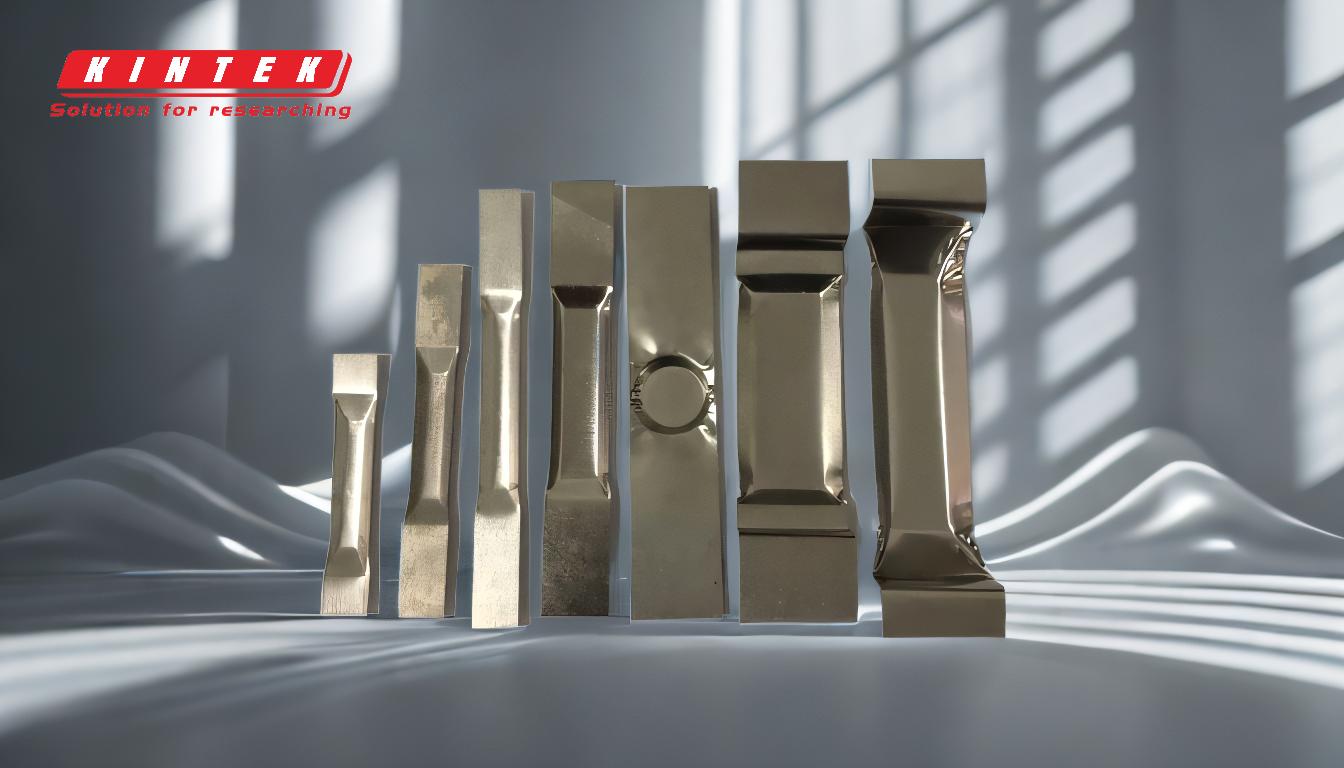
-
High Purity and Versatility in Material Synthesis
- CVD enables the production of high-purity single- or polycrystalline thin films, as well as amorphous films. This is achieved through precise control of chemical reactions and process parameters.
- Unlike oxidation, which is limited to forming oxide layers, CVD can synthesize a wide range of materials, including ceramics, metals, and glass, with tailored properties such as corrosion resistance, abrasion resistance, or high purity.
-
Control Over Process Parameters
- CVD allows for full control over critical parameters such as temperature, pressure, gas flow rate, and gas concentration. This level of control ensures consistent and uniform coatings, which is particularly important for precision applications.
- Oxidation, on the other hand, is less flexible and typically relies on thermal processes that may not offer the same level of precision or adaptability.
-
Ability to Coat Complex and Precision Surfaces
- CVD is highly effective at coating complex and precision surfaces, making it suitable for advanced applications like electrical circuits and microelectronics.
- The process can create ultra-thin layers of material, which are essential for modern technologies. Oxidation processes are generally less capable of achieving such fine control over layer thickness and uniformity.
-
Durability and Performance in Extreme Conditions
- CVD coatings are known for their durability and ability to withstand high-stress environments, extreme temperatures, and temperature variations.
- This makes CVD a preferred choice for applications requiring long-term performance and reliability, where oxidation may not provide the same level of durability.
-
Scalability and Uniformity
- CVD is highly scalable, making it suitable for both small-scale and large-scale production. The process ensures uniform deposition across large areas, which is critical for industrial applications.
- Oxidation processes often lack this scalability and uniformity, particularly when dealing with large or complex substrates.
-
Broad Applicability Across Industries
- CVD's ability to deposit coatings on a wide range of materials and its adaptability to different chemical reactions make it a versatile tool across industries, including electronics, aerospace, and manufacturing.
- Oxidation is more limited in its applicability, primarily serving as a surface treatment for specific materials like metals.
In summary, CVD's advantages over oxidation include superior control over material properties, the ability to coat complex surfaces, and the production of durable, high-performance coatings. These qualities make CVD a preferred choice for advanced applications requiring precision, scalability, and reliability.
Summary Table:
Advantage | CVD | Oxidation |
---|---|---|
Material Versatility | Deposits on ceramics, metals, glass, and more | Limited to forming oxide layers on specific materials |
Control Over Process Parameters | Precise control of temperature, pressure, gas flow, and concentration | Less flexible, relies on thermal processes |
Coating Complexity | Coats complex and precision surfaces effectively | Limited ability to coat intricate surfaces |
Durability | Withstands high-stress environments and extreme conditions | Less durable in extreme environments |
Scalability | Suitable for both small- and large-scale production | Limited scalability, especially for large or complex substrates |
Industry Applications | Widely used in electronics, aerospace, and manufacturing | Primarily used for surface treatment of metals |
Unlock the full potential of CVD for your applications—contact our experts today!