Chemical Vapor Deposition (CVD) is a widely used technique for depositing thin films and coatings onto substrates through chemical reactions in the vapor phase. This method involves the use of precursor gases that react on the surface of a substrate, typically at elevated temperatures, to form a solid material. The CVD process is highly versatile and can be tailored to produce a variety of materials, including metals, semiconductors, and ceramics, with precise control over film thickness, composition, and morphology. The process can be conducted at atmospheric pressure or under vacuum, depending on the specific requirements of the application. Key parameters such as temperature, pressure, and precursor flow rates significantly influence the quality and properties of the deposited films. CVD is widely used in industries such as electronics, optics, and materials science due to its ability to produce high-quality, uniform coatings.
Key Points Explained:
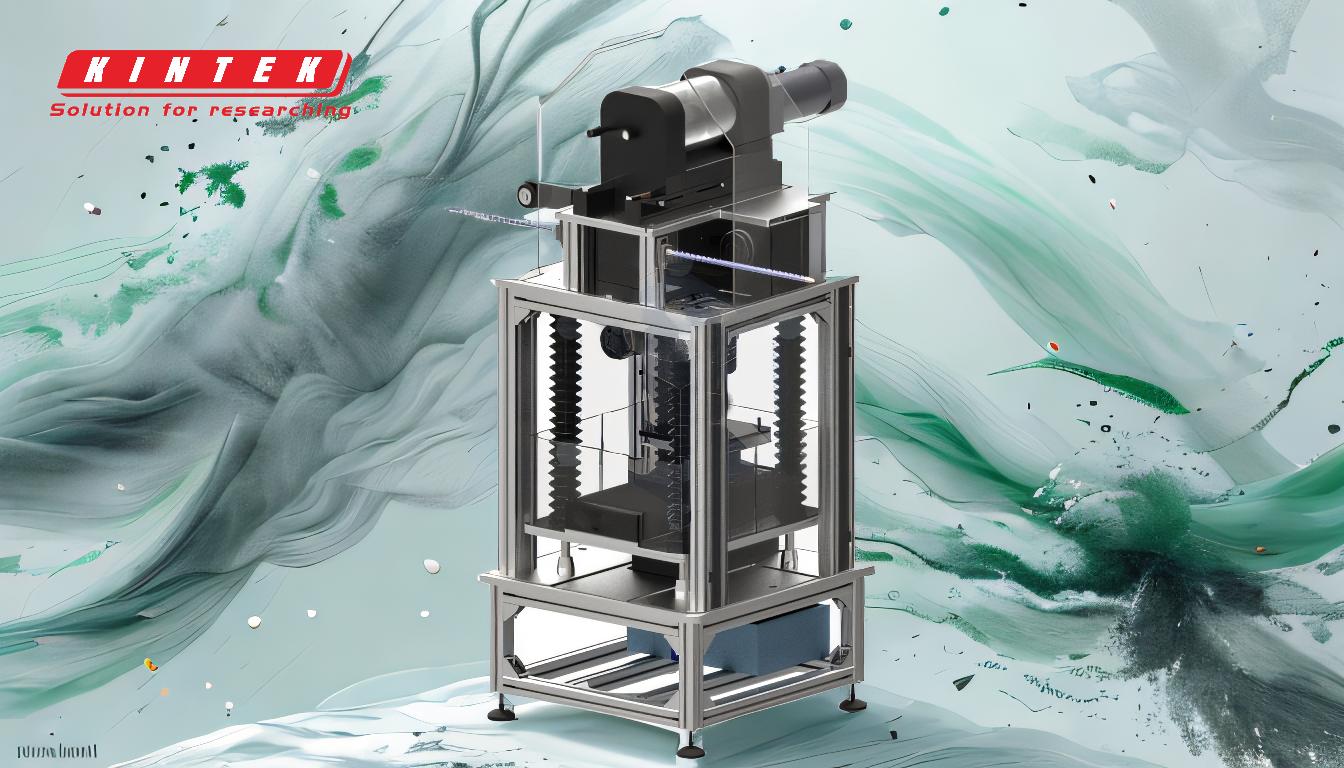
-
Basic Principle of CVD:
- CVD involves the use of precursor gases that react on the surface of a substrate to form a solid material. The chemical reaction occurs in the vapor phase, and the resulting solid is deposited as a thin film, powder, or single crystal material.
-
Process Parameters:
- Temperature: The substrate temperature is a critical parameter in CVD. It influences the rate of chemical reactions and the quality of the deposited film. Higher temperatures generally lead to faster deposition rates but may also affect the film's properties.
- Pressure: CVD can be performed at both atmospheric and low pressures. Low-pressure CVD (LPCVD) is often used to achieve more uniform films and better control over film properties.
- Precursor Flow Rates: The flow rates of the precursor gases determine the availability of reactants on the substrate surface. Proper control of flow rates is essential for achieving the desired film composition and thickness.
-
Types of CVD:
- Atmospheric Pressure CVD (APCVD): Conducted at atmospheric pressure, this method is simpler and often used for large-scale production. However, it may result in less uniform films compared to low-pressure methods.
- Low-Pressure CVD (LPCVD): Performed under reduced pressure, LPCVD offers better control over film uniformity and properties. It is commonly used in the semiconductor industry.
- Plasma-Enhanced CVD (PECVD): Utilizes plasma to enhance the chemical reactions, allowing for lower deposition temperatures. This is particularly useful for depositing films on temperature-sensitive substrates.
-
Applications of CVD:
- Semiconductor Manufacturing: CVD is extensively used in the production of semiconductor devices, including the deposition of silicon dioxide, silicon nitride, and various metal films.
- Optical Coatings: CVD is employed to deposit anti-reflective, protective, and other functional coatings on optical components.
- Protective Coatings: CVD is used to apply wear-resistant and corrosion-resistant coatings on tools and components in various industries.
-
Comparison with Short Path Vacuum Distillation:
- While CVD involves chemical reactions in the vapor phase to deposit materials, short path vacuum distillation is a physical separation process used to purify or separate compounds based on their boiling points under reduced pressure. Both processes utilize vacuum conditions, but their objectives and mechanisms are fundamentally different.
-
Advantages of CVD:
- High-quality, uniform films with precise control over thickness and composition.
- Versatility in depositing a wide range of materials, including metals, semiconductors, and ceramics.
- Ability to coat complex geometries and large areas.
-
Challenges in CVD:
- High equipment and operational costs.
- Need for precise control over process parameters to achieve desired film properties.
- Potential for hazardous by-products, requiring proper handling and disposal.
In summary, CVD is a powerful and versatile technique for depositing thin films and coatings with high precision and control. Its applications span across various industries, making it a critical process in modern manufacturing and materials science.
Summary Table:
Aspect | Details |
---|---|
Basic Principle | Precursor gases react on a substrate to form solid thin films or coatings. |
Key Parameters | Temperature, pressure, and precursor flow rates. |
Types of CVD | APCVD, LPCVD, PECVD. |
Applications | Semiconductor manufacturing, optical coatings, protective coatings. |
Advantages | High-quality films, versatility, ability to coat complex geometries. |
Challenges | High costs, precise parameter control, hazardous by-products. |
Discover how CVD can enhance your manufacturing process—contact our experts today!