Physical Vapor Deposition (PVD) and Chemical Vapor Deposition (CVD) are both widely used techniques for creating thin films and coatings on substrates. However, PVD offers several advantages over CVD, particularly in terms of temperature resistance, environmental impact, surface finish, and durability. PVD coatings are applied at lower temperatures, produce no harmful by-products, and replicate the original surface finish of the substrate. Additionally, PVD coatings are more durable, wear-resistant, and capable of withstanding higher temperatures. These advantages make PVD a preferred choice in industries where precision, environmental considerations, and durability are critical.
Key Points Explained:
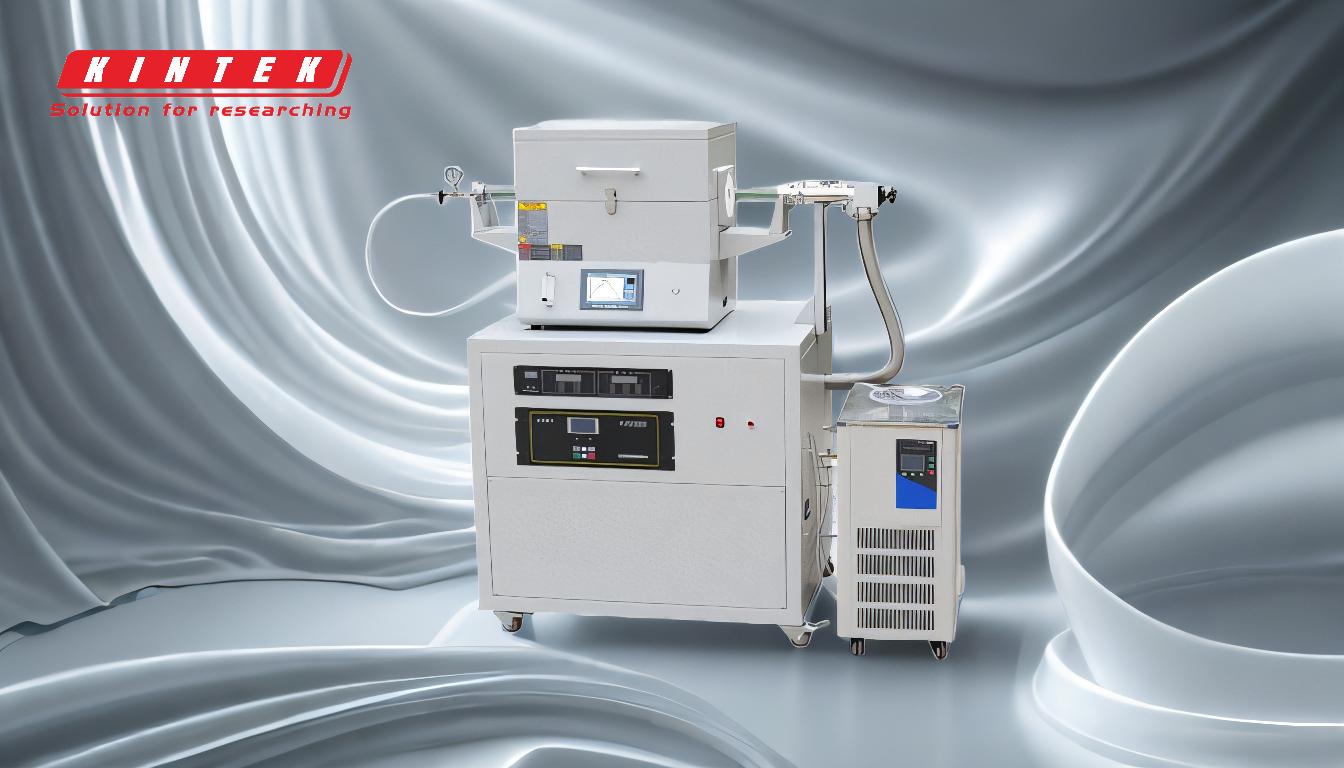
-
Temperature Resistance and Application Conditions:
- PVD coatings are applied at relatively low temperatures (250°C~450°C), making them suitable for heat-sensitive materials. CVD, on the other hand, requires higher temperatures (450°C to 1050°C), which can limit its applicability to materials that can withstand such conditions.
- PVD-coated parts do not require heat treatment after coating, simplifying the manufacturing process and reducing energy consumption.
-
Environmental Friendliness:
- PVD is an environmentally friendly process that produces no harmful by-products. In contrast, CVD involves chemical reactions that can generate toxic by-products, requiring specialized equipment and handling procedures to mitigate environmental and safety risks.
- The absence of chemical reactions in PVD makes it a cleaner and more sustainable option, aligning with the growing emphasis on environmentally conscious manufacturing practices.
-
Surface Finish and Precision:
- PVD replicates the original surface finish of the substrate, maintaining the part's aesthetic and functional properties. This is particularly important for applications where surface smoothness and precision are critical.
- CVD typically results in a matte finish unless the part is polished, which can add additional steps and costs to the manufacturing process.
-
Durability and Wear Resistance:
- PVD coatings are known for their durability, abrasion resistance, and impact resistance. These properties make PVD coatings ideal for applications requiring long-lasting performance under harsh conditions.
- PVD films can withstand high temperatures and provide excellent wear resistance, making them suitable for use in demanding environments such as aerospace, automotive, and industrial machinery.
-
Material Versatility and Process Simplicity:
- While CVD can be applied to a wider range of materials, PVD offers greater simplicity in terms of process control and equipment requirements. PVD involves the physical vaporization of solid materials, which is easier to manage compared to the complex chemical reactions involved in CVD.
- PVD's line-of-sight deposition ensures precise control over the coating thickness and uniformity, which is advantageous for applications requiring high precision.
-
Economic and Operational Advantages:
- The lower operating temperatures and absence of harmful by-products in PVD reduce operational costs and regulatory compliance burdens. This makes PVD a more cost-effective and manageable option for many manufacturers.
- PVD equipment is generally less specialized and easier to maintain compared to CVD equipment, which often requires additional safety measures and waste management systems.
In summary, PVD offers significant advantages over CVD in terms of temperature resistance, environmental impact, surface finish, durability, and operational simplicity. These benefits make PVD a preferred choice for industries prioritizing precision, sustainability, and long-term performance.
Summary Table:
Aspect | PVD | CVD |
---|---|---|
Temperature Resistance | Applied at lower temperatures (250°C~450°C), suitable for heat-sensitive materials. | Requires higher temperatures (450°C~1050°C), limiting material options. |
Environmental Impact | No harmful by-products, environmentally friendly. | Generates toxic by-products, requiring specialized handling. |
Surface Finish | Replicates original surface finish, maintaining precision and aesthetics. | Typically results in a matte finish unless polished. |
Durability | More durable, wear-resistant, and capable of withstanding high temperatures. | Less durable compared to PVD. |
Process Simplicity | Easier process control and equipment requirements. | Complex chemical reactions and specialized equipment needed. |
Economic Benefits | Lower operational costs and regulatory compliance burdens. | Higher costs due to safety measures and waste management. |
Ready to explore how PVD can elevate your manufacturing process? Contact us today to learn more!