Thermal evaporation is a widely used physical vapor deposition (PVD) technique where a material is heated to its vaporization point in a vacuum, allowing it to deposit onto a substrate. The deposition rate in thermal evaporation is influenced by the temperature and power supplied to the resistance source, which directly affects the vapor pressure of the material. Higher temperatures lead to higher vapor pressures, resulting in increased deposition rates. Typical deposition rates for thermal evaporation range from 1 to 100 angstroms per second (Å/s), depending on the material and process conditions. Additionally, the choice of material and its reaction characteristics also play a role in determining the deposition rate. For example, e-beam evaporation, a variant of thermal evaporation, can achieve deposition rates ranging from 0.1 to 100 nanometers (nm) per minute at low substrate temperatures.
Key Points Explained:
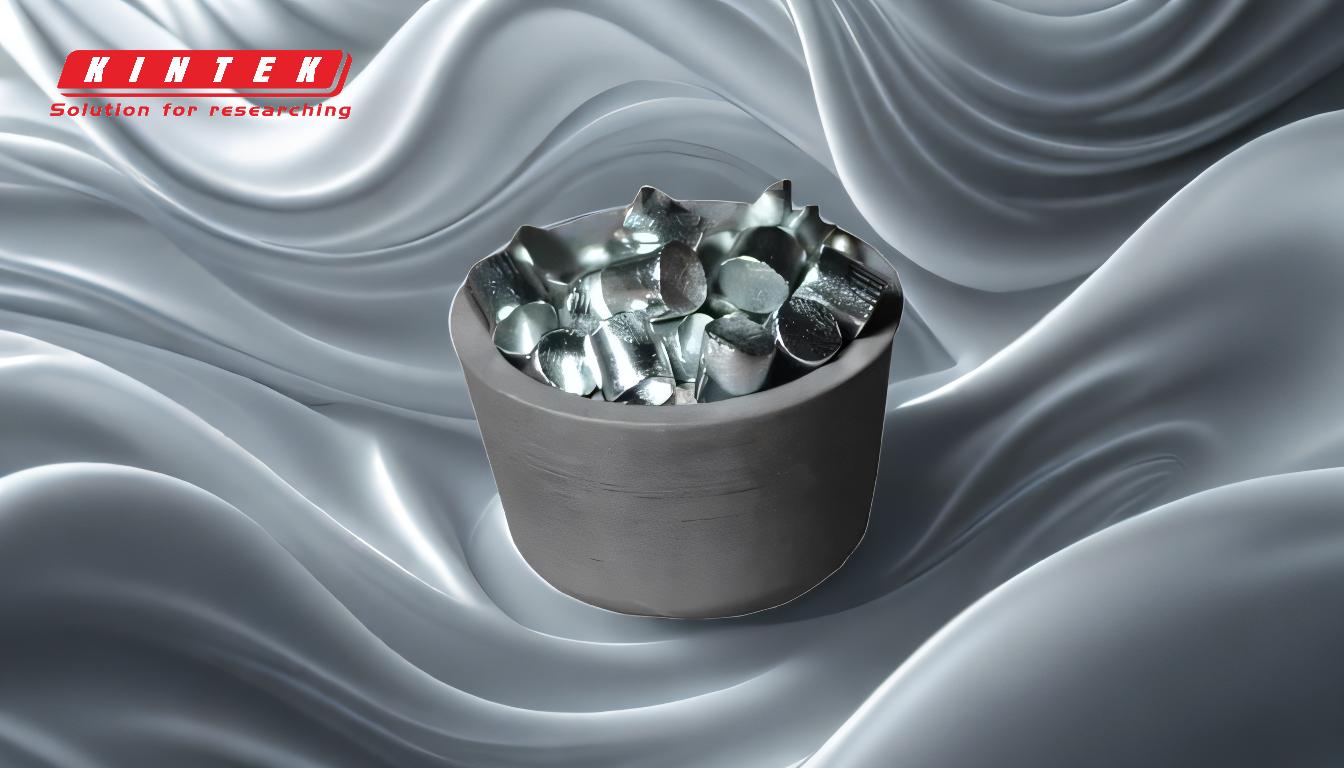
-
Deposition Rate Definition:
- The deposition rate refers to the amount of material deposited onto a substrate per unit of time. In thermal evaporation, this rate is typically measured in angstroms per second (Å/s) or nanometers per minute (nm/min).
-
Influence of Temperature and Power:
- The deposition rate in thermal evaporation is directly influenced by the temperature of the material being evaporated. Higher temperatures increase the vapor pressure of the material, leading to more material being vaporized and deposited onto the substrate.
- The power supplied to the resistance source (e.g., a filament or boat) determines the temperature. Higher power results in higher temperatures, which in turn increases the deposition rate.
-
Typical Deposition Rates:
- For thermal evaporation, typical deposition rates range from 1 to 100 angstroms per second (Å/s). This range can vary depending on the material being evaporated and the specific process conditions.
- In the case of e-beam evaporation, a related technique, deposition rates can range from 0.1 to 100 nanometers per minute (nm/min), especially at low substrate temperatures.
-
Material Characteristics:
- The choice of material significantly impacts the deposition rate. Materials with higher vapor pressures at lower temperatures will generally have higher deposition rates.
- The reaction characteristics of the material, such as its melting point and vapor pressure, are critical factors in determining the deposition rate. Materials that require higher temperatures to vaporize will typically have lower deposition rates compared to those that vaporize at lower temperatures.
-
Comparison with Other PVD Techniques:
- Thermal evaporation is one of several PVD techniques. For example, in sputtering, the deposition rate depends on factors such as the physical properties of the target material, the current, and the beam energy. Thermal evaporation, by contrast, relies primarily on temperature and vapor pressure.
- E-beam evaporation, a variant of thermal evaporation, can achieve higher deposition rates at lower substrate temperatures due to the focused energy of the electron beam.
-
Practical Considerations for Equipment and Consumables:
- When selecting equipment for thermal evaporation, it is important to consider the power capacity of the resistance source, as this will directly impact the achievable deposition rates.
- Consumables, such as the evaporation boats or filaments, must be compatible with the material being evaporated and capable of withstanding high temperatures without degrading.
- The vacuum environment is also crucial, as it ensures that the material vaporizes and deposits uniformly onto the substrate without contamination.
-
Optimization of Deposition Rate:
- To optimize the deposition rate, it is essential to balance the temperature and power settings with the material properties. Overheating can lead to excessive vaporization and potential damage to the substrate, while insufficient heating may result in low deposition rates.
- Monitoring and controlling the deposition rate in real-time can help achieve consistent and high-quality thin films.
In summary, the deposition rate in thermal evaporation is primarily determined by the temperature and power supplied to the resistance source, which affects the vapor pressure of the material. Typical rates range from 1 to 100 Å/s, with variations depending on the material and process conditions. Understanding these factors is crucial for optimizing the deposition process and achieving desired thin-film properties.
Summary Table:
Factor | Influence on Deposition Rate |
---|---|
Temperature | Higher temperatures increase vapor pressure, leading to higher deposition rates. |
Power Supply | Higher power raises temperature, directly boosting deposition rates. |
Material Properties | Materials with higher vapor pressures at lower temperatures deposit faster. |
Typical Deposition Rates | Thermal evaporation: 1–100 Å/s; E-beam evaporation: 0.1–100 nm/min. |
Equipment Considerations | Power capacity, consumable compatibility, and vacuum environment are critical for optimal rates. |
Optimize your thermal evaporation process—contact our experts today for tailored solutions!