Wet and dry ball mills are both used for grinding materials into fine particles, but they differ significantly in their processes, efficiency, and applications. Dry ball milling is ideal for materials that do not require extremely fine particles or those that do not clump together, as it avoids the complications of handling liquids. On the other hand, wet ball milling is more effective for materials that need very fine particles or have a tendency to agglomerate, as the liquid medium aids in breaking down the material and preventing clumping. The choice between the two depends on the material properties, desired particle size, and specific application requirements.
Key Points Explained:
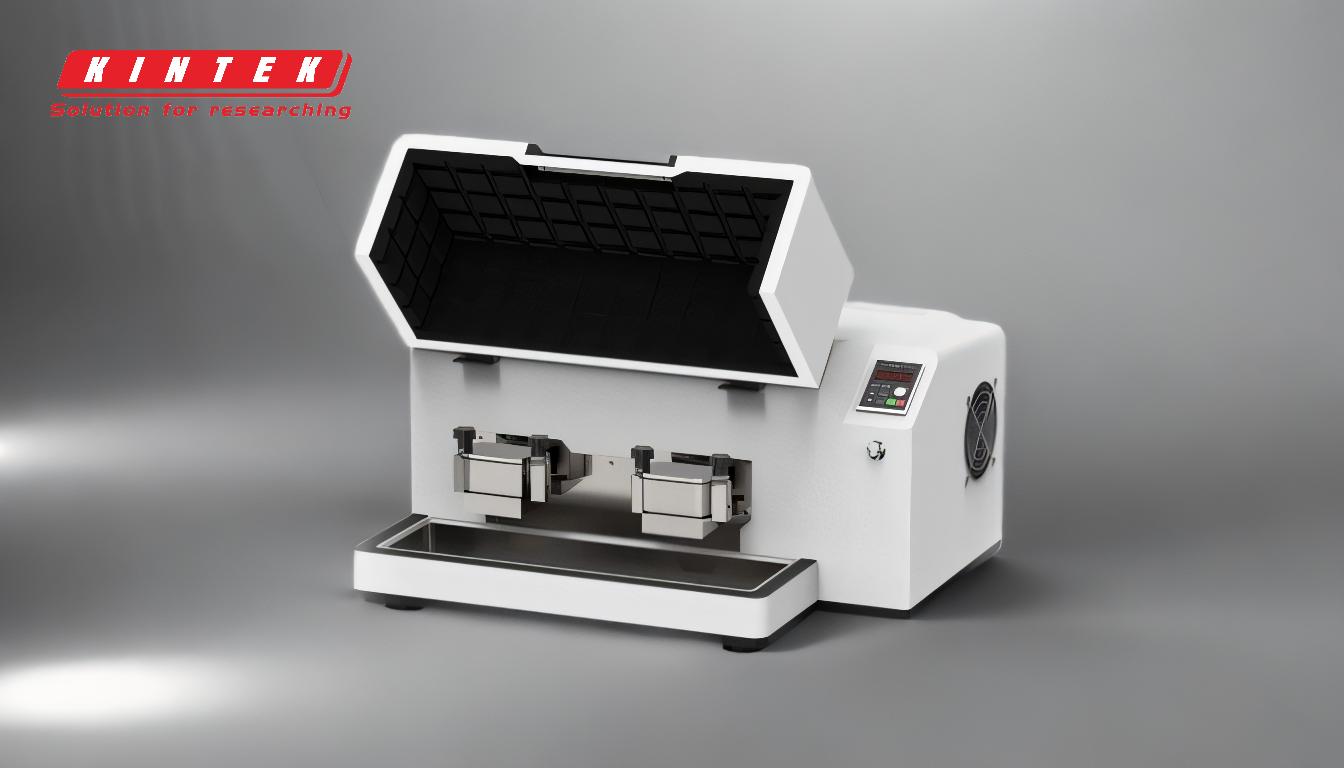
-
Process Differences:
- Dry Ball Mill: Operates without any liquid medium. The material is ground by the impact and friction between the balls and the material itself.
- Wet Ball Mill: Uses a liquid (usually water) as a medium to assist in the grinding process. The liquid helps in breaking down the material and prevents the particles from sticking together.
-
Efficiency:
- Dry Ball Mill: More efficient for materials that do not require extremely fine particles or have a low tendency to clump. It is simpler to handle and requires less maintenance since there is no liquid to manage.
- Wet Ball Mill: More efficient for materials that need very fine particles or have a high tendency to agglomerate. The liquid medium helps in achieving a finer grind and reduces the risk of material clumping.
-
Material Suitability:
- Dry Ball Mill: Suitable for materials that are not affected by the absence of a liquid medium and do not require ultra-fine grinding. Examples include certain types of ores, ceramics, and some chemicals.
- Wet Ball Mill: Suitable for materials that benefit from the presence of a liquid medium, such as those that are prone to clumping or require a very fine particle size. Examples include certain minerals, pigments, and some pharmaceuticals.
-
Operational Considerations:
- Dry Ball Mill: Easier to operate and maintain since there is no need to handle liquids. However, it may generate more dust, which can be a concern in some environments.
- Wet Ball Mill: Requires handling of liquids, which can complicate the operation and maintenance. However, it generally produces less dust and can be more effective for certain materials.
-
Applications:
- Dry Ball Mill: Commonly used in industries where the material does not require ultra-fine grinding or where the presence of a liquid medium is undesirable. Examples include the cement industry and certain types of chemical processing.
- Wet Ball Mill: Often used in industries where extremely fine particles are required or where the material has a high tendency to clump. Examples include the mining industry for ore processing and the paint industry for pigment dispersion.
-
Environmental and Safety Considerations:
- Dry Ball Mill: May pose a higher risk of dust generation, which can be a safety and environmental concern. Proper dust control measures are necessary.
- Wet Ball Mill: Generally produces less dust, but the handling of liquids can introduce other environmental and safety concerns, such as spillage and the need for proper liquid waste management.
In summary, the choice between wet and dry ball milling depends on the specific requirements of the material being processed, the desired particle size, and the operational constraints of the application. Each method has its advantages and limitations, and the decision should be based on a thorough evaluation of these factors.
Summary Table:
Aspect | Dry Ball Mill | Wet Ball Mill |
---|---|---|
Process | No liquid medium; grinding via impact and friction. | Uses liquid (e.g., water) to assist grinding and prevent clumping. |
Efficiency | Better for materials not requiring ultra-fine particles or prone to clumping. | More effective for fine particles and materials prone to agglomeration. |
Material Suitability | Ideal for ores, ceramics, and chemicals not needing ultra-fine grinding. | Suitable for minerals, pigments, and pharmaceuticals requiring fine grinding. |
Operational Ease | Easier to maintain; no liquid handling. May generate dust. | Requires liquid handling; less dust but more complex maintenance. |
Applications | Cement industry, chemical processing. | Mining (ore processing), paint (pigment dispersion). |
Environmental Impact | Dust generation requires control measures. | Liquid waste management needed; less dust. |
Need help choosing between wet and dry ball mills? Contact our experts today for tailored advice!