The capacity of a pyrolysis machine varies significantly based on its type, design, and operational mode. Continuous pyrolysis plants, such as those used for tyre pyrolysis, have a larger capacity and can operate 24/7 for extended periods, making them suitable for large-scale industrial applications. In contrast, small-scale or batch pyrolysis machines, often used for biomass or waste processing, have a smaller capacity and require downtime for cooling and discharging, making them more suitable for smaller operations. The choice of pyrolysis machine depends on factors such as the desired output, operational efficiency, and environmental considerations.
Key Points Explained:
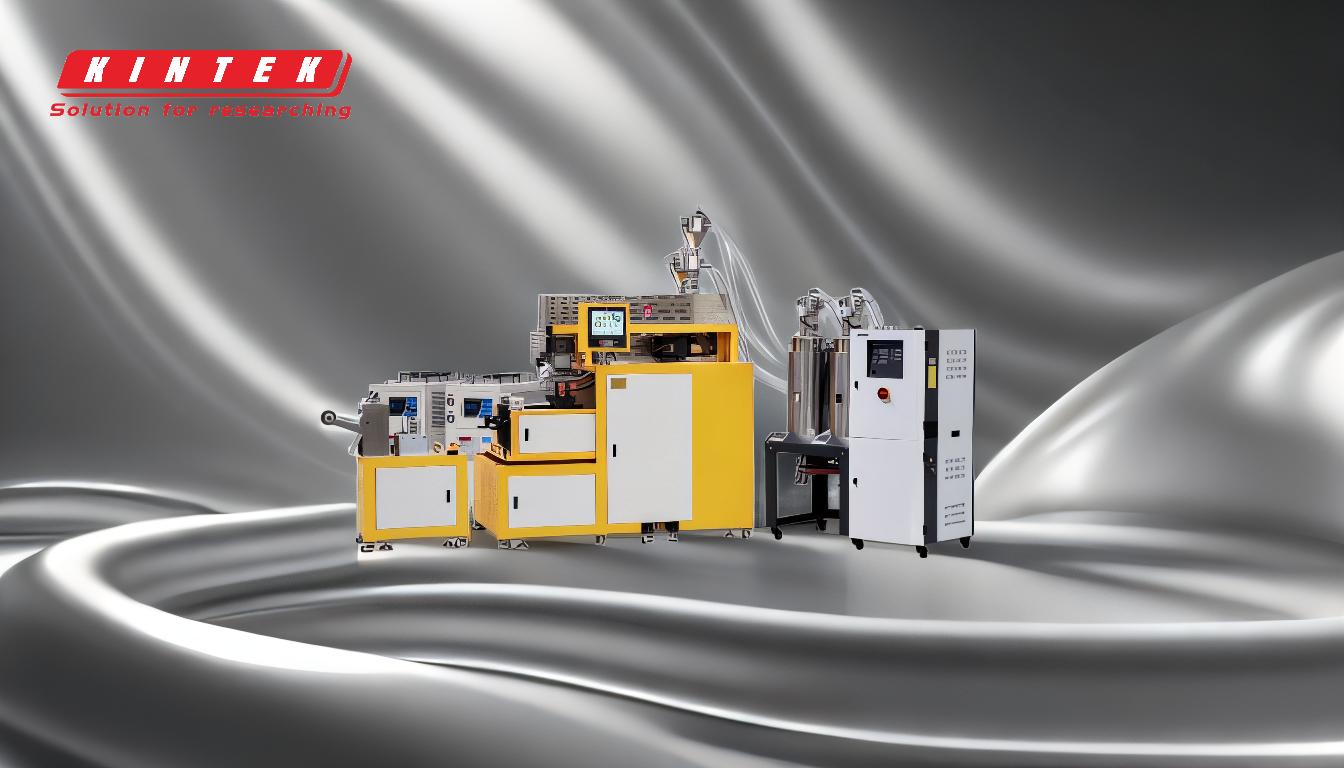
-
Types of Pyrolysis Machines and Their Capacities:
- Continuous Pyrolysis Plants: These machines are designed for large-scale operations and can process materials continuously without interruption. They are ideal for industries requiring high throughput, such as tyre recycling. For example, a continuous tyre pyrolysis plant can operate 24 hours a day and run continuously for over 30 days.
- Batch Pyrolysis Machines: These are smaller-scale machines that process materials in batches. A typical batch in a small pyrolysis machine takes about 10 hours for the reaction, 7 hours for cooling, and 2 hours for discharging, totaling approximately 19 hours per batch. This makes them suitable for smaller operations or businesses with limited processing needs.
-
Design and Operational Efficiency:
- Continuous Pyrolysis Plants: These machines are designed for efficiency and high output. Their continuous operation reduces downtime and maximizes productivity, making them cost-effective for large-scale applications.
- Batch Pyrolysis Machines: While these machines have a smaller capacity, they are often more flexible and easier to manage for smaller operations. The downtime between batches allows for cooling and maintenance, ensuring the machine's longevity.
-
Material and Construction:
- Biomass Pyrolysis Machines: These machines often feature a double-layer main drum structure made of stainless steel, which is resistant to high temperatures and corrosion. This design enhances thermal efficiency and extends the equipment's service life.
- Environmental Considerations: Modern pyrolysis machines, especially those used for biomass, are designed to be smoke-free and pollution-free, aligning with national environmental protection policies. This makes them an environmentally friendly option for waste processing.
-
Customization and Flexibility:
- Small-Scale Pyrolysis Equipment: These machines offer a variety of options, including skid-mounted pyrolysis plants, batch type, semi-continuous, and fully continuous models. This flexibility allows customers to choose the model that best fits their specific needs and operational scale.
-
Applications and Suitability:
- Continuous Pyrolysis Plants: Best suited for large-scale industrial applications where high throughput and continuous operation are required.
- Batch Pyrolysis Machines: Ideal for smaller operations, research and development, or businesses with fluctuating processing needs.
In summary, the capacity of a pyrolysis machine is influenced by its type, design, and operational mode. Continuous pyrolysis plants offer high capacity and efficiency for large-scale operations, while batch pyrolysis machines provide flexibility and suitability for smaller-scale applications. The choice of machine should be based on the specific needs of the operation, including desired output, operational efficiency, and environmental considerations.
Summary Table:
Feature | Continuous Pyrolysis Plants | Batch Pyrolysis Machines |
---|---|---|
Capacity | High (24/7 operation) | Lower (batch processing) |
Operational Efficiency | High throughput, minimal downtime | Flexible, downtime for cooling |
Applications | Large-scale industrial use | Small-scale operations, R&D |
Material Construction | Durable, high-temperature resistant | Stainless steel, corrosion-resistant |
Environmental Impact | Aligns with eco-friendly policies | Smoke-free, pollution-free |
Ready to find the perfect pyrolysis machine for your operation? Contact our experts today for personalized advice!