The chemical vapor deposition (CVD) growth process is a widely used technique for depositing thin films of materials onto substrates. It involves the chemical reaction of gaseous precursors to form a solid material on a substrate surface. The process is highly versatile, allowing for the deposition of a wide range of materials, including metals, semiconductors, and ceramics. CVD is preferred in many applications due to its ability to produce high-quality, uniform films with excellent adhesion and conformal coverage, even on complex geometries. The process typically involves multiple steps, including the transport of gaseous reactants to the substrate, surface reactions, and the removal of by-products. Below, we will explore the key steps and mechanisms involved in the CVD process.
Key Points Explained:
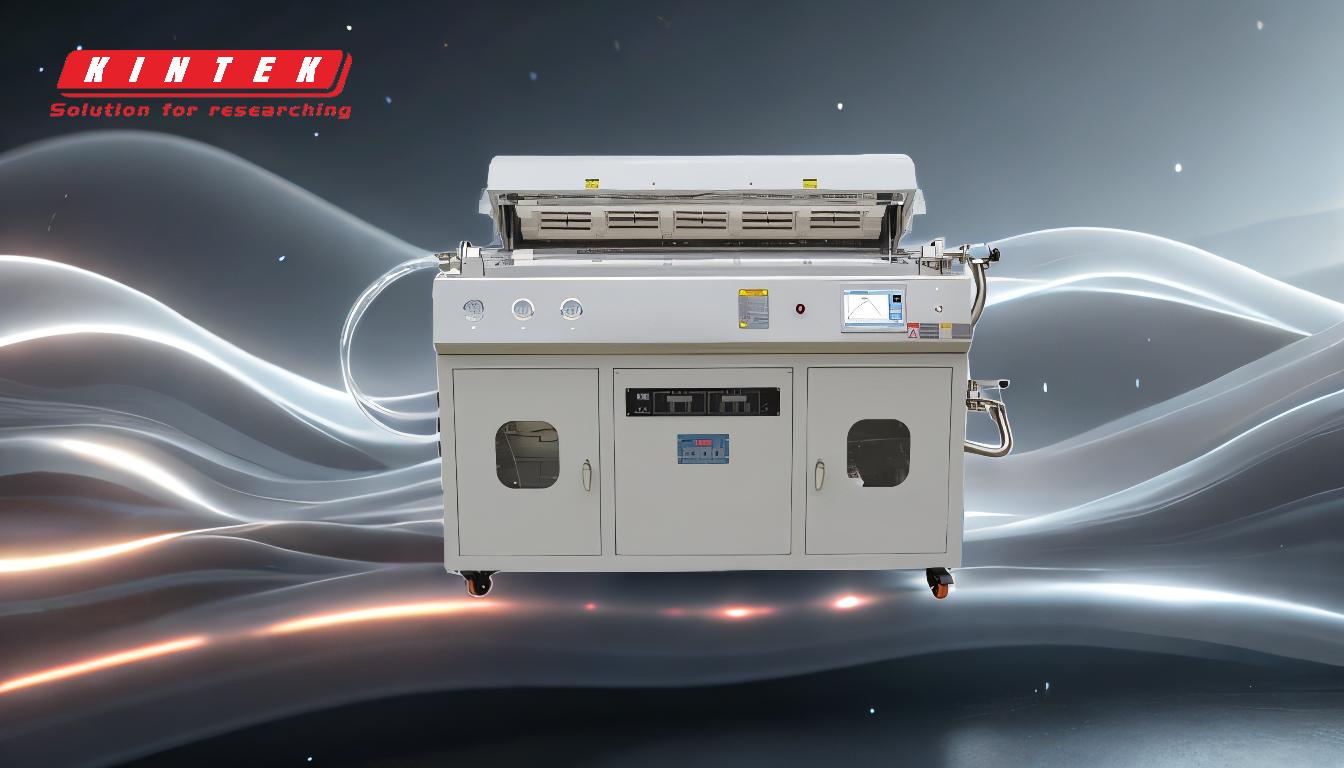
-
Transport of Reacting Gaseous Species to the Surface
- The first step in the CVD process involves the delivery of volatile gaseous precursors to the substrate surface. These precursors are typically introduced into a reaction chamber, where they are transported to the substrate by gas flow. The efficiency of this step depends on factors such as gas flow rate, pressure, and temperature, which are carefully controlled to ensure uniform deposition.
