Catalytic pyrolysis is a versatile and innovative process with significant applications in waste management, renewable energy production, and resource recovery. It involves the thermal decomposition of organic materials, such as plastic waste or biomass, in the presence of a catalyst to produce valuable products like liquid fuels, syngas, and char. This process not only addresses environmental concerns by reducing waste but also contributes to the production of renewable energy and chemicals. By leveraging catalysts like modified natural zeolite, catalytic pyrolysis enhances the efficiency and selectivity of the process, making it a sustainable solution for converting waste into useful resources.
Key Points Explained:
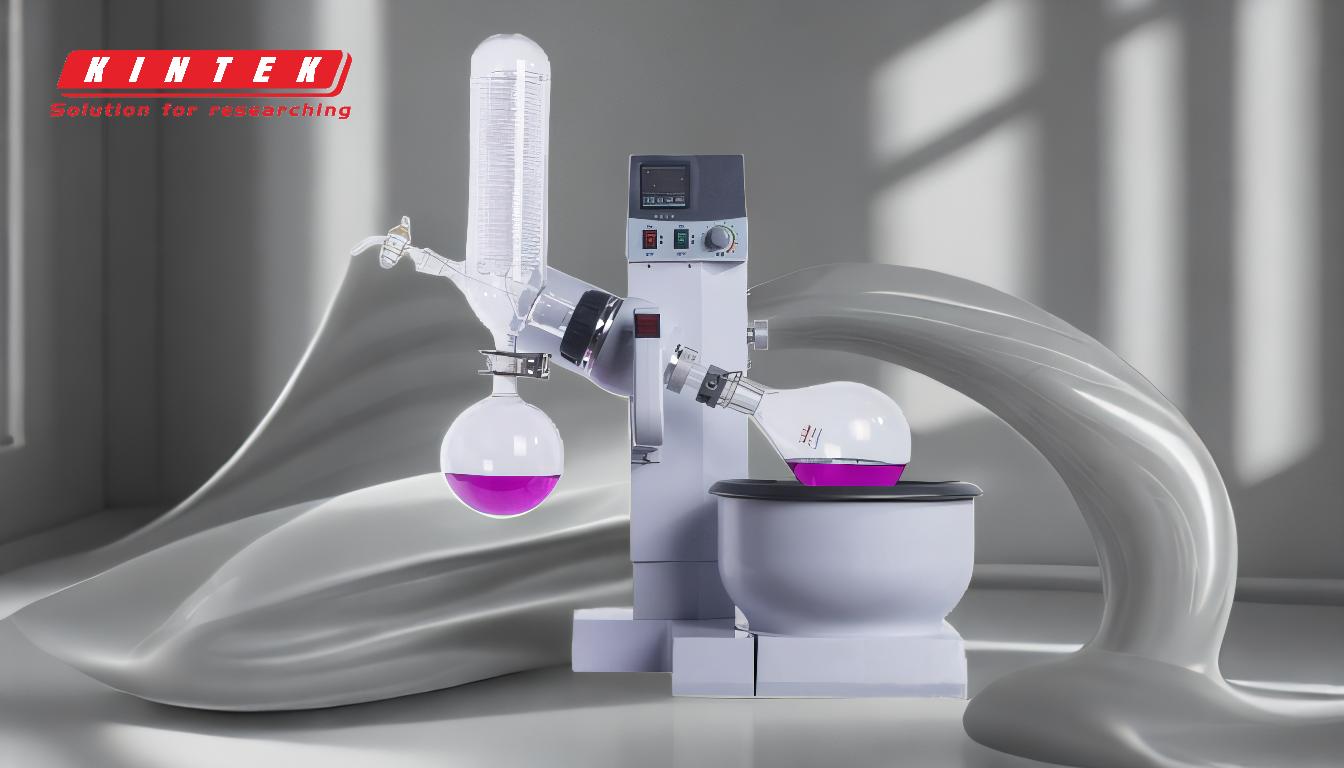
-
Conversion of Plastic Waste into Liquid Oil
- Catalytic pyrolysis is a promising method for transforming plastic waste into liquid oil, which can be used as fuel or feedstock for chemical production.
- The use of a catalyst, such as modified natural zeolite (NZ), improves the efficiency and quality of the oil produced.
- This application helps reduce plastic pollution and provides an alternative to fossil fuels, contributing to a circular economy.
-
Production of Biofuel from Biomass
- Fast pyrolysis, a subset of catalytic pyrolysis, is used to convert biomass (e.g., grasses, agricultural residues) into bio-oil, char, and flammable gases.
- The process involves heating biomass to around 500°C in the absence of oxygen and then rapidly cooling the products.
- Bio-oil is the primary product and can be refined into renewable fuels, making it a key component of sustainable energy systems.
-
Generation of Syngas and Char from Organic Waste
- Pyrolysis, including catalytic pyrolysis, is employed to extract energy from organic waste by producing syngas and char.
- Syngas, a mixture of hydrogen, methane, and other combustible gases, can be used as a fuel or chemical feedstock.
- Char, a solid byproduct, can be utilized as a soil amendment or solid fuel, adding value to the process.
-
Environmental and Economic Benefits
- Catalytic pyrolysis reduces the volume of waste in landfills and minimizes greenhouse gas emissions by converting waste into useful products.
- The process supports renewable energy production, reducing reliance on fossil fuels and promoting energy security.
- By producing value-added products like liquid oil, biofuel, and syngas, catalytic pyrolysis creates economic opportunities and supports sustainable development.
-
Role of Catalysts in Enhancing Efficiency
- Catalysts like modified natural zeolite play a critical role in improving the yield and quality of products from catalytic pyrolysis.
- They lower the activation energy required for the reaction, making the process more energy-efficient.
- Catalysts also enhance selectivity, ensuring the production of desired products while minimizing unwanted byproducts.
-
Applications in Renewable Energy Systems
- Catalytic pyrolysis is a key technology in the transition to renewable energy systems, providing a sustainable way to produce biofuels and chemicals.
- It complements other renewable energy technologies by converting waste materials into energy-dense products.
- The process aligns with global efforts to reduce carbon emissions and achieve climate goals.
By addressing waste management challenges and contributing to renewable energy production, catalytic pyrolysis offers a sustainable and economically viable solution for modern energy and environmental needs.
Summary Table:
Key Application | Key Benefits |
---|---|
Conversion of Plastic Waste | Produces liquid oil for fuel/chemicals; reduces plastic pollution. |
Biofuel Production from Biomass | Generates bio-oil, char, and gases for renewable energy systems. |
Syngas and Char from Organic Waste | Extracts energy from waste; produces syngas (fuel/chemicals) and char (soil/fuel). |
Environmental & Economic Benefits | Reduces landfill waste, greenhouse gases, and reliance on fossil fuels. |
Role of Catalysts | Enhances efficiency, yield, and selectivity of the pyrolysis process. |
Renewable Energy Systems | Supports sustainable energy production and aligns with climate goals. |
Learn how catalytic pyrolysis can transform waste into valuable resources—contact us today for expert guidance!