Plastic pyrolysis is a thermochemical process that converts plastic waste into valuable fuels like pyrolysis oil, carbon black, and syngas. This process involves heating plastic in the absence of oxygen at high temperatures (200-900°C), breaking down the polymer chains into smaller hydrocarbon molecules. The process is eco-friendly as it reduces plastic waste and produces usable fuel. However, challenges such as harmful emissions, health risks, and economic impacts on other waste-to-fuel processes need to be addressed. Recent advancements, like using ruthenium-based catalysts, have made the process more efficient and economical, paving the way for large-scale adoption.
Key Points Explained:
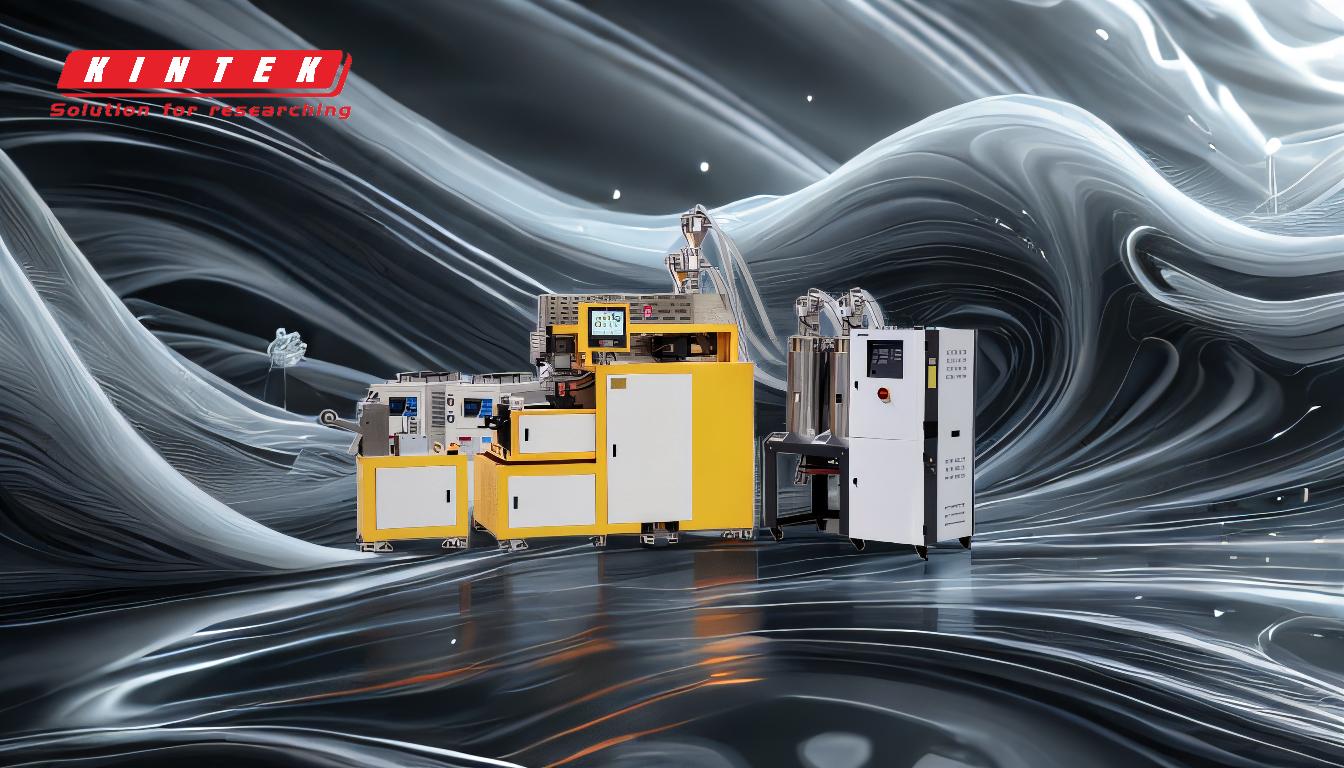
-
What is Plastic Pyrolysis?
