The cleaning process before PVD (Physical Vapor Deposition) coating is a critical step to ensure the quality and durability of the coating. It involves a series of meticulous steps to remove contaminants such as oils, oxides, and organic films from the substrate. The process typically includes ultrasonic cleaning with environmentally friendly detergents, rinsing, and drying. These steps are essential to achieve proper adhesion of the coating and to prevent defects that could compromise the performance of the final product.
Key Points Explained:
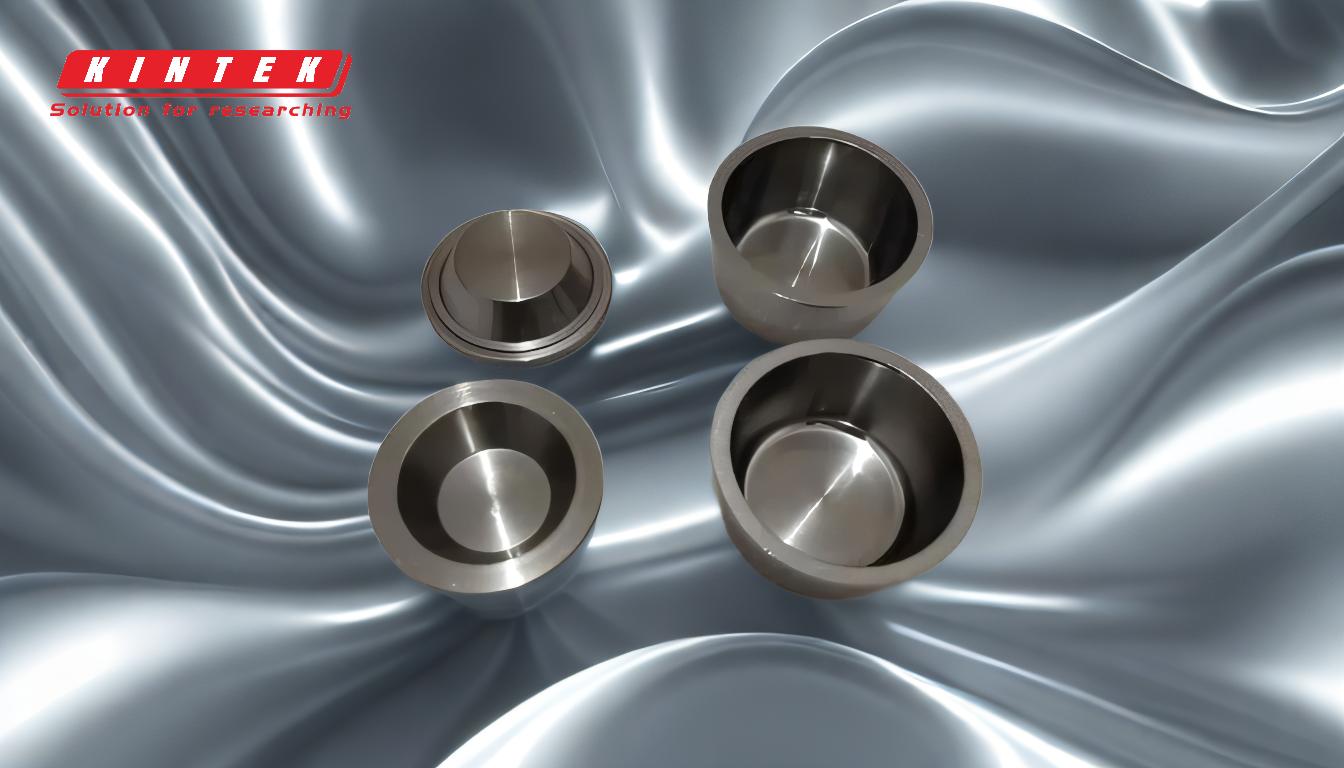
-
Importance of Cleaning Before PVD Coating:
- Contaminant Removal: Contaminants like oils, oxides, and organic films can significantly affect the adhesion and quality of the PVD coating. These contaminants can lead to poor coating adhesion, uneven deposition, and even coating failure.
- Surface Preparation: A clean surface is crucial for the PVD coating to adhere properly. The cleaning process ensures that the substrate is free from any substances that could interfere with the coating's ability to bond with the surface.
-
Steps in the Cleaning Process:
-
Ultrasonic Cleaning:
- Process: The items are placed in a tank filled with a cleaning solution, and ultrasonic waves are used to agitate the solution. This agitation helps to dislodge contaminants from the surface of the substrate.
- Detergents: Environmentally friendly detergents are often used in this step to ensure that the cleaning process is both effective and sustainable.
-
Rinsing:
- Purpose: After ultrasonic cleaning, the items are rinsed to remove any remaining detergent and loosened contaminants.
- Methods: Rinsing can be done using deionized water or other suitable rinsing agents to ensure that no residues are left on the surface.
-
Drying:
- Importance: Drying is the final step in the cleaning process. It ensures that no moisture remains on the surface, which could affect the coating process.
- Techniques: Drying can be achieved using air drying, oven drying, or other methods depending on the substrate and the specific requirements of the PVD process.
-
Ultrasonic Cleaning:
-
Additional Surface Preparation Techniques:
- Polishing and Tumbling: These techniques are used to smooth the surface and remove any rough spots or burrs that could affect the coating's uniformity.
- Acid Etching: Acid etching is sometimes used to remove oxides and other surface contaminants that are not easily removed by ultrasonic cleaning.
- Sand or Glass-Bead Blasting: This technique is used to clean and roughen the surface, which can improve the adhesion of the PVD coating.
-
Quality Control:
- Inspection: After cleaning, the items are inspected to ensure that they are free of contaminants and ready for the PVD coating process.
- Adhesion Testing: In some cases, adhesion tests may be performed to ensure that the coating will adhere properly to the substrate.
-
Environmental Considerations:
- Eco-Friendly Detergents: The use of environmentally friendly detergents in the cleaning process helps to minimize the environmental impact of the PVD coating process.
- Waste Management: Proper disposal of cleaning solutions and rinsing agents is essential to prevent environmental contamination.
In summary, the cleaning process before PVD coating is a multi-step procedure designed to ensure that the substrate is free of contaminants and ready for coating. This process is crucial for achieving a high-quality, durable coating that adheres well to the substrate. The steps include ultrasonic cleaning, rinsing, drying, and sometimes additional surface preparation techniques. Quality control and environmental considerations are also important aspects of the cleaning process.
Summary Table:
Step | Purpose | Details |
---|---|---|
Ultrasonic Cleaning | Removes oils, oxides, and organic films | Uses environmentally friendly detergents and ultrasonic waves for effective contamination removal. |
Rinsing | Eliminates residual detergents and loosened contaminants | Done with deionized water or suitable rinsing agents to ensure a residue-free surface. |
Drying | Prevents moisture from affecting the coating process | Achieved via air drying, oven drying, or other methods depending on substrate requirements. |
Additional Prep | Enhances surface readiness for coating | Includes polishing, acid etching, or sand/glass-bead blasting for improved adhesion. |
Quality Control | Ensures the substrate is contamination-free and ready for PVD coating | Involves inspection and adhesion testing to verify surface readiness. |
Environmental Care | Minimizes environmental impact | Uses eco-friendly detergents and proper waste management practices. |
Ready to optimize your PVD coating process? Contact our experts today for tailored solutions!