The Chemical Vapor Deposition (CVD) process for carbon nanotubes (CNTs) is a widely used commercial method that involves the decomposition of carbon-containing gases on a substrate, typically in the presence of a catalyst. This process allows for the controlled growth of CNTs with specific structural properties. CVD is preferred over traditional methods like laser ablation and arc discharge due to its scalability, cost-effectiveness, and ability to produce high-quality CNTs. The process involves precise control of temperature, gas flow, and catalyst properties, ensuring efficient synthesis with minimal environmental impact. Emerging advancements focus on using sustainable feedstocks, such as carbon dioxide or methane, to further reduce the ecological footprint of CNT production.
Key Points Explained:
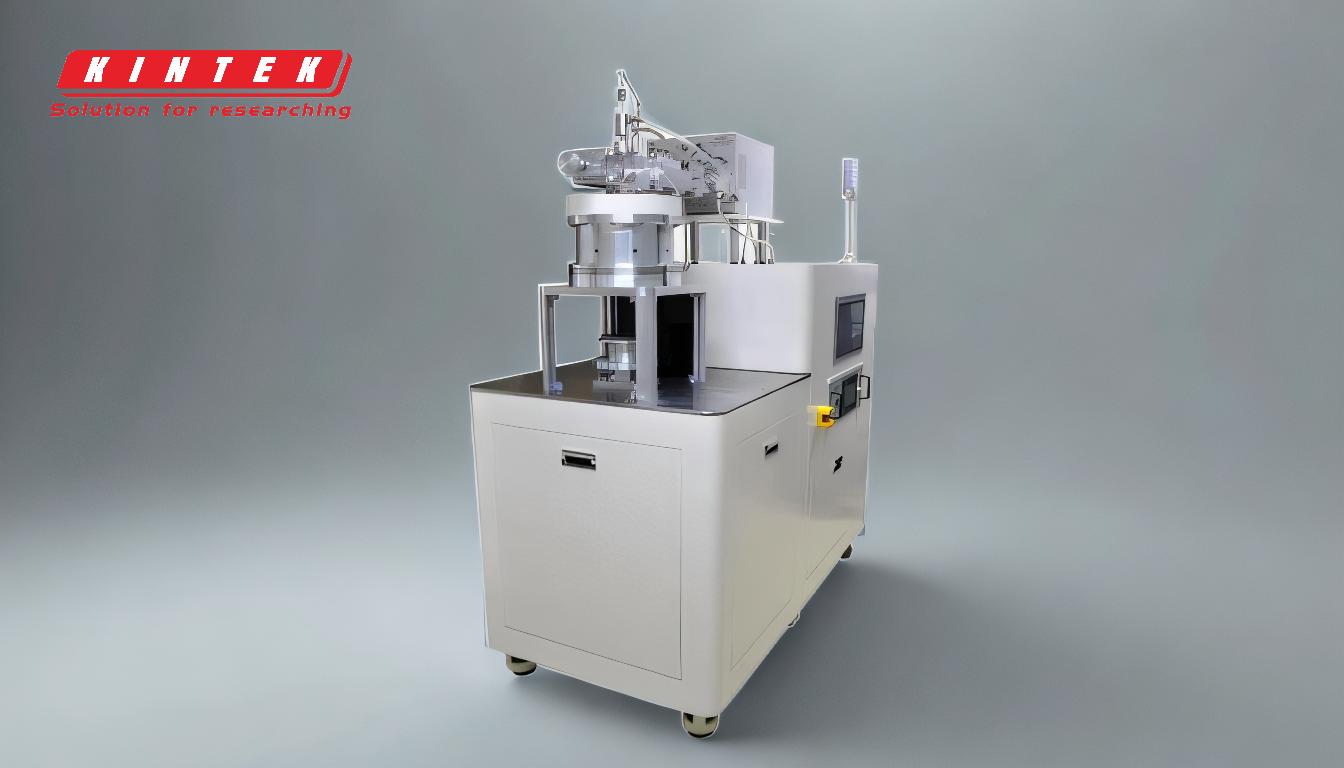
-
Overview of CVD for CNTs:
- CVD is a bottom-up synthesis method where carbon-containing gases, such as methane or ethylene, decompose on a substrate to form CNTs.
- It is the dominant commercial process for CNT production due to its scalability, structural controllability, and cost-effectiveness.
-
Key Components of the CVD Process:
- Carbon Source: Gases like methane, ethylene, or acetylene serve as the carbon feedstock.
- Catalyst: Metal nanoparticles (e.g., iron, nickel, or cobalt) are used to facilitate the decomposition of the carbon source and guide CNT growth.
- Substrate: Materials like silicon wafers or metal foils provide a surface for CNT growth.
- Temperature and Gas Flow: Precise control of these parameters ensures optimal growth conditions and high-quality CNTs.
-
Types of CVD:
- Thermal CVD: Relies on high temperatures (typically 600–1000°C) to decompose the carbon source and grow CNTs.
- Plasma-Enhanced CVD (PECVD): Uses plasma to lower the required reaction temperature, enabling CNT growth on temperature-sensitive substrates.
-
Catalytic Chemical Vapor Deposition (CCVD):
- CCVD is the mainstream method for CNT synthesis due to its ability to control CNT structure (e.g., single-walled, multi-walled) and alignment.
- The process involves gas-phase rearrangement and catalyst deposition, ensuring efficient and reproducible growth.
-
Environmental Considerations:
- The synthesis process is a major contributor to the life cycle ecotoxicity of CNTs.
- Efforts to reduce material and energy consumption, as well as greenhouse gas emissions, are critical for sustainable CNT production.
- Emerging methods focus on using green or waste feedstocks, such as carbon dioxide captured by electrolysis or methane pyrolysis.
-
Advantages of CVD:
- High-quality CNTs with controlled properties.
- Scalable and cost-effective for large-scale production.
- Compatible with a variety of substrates and catalysts.
-
Emerging Trends:
- Use of sustainable feedstocks to reduce environmental impact.
- Development of advanced catalysts and process optimization to enhance CNT yield and quality.
- Integration of CVD with other technologies for novel applications, such as energy storage and composite materials.
By understanding these key aspects, purchasers and researchers can make informed decisions about the equipment, materials, and processes needed for efficient and sustainable CNT production.
Summary Table:
Aspect | Details |
---|---|
Process Overview | Decomposition of carbon-containing gases on a substrate with a catalyst. |
Key Components | Carbon source (e.g., methane), catalyst (e.g., iron), substrate, and precise temperature/gas flow control. |
Types of CVD | Thermal CVD (600–1000°C) and Plasma-Enhanced CVD (PECVD). |
Advantages | High-quality CNTs, scalability, cost-effectiveness, and compatibility. |
Environmental Focus | Use of sustainable feedstocks like carbon dioxide or methane. |
Emerging Trends | Advanced catalysts, process optimization, and integration with new technologies. |
Discover how CVD can revolutionize your CNT production—contact our experts today!