Chemical vapor deposition (CVD) is a sophisticated manufacturing technique used to deposit thin films and coatings onto substrates through chemical reactions in a controlled environment. This process is integral to industries such as semiconductor manufacturing, optical device production, and the creation of protective coatings. The CVD process typically involves several key steps, including the transport of gaseous reactants to the substrate surface, adsorption, surface reactions, nucleation, and film growth, followed by the desorption and removal of by-products. The technique is highly versatile, enabling the efficient growth of low-dimensional materials and the enhancement of substrate properties like durability, friction reduction, and thermal performance.
Key Points Explained:
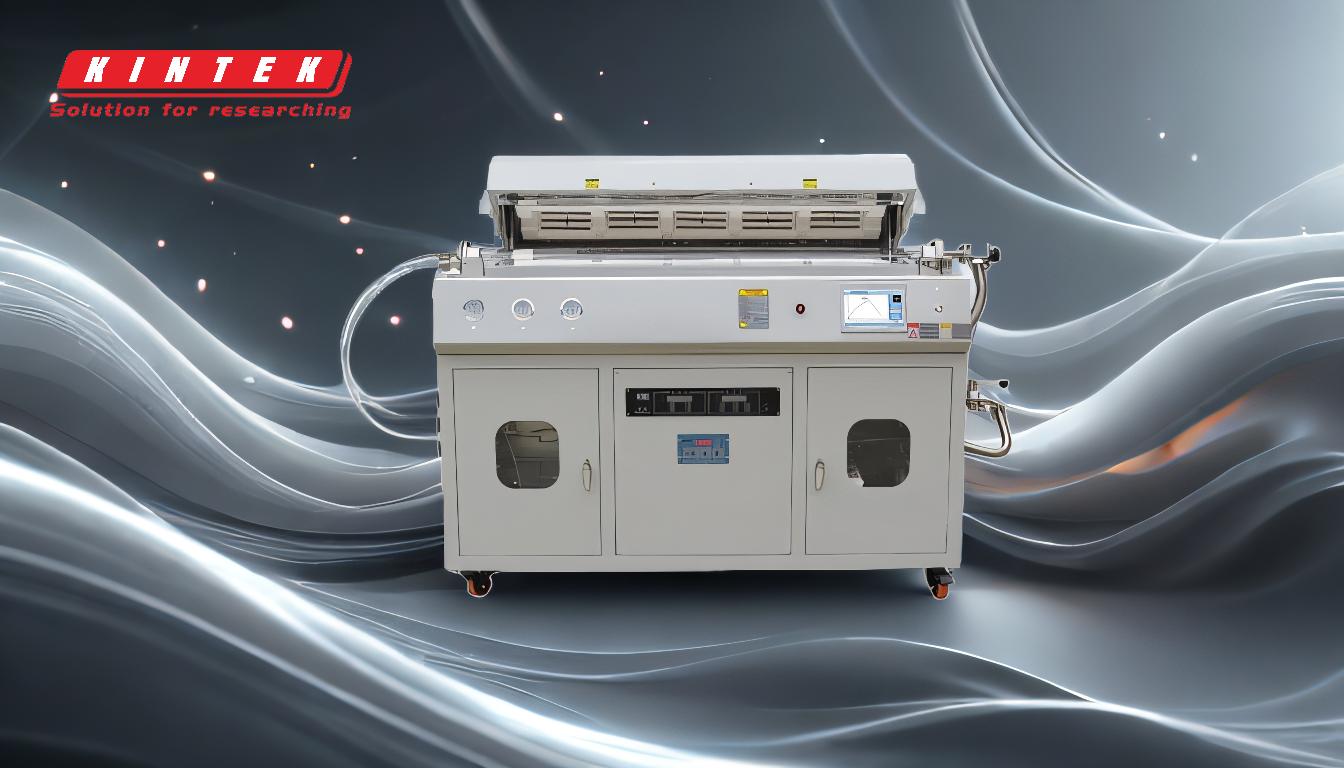
-
Transport of Reacting Gaseous Species:
- The process begins with the introduction of volatile gaseous compounds into a reaction chamber. These gases are transported to the substrate surface, often under vacuum conditions, to ensure precise control over the deposition environment.
-
Adsorption on the Surface:
- Once the gaseous species reach the substrate, they adsorb onto its surface. This step is crucial as it sets the stage for the subsequent chemical reactions that will form the thin film.
-
Heterogeneous Surface-Catalyzed Reactions:
- The adsorbed species undergo chemical reactions on the substrate surface, often catalyzed by the surface itself. These reactions can involve decomposition, recombination, or interaction with other gases, leading to the formation of solid material.
-
Surface Diffusion to Growth Sites:
- After the initial reactions, the species diffuse across the substrate surface to reach growth sites where nucleation and film growth occur. This step ensures uniform deposition and adherence of the material.
-
Nucleation and Growth of the Film:
- Nucleation marks the beginning of film formation, where small clusters of the deposited material form on the substrate. These clusters grow and coalesce to form a continuous thin film.
-
Desorption of Gaseous By-products:
- As the film grows, gaseous by-products are generated and must be desorbed from the surface. These by-products are then transported away from the reaction zone to maintain the purity and integrity of the deposited film.
-
Applications and Benefits:
- CVD is widely used in the production of semiconductors, optical devices, and protective coatings. It is particularly valued for its ability to produce high-quality, uniform films with precise control over thickness and composition. Additionally, CVD can enhance substrate properties, such as increasing durability, reducing friction, and improving thermal performance.
-
Versatility in Material Deposition:
- The technique is capable of depositing a wide range of materials, including polymers like poly(paraxylene), through vapor deposition in a vacuum chamber. This versatility makes CVD a cornerstone technology in advanced manufacturing and material science.
By understanding these key steps and their significance, one can appreciate the complexity and precision involved in the chemical vapor deposition process, as well as its critical role in modern industrial applications.
Summary Table:
Step | Description |
---|---|
Transport of Gaseous Species | Volatile gases are introduced into a reaction chamber and transported to the substrate. |
Adsorption on the Surface | Gaseous species adsorb onto the substrate surface, enabling chemical reactions. |
Surface-Catalyzed Reactions | Adsorbed species undergo reactions, often catalyzed by the substrate surface. |
Surface Diffusion | Species diffuse across the substrate to growth sites for uniform deposition. |
Nucleation and Film Growth | Small clusters form and grow into a continuous thin film. |
Desorption of By-products | Gaseous by-products are removed to maintain film purity. |
Applications | Used in semiconductors, optical devices, and protective coatings. |
Benefits | Enhances durability, reduces friction, and improves thermal performance. |
Discover how CVD can revolutionize your manufacturing process—contact our experts today!