Magnetically assisted sputtering, also known as magnetron sputtering, is a highly efficient and versatile thin-film deposition technique that offers numerous advantages over traditional sputtering methods. By using magnetic fields to trap secondary electrons near the target surface, it enhances ionization efficiency, increases deposition rates, and improves film quality. This method is suitable for a wide range of materials, including metals and insulators, and is widely used in industries such as microelectronics, optics, and wear-resistant coatings. Its ability to produce uniform, high-purity films with precise thickness control makes it a preferred choice for both research and industrial applications.
Key Points Explained:
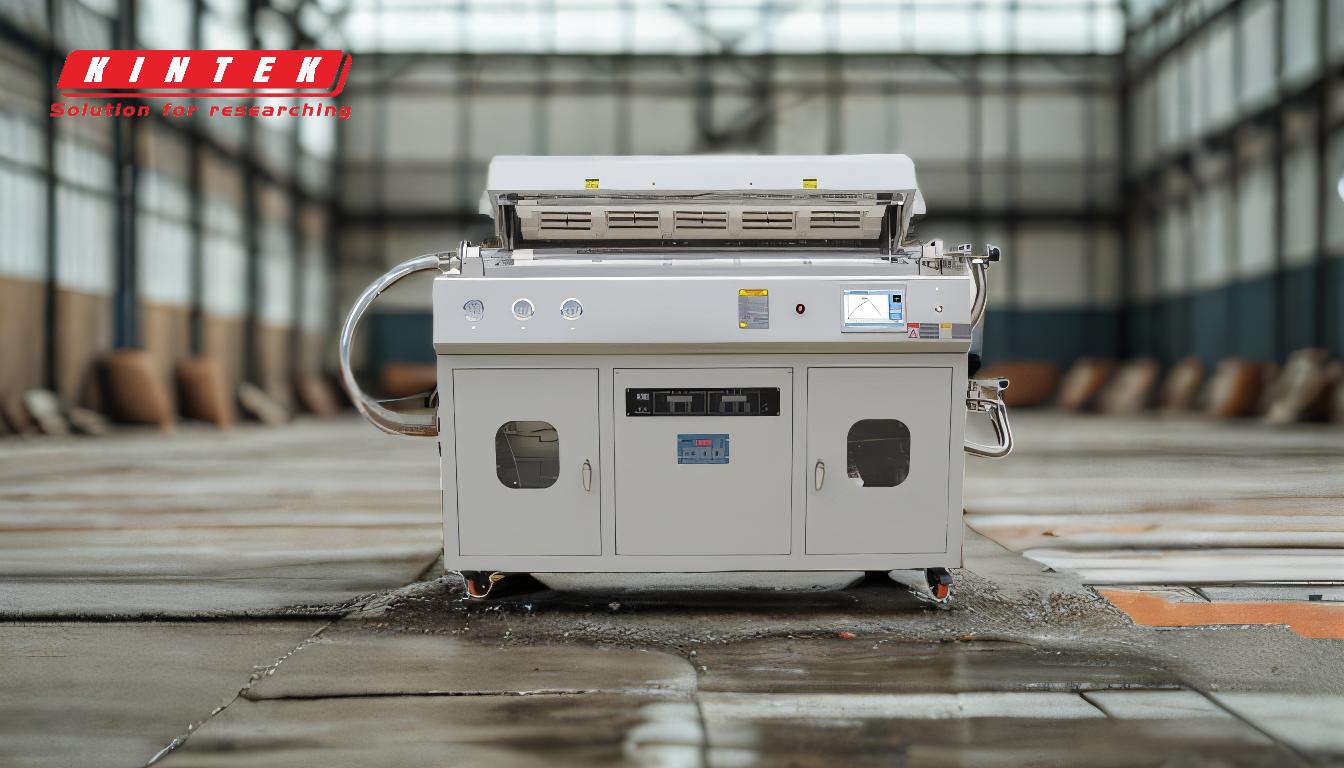
-
Enhanced Ionization and Plasma Density:
- Magnetically assisted sputtering uses magnetic fields to confine secondary electrons near the target surface.
- This confinement increases the ionization of argon gas, creating a denser plasma.
- Higher plasma density leads to more efficient sputtering and faster deposition rates.
-
Lower Pressure Operation:
- The magnetic field allows the process to operate at lower pressures compared to conventional sputtering.
- Lower pressure reduces contamination and improves the purity of the deposited films.
-
High Deposition Rates:
- The increased ionization and plasma density result in higher sputtering rates.
- This makes magnetron sputtering faster and more efficient than traditional methods.
-
Precision and Uniformity:
- Magnetron sputtering provides excellent control over film thickness, with variations of less than 2% across the substrate.
- It ensures uniform deposition over large areas, making it ideal for industrial applications.
-
Versatility in Material Deposition:
- Unlike thermal evaporation, magnetron sputtering does not require heating or melting of the target material.
- It can deposit a wide range of materials, including metals, insulators, and compounds, regardless of their melting points.
-
High-Quality Films:
- The process produces dense, high-purity films with excellent adhesion to the substrate.
- Films deposited using magnetron sputtering are free from defects and have superior mechanical, optical, and electrical properties.
-
Low-Temperature Deposition:
- Magnetron sputtering operates at relatively low temperatures, preventing damage to temperature-sensitive substrates.
- This makes it suitable for applications in microelectronics and semiconductor manufacturing.
-
Cost-Effectiveness:
- The high deposition rates and ability to produce large quantities of films make magnetron sputtering a cost-effective solution.
- It reduces production time and material waste, lowering overall manufacturing costs.
-
Multiple Configurations:
- Magnetron sputtering systems can be configured with multiple targets, allowing for the deposition of multi-layer or composite films.
- RF magnetron sputtering extends the technique to non-conductive materials, further broadening its applicability.
-
Industry Applications:
- Magnetically assisted sputtering is used in various industries for applications such as wear-resistant coatings, corrosion protection, and functional coatings.
- It is particularly valuable in microelectronics for depositing dielectric and nitride films.
In summary, magnetically assisted sputtering combines efficiency, precision, and versatility, making it a superior thin-film deposition technique for both research and industrial applications. Its ability to produce high-quality, uniform films at lower costs and temperatures ensures its continued dominance in the field.
Summary Table:
Key Feature | Description |
---|---|
Enhanced Ionization | Magnetic fields increase plasma density, improving sputtering efficiency. |
Lower Pressure Operation | Reduces contamination, ensuring high-purity films. |
High Deposition Rates | Faster and more efficient than traditional methods. |
Precision and Uniformity | Film thickness control with less than 2% variation across substrates. |
Versatility in Materials | Deposits metals, insulators, and compounds without melting. |
High-Quality Films | Produces dense, defect-free films with superior properties. |
Low-Temperature Deposition | Ideal for temperature-sensitive substrates in microelectronics. |
Cost-Effectiveness | Reduces production time and material waste, lowering costs. |
Multiple Configurations | Supports multi-layer and composite films, including non-conductive materials. |
Industry Applications | Used in microelectronics, optics, wear-resistant coatings, and more. |
Unlock the potential of magnetically assisted sputtering for your applications—contact our experts today!