-
Adsorption of Species on the Surface
- Once the gaseous precursors reach the substrate, they adsorb onto its surface. Adsorption is the process by which gas molecules adhere to the substrate surface, forming a thin layer. This step is critical because it determines the availability of reactants for subsequent chemical reactions. The adsorption process is influenced by the surface chemistry and temperature of the substrate.
-
Heterogeneous Surface-Catalyzed Reactions
- After adsorption, the adsorbed species undergo chemical reactions on the substrate surface. These reactions are often catalyzed by the substrate itself or by a catalyst layer deposited on the substrate. The reactions typically involve decomposition, reduction, or oxidation of the precursors, leading to the formation of solid material and gaseous by-products. The nature of these reactions depends on the specific precursors and process conditions.
-
Surface Diffusion of Species to Growth Sites
- The reaction products diffuse across the substrate surface to reach growth sites, where they contribute to the formation of the thin film. Surface diffusion is crucial for achieving uniform film growth and minimizing defects. The rate of diffusion is influenced by the substrate temperature and the mobility of the adsorbed species.
-
Nucleation and Growth of the Film
- Nucleation is the initial formation of small clusters of the deposited material on the substrate. These clusters grow and coalesce to form a continuous thin film. The nucleation and growth processes are influenced by factors such as substrate temperature, precursor concentration, and surface energy. Proper control of these factors is essential for achieving high-quality films with desired properties.
-
Desorption of Gaseous Reaction Products
- As the film grows, gaseous by-products are generated from the surface reactions. These by-products must be desorbed from the substrate surface and transported away from the reaction zone to prevent contamination and ensure continuous film growth. The desorption process is facilitated by maintaining appropriate pressure and temperature conditions in the reaction chamber.
-
Transportation of Reaction Products Away from the Surface
- The final step involves the removal of gaseous by-products from the reaction chamber. This is typically achieved by continuous gas flow or vacuum pumping. Efficient removal of by-products is essential to maintain the purity of the deposited film and prevent unwanted reactions.
Advantages of CVD Over PVD
- CVD is not limited by line-of-sight deposition, allowing for uniform coverage on complex geometries.
- It offers high throwing power, making it suitable for coating substrates with intricate shapes.
- CVD processes are often more economical and provide higher deposition rates compared to physical vapor deposition (PVD).
- Unlike PVD, CVD does not typically require an ultra-high vacuum, simplifying the equipment and reducing costs.
Common CVD Methods
- Chemical Transport Method: Involves the transport of a solid material in the form of a volatile compound, which decomposes at the substrate to form the desired film.
- Pyrolysis Method: Relies on the thermal decomposition of gaseous precursors at high temperatures to deposit the material.
- Synthesis Reaction Method: Involves the reaction of two or more gaseous precursors to form a solid film on the substrate.
By understanding these key steps and mechanisms, one can appreciate the versatility and effectiveness of the CVD process in producing high-quality thin films for various applications.
Summary Table:
Step | Description |
---|---|
1. Transport of Gaseous Species | Delivery of volatile precursors to the substrate via gas flow, controlled by flow rate, pressure, and temperature. |
2. Adsorption on Surface | Gaseous precursors adhere to the substrate, forming a thin layer influenced by surface chemistry and temperature. |
3. Surface-Catalyzed Reactions | Adsorbed species undergo decomposition, reduction, or oxidation to form solid material and by-products. |
4. Surface Diffusion to Growth Sites | Reaction products diffuse across the substrate to form a uniform film, influenced by temperature and mobility. |
5. Nucleation and Film Growth | Small clusters form and grow into a continuous film, controlled by temperature, precursor concentration, and surface energy. |
6. Desorption of By-Products | Gaseous by-products are removed from the surface to prevent contamination and ensure continuous growth. |
7. Removal of By-Products | By-products are transported out of the reaction chamber via gas flow or vacuum pumping. |
Advantages of CVD Over PVD | - Uniform coverage on complex geometries - High throwing power - Economical and high deposition rates - No ultra-high vacuum required |
Common CVD Methods | - Chemical Transport Method - Pyrolysis Method - Synthesis Reaction Method |
Discover how the CVD process can elevate your thin film applications—contact us today for expert guidance!