- Plastic pyrolysis is a thermochemical decomposition process that converts plastic waste into fuel by heating it in an oxygen-free environment.
- The process breaks down long-chain polymers in plastics into smaller hydrocarbon molecules, producing fuel oil, carbon black, and syngas.
- It is an eco-friendly solution for managing plastic waste and reducing reliance on fossil fuels.
-
How Does the Pyrolysis Process Work?
-
Step 1: Pre-treatment
- Plastic waste is collected, shredded, and dried to remove moisture and impurities.
- Non-plastic materials are separated to ensure the feedstock is pure.
-
Step 2: Heating
- The shredded plastic is loaded into a pyrolysis chamber and heated to temperatures between 200-900°C.
- The absence of oxygen prevents combustion, allowing the plastic to melt and vaporize.
-
Step 3: Condensation
- The vaporized hydrocarbons are condensed into liquid pyrolysis oil.
-
Step 4: Refinement
- The pyrolysis oil is distilled and purified to improve its quality for use as fuel.
-
Step 5: Storage and Dispatch
- The final products (fuel oil, carbon black, and syngas) are stored and dispatched for various applications.
-
Step 1: Pre-treatment
-
Benefits of Plastic Pyrolysis
- Waste Reduction: Converts non-recyclable plastic waste into valuable resources.
- Fuel Production: Produces pyrolysis oil, which can be used as a substitute for diesel or gasoline.
- Energy Recovery: Generates syngas, which can be used for heating or electricity generation.
- Carbon Black: A byproduct used in industries like tire manufacturing and ink production.
- Eco-Friendly: Reduces landfill waste and greenhouse gas emissions compared to traditional incineration.
-
Challenges and Concerns
- Emissions: The process can release harmful pollutants like nitrous oxides and sulfur dioxides if not properly controlled.
- Health Risks: Workers may be exposed to toxic fumes during the process.
- Economic Impact: Competing waste-to-fuel processes, such as solid waste-to-fuel, may face economic challenges.
- Dependence on Imports: Some countries rely on importing waste for pyrolysis, which can create logistical and environmental issues.
-
Recent Advancements in Pyrolysis Technology
-
Catalyst Development: Researchers have introduced ruthenium-based catalysts that improve the efficiency of plastic-to-fuel conversion.
- These catalysts enable the process to work at lower temperatures, reducing energy consumption.
- They also increase the yield of fuel oil to up to 90% of the plastic waste.
- Scalability: The new methods are faster and more economical, making them suitable for large-scale implementation.
-
Catalyst Development: Researchers have introduced ruthenium-based catalysts that improve the efficiency of plastic-to-fuel conversion.
-
Applications of Pyrolysis Products
- Pyrolysis Oil: Can be used as a fuel in industrial boilers, generators, and vehicles after refinement.
- Carbon Black: Used as a reinforcing agent in rubber products, pigments, and coatings.
- Syngas: A mixture of hydrogen and carbon monoxide, used for heating or as a feedstock for chemical production.
-
Future Prospects
- With advancements in catalyst technology and process optimization, plastic pyrolysis has the potential to become a mainstream waste management solution.
- Governments and industries are increasingly investing in pyrolysis plants to address plastic pollution and meet sustainability goals.
- Continued research is needed to mitigate emissions, improve safety, and enhance the economic viability of the process.
In conclusion, plastic pyrolysis offers a promising solution for converting plastic waste into fuel, addressing both environmental and energy challenges. While there are hurdles to overcome, technological advancements and growing awareness are driving its adoption worldwide.
Summary Table:
Aspect | Details |
---|---|
Process | Thermochemical decomposition of plastic waste in an oxygen-free environment. |
Temperature Range | 200-900°C |
Products | Pyrolysis oil, carbon black, and syngas. |
Benefits | Waste reduction, fuel production, energy recovery, eco-friendly. |
Challenges | Harmful emissions, health risks, economic impacts. |
Advancements | Ruthenium-based catalysts improve efficiency and scalability. |
Applications | Fuel for boilers, carbon black for rubber, syngas for heating. |
Discover how plastic pyrolysis can transform waste into valuable resources—contact our experts today to learn more!