Plasma-Enhanced Chemical Vapor Deposition (PECVD) is a highly advantageous thin-film deposition technique widely used in semiconductor manufacturing, optoelectronics, MEMS, and other advanced technologies. Its primary benefit lies in its ability to deposit high-quality films at low temperatures, preserving the integrity of temperature-sensitive substrates. PECVD offers excellent film uniformity, high packing density, and strong adhesion, making it suitable for a variety of applications. Additionally, it provides high deposition rates, controllable parameters, and the ability to produce films with tailored optical, mechanical, and thermal properties. These features make PECVD a cost-effective and versatile solution for modern thin-film fabrication.
Key Points Explained:
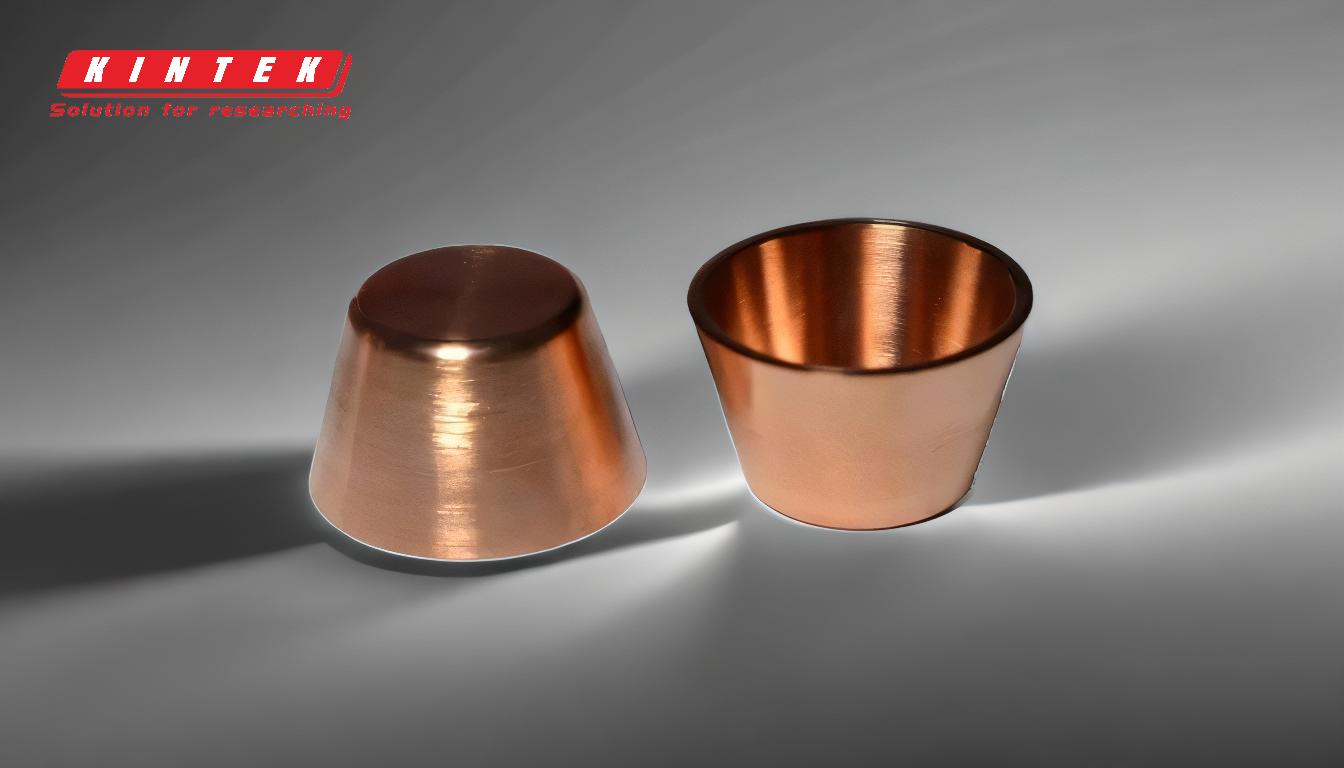
-
Low Deposition Temperature
- PECVD operates at temperatures below 400°C, significantly lower than traditional CVD methods.
- This low-temperature capability is critical for depositing films on temperature-sensitive substrates, such as polymers or pre-fabricated semiconductor devices, without damaging their structure or physical properties.
- It enables the use of a wider range of substrates, including those that cannot withstand high-temperature processes.
-
Excellent Film Properties
- Films deposited by PECVD exhibit high packing density (∼ 98%), making them hard, environmentally stable, and resistant to wear and corrosion.
- The films have dense structures with few pinholes, ensuring excellent barrier properties and protection against environmental factors.
- They also demonstrate strong adhesion to substrates, which is essential for long-term reliability in applications like protective coatings and optical devices.
-
Versatility in Material Deposition
- PECVD can deposit a wide range of materials, including elemental, alloy, glassy, and compound films.
- It allows for the fabrication of graded or inhomogeneous films, which are useful for optical devices and multifunctional systems.
- The technique can produce films with varying microstructures, from amorphous to polycrystalline to single crystal, depending on the application requirements.
-
High Deposition Rates and Efficiency
- PECVD achieves high deposition rates, making it a cost-effective and time-efficient process.
- Reactions primarily occur on the cathode surface, reducing reactant loss and increasing deposition efficiency.
- This high throughput is particularly beneficial for industrial-scale manufacturing.
-
Uniformity and Step Coverage
- PECVD provides excellent thickness and composition uniformity across complex surfaces, ensuring consistent film properties.
- It offers superior step coverage, which is crucial for coating intricate geometries in MEMS and semiconductor devices.
-
Controllable Process Parameters
- PECVD allows precise control over deposition parameters, such as discharge methods, voltage, current density, and ventilation.
- Electromagnetic fields can be used to manipulate the movement and energy of charged particles in the plasma, enabling tailored film properties.
- Advanced techniques like arc-PECVD can deposit difficult-to-obtain film materials, further expanding its capabilities.
-
Broad Application Range
- PECVD is widely used in very large-scale integrated circuits (VLSI), optoelectronic devices, MEMS, and protective coatings.
- It is compatible with other vacuum processes, making it a versatile tool in multi-step fabrication workflows.
- Its ability to produce films with desired optical, mechanical, and thermal properties makes it suitable for a variety of high-tech applications.
-
Cost-Effectiveness
- The combination of low-temperature processing, high deposition rates, and excellent film quality makes PECVD a reliable and cost-effective technology.
- It reduces the need for expensive post-processing steps, such as annealing, further lowering production costs.
In summary, PECVD's low-temperature operation, excellent film properties, versatility, and cost-effectiveness make it an indispensable tool in modern thin-film fabrication. Its ability to meet the demanding requirements of advanced technologies ensures its continued relevance in industries ranging from semiconductors to optoelectronics.
Summary Table:
Advantage | Description |
---|---|
Low Deposition Temperature | Operates below 400°C, ideal for temperature-sensitive substrates. |
Excellent Film Properties | High packing density, strong adhesion, and environmental stability. |
Versatility in Materials | Deposits elemental, alloy, glassy, and compound films with tailored properties. |
High Deposition Rates | Ensures cost-effective and time-efficient industrial-scale manufacturing. |
Uniformity & Step Coverage | Provides consistent film properties across complex surfaces. |
Controllable Parameters | Enables precise tuning of film properties for specific applications. |
Broad Application Range | Used in VLSI, optoelectronics, MEMS, and protective coatings. |
Cost-Effectiveness | Reduces production costs with low-temperature processing and high efficiency. |
Unlock the potential of PECVD for your applications—contact our experts today!