The deposition rate of PECVD (Plasma-Enhanced Chemical Vapor Deposition) is influenced by several factors, including the power of the radio frequency supply, the type and flow rate of reactive gases, the substrate temperature, and the design of the deposition system. PECVD is widely used in industries such as semiconductors, aerospace, and optics due to its ability to deposit thin films at relatively low temperatures compared to other CVD methods. The deposition rate can vary significantly depending on the specific application and parameters used, but it generally ranges from a few nanometers per minute to several micrometers per hour.
Key Points Explained:
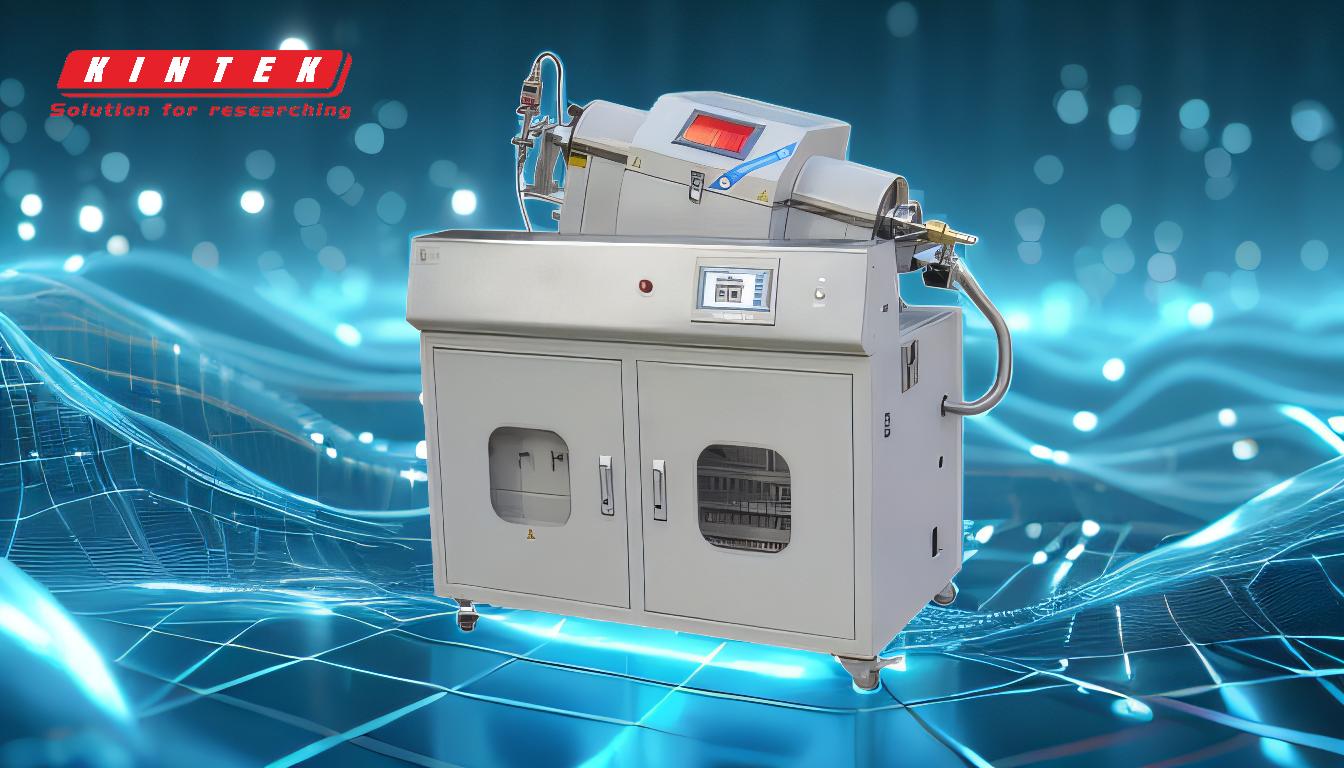
-
Components of PECVD System:
- Radio Frequency Power Supply: This component ionizes the reactive gases, creating a plasma that facilitates the deposition process. The power level of the RF supply can directly affect the deposition rate, with higher power typically leading to faster deposition.
- Water Cooling System: Essential for maintaining the temperature of various components, especially the pumps, to ensure they operate efficiently and do not overheat, which could otherwise disrupt the deposition process.
- Substrate Heating Device: Heats the substrate to the required temperature, which is crucial for the quality and adhesion of the deposited film. Proper heating also helps in removing impurities from the substrate surface.
-
Factors Affecting Deposition Rate:
- Power of RF Supply: Higher power levels can increase the ionization of gases, leading to a higher deposition rate. However, excessive power can also lead to film defects.
- Type and Flow Rate of Reactive Gases: Different gases and their flow rates can significantly impact the deposition rate. Optimal gas mixtures and flow rates are crucial for achieving desired film properties and deposition rates.
- Substrate Temperature: The temperature of the substrate affects the kinetics of the deposition process. Higher temperatures can enhance the deposition rate but may also affect film quality.
- System Design: The overall design of the PECVD system, including the arrangement of components and the efficiency of the plasma generation, can influence the deposition rate.
-
Applications of PECVD:
- Semiconductor Industry: Used for growing electronic materials with precise control over film thickness and properties.
- Aerospace Industry: Forms thermal and chemical barrier coatings to protect components from corrosive environments.
- Optics: Imparts desired reflective and transmissive properties to substrates, enhancing their optical performance.
- Other Industries: Modifies surfaces to achieve various desired properties, such as improved hardness, wear resistance, or chemical stability.
-
Typical Deposition Rates:
- The deposition rate in PECVD can vary widely depending on the specific application and parameters used. Generally, it ranges from a few nanometers per minute to several micrometers per hour. For example, in semiconductor applications, typical deposition rates might be in the range of 10-100 nm/min, while in other applications, rates could be higher or lower depending on the requirements.
-
Advantages of PECVD:
- Low Temperature Deposition: PECVD allows for the deposition of thin films at relatively low temperatures compared to other CVD methods, making it suitable for temperature-sensitive substrates.
- Versatility: Capable of depositing a wide range of materials, including silicon dioxide, silicon nitride, and various metal oxides.
- High-Quality Films: Produces films with good uniformity, adhesion, and conformality, essential for many high-performance applications.
In summary, the deposition rate of PECVD is influenced by multiple factors, including the power of the RF supply, the type and flow rate of reactive gases, the substrate temperature, and the system design. Understanding these factors is crucial for optimizing the deposition process to achieve the desired film properties and deposition rates for various industrial applications.
Summary Table:
Factor | Impact on Deposition Rate |
---|---|
RF Power Supply | Higher power increases ionization, leading to faster deposition. Excessive power may cause defects. |
Reactive Gases | Type and flow rate significantly affect deposition rate. Optimal mixtures ensure desired results. |
Substrate Temperature | Higher temperatures enhance deposition rate but may impact film quality. |
System Design | Efficient plasma generation and component arrangement influence deposition rate. |
Typical Deposition Rates | Ranges from a few nm/min to several µm/h, depending on application and parameters. |
Optimize your PECVD process for superior results—contact our experts today!