The thermal evaporation method offers several advantages over the sputtering method, particularly in terms of simplicity, efficiency, and suitability for specific applications. Thermal evaporation involves heating a material in a vacuum until it evaporates, allowing the vaporized atoms to deposit onto a substrate, forming a thin film. This method is known for its low temperature differences and short product contact times, making it ideal for heat-sensitive products. It is also efficient for outgassing and reloading metal charges, and it automatically terminates evaporation before less volatile impurities can contaminate the film. In contrast, sputtering involves bombarding a target material with ions to eject atoms, which then deposit onto the substrate. While sputtering is highly reproducible and environmentally friendly, thermal evaporation is often preferred for its ability to create alloys, its simplicity, and its lower operational complexity.
Key Points Explained:
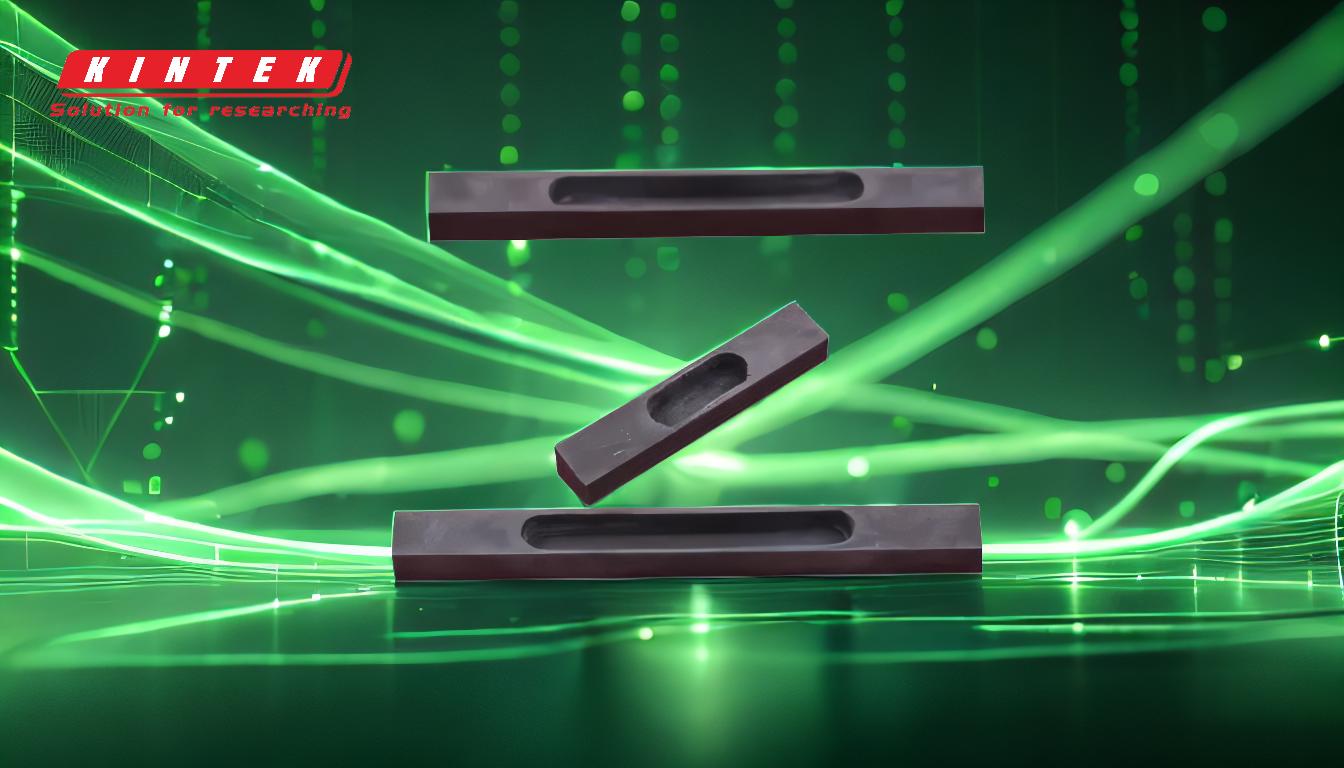
-
Simplicity and Ease of Operation:
- Thermal evaporation is straightforward, involving heating a material in a vacuum until it evaporates and deposits onto a substrate. This process is less complex compared to sputtering, which requires precise control of ion bombardment and plasma generation.
- The use of a resistance boat or coil in thermal evaporation simplifies the setup, making it easier to operate and maintain.
-
Efficiency and Outgassing:
- Thermal evaporation is highly efficient, with the ability to outgas materials effectively, ensuring a clean deposition process. This is particularly important for applications requiring high-purity films.
- The method automatically terminates evaporation before less volatile impurities can evaporate, ensuring the purity of the deposited film.
-
Suitability for Heat-Sensitive Products:
- Due to its low temperature differences and short product contact times, thermal evaporation is ideal for heat-sensitive products. This minimizes the risk of thermal damage to the substrate or the material being deposited.
-
Creation of Alloys and Sequential Coatings:
- Thermal evaporation allows for the creation of alloys by using multiple sources, enabling the deposition of complex material compositions.
- Sequential coatings can be performed using either evaporation or sputtering, depending on the coater's configuration, providing flexibility in film deposition.
-
Industrial Applications:
- Thermal evaporation is widely used in various industrial applications, including the creation of metal bonding layers in solar cells, thin-film transistors, semiconductor wafers, and carbon-based OLEDs. Its versatility makes it a preferred choice for many thin-film deposition processes.
-
Comparison with Sputtering:
- While sputtering is highly reproducible and allows for precise deposition of small quantities of oxides, metals, and alloys, it is more complex and requires more sophisticated equipment.
- Thermal evaporation, on the other hand, is simpler, more cost-effective, and better suited for applications requiring high purity and minimal thermal impact.
In summary, the thermal evaporation method offers significant advantages over sputtering, particularly in terms of simplicity, efficiency, and suitability for heat-sensitive applications. Its ability to create alloys and perform sequential coatings further enhances its versatility in thin-film deposition processes. For more detailed information on thermal evaporation, you can visit thermal evaporation.
Summary Table:
Aspect | Thermal Evaporation | Sputtering |
---|---|---|
Simplicity | Straightforward process with minimal setup complexity. | Requires precise control of ion bombardment and plasma generation. |
Efficiency | Efficient outgassing and automatic termination to ensure high-purity films. | Highly reproducible but less efficient for outgassing. |
Heat Sensitivity | Ideal for heat-sensitive products due to low temperature differences. | May cause thermal damage to sensitive substrates. |
Alloy Creation | Allows creation of alloys using multiple sources. | Limited flexibility for alloy creation. |
Industrial Applications | Widely used in solar cells, thin-film transistors, semiconductor wafers, and OLEDs. | Suitable for precise deposition of oxides, metals, and alloys. |
Cost and Complexity | Cost-effective and simpler to operate. | More complex and requires sophisticated equipment. |
Interested in leveraging thermal evaporation for your applications? Contact our experts today to learn more!