Induction furnaces and arc furnaces are both widely used in metallurgical processes, but they differ significantly in their heating mechanisms, efficiency, and applications. Induction furnaces generate heat directly within the molten metal using electromagnetic induction, resulting in faster heating and higher thermal efficiency. In contrast, arc furnaces rely on an electric arc to transfer heat indirectly through slag, which leads to slower heating and lower efficiency due to heat loss through the furnace structure. Below, we explore the key differences between these two types of furnaces in detail.
Key Points Explained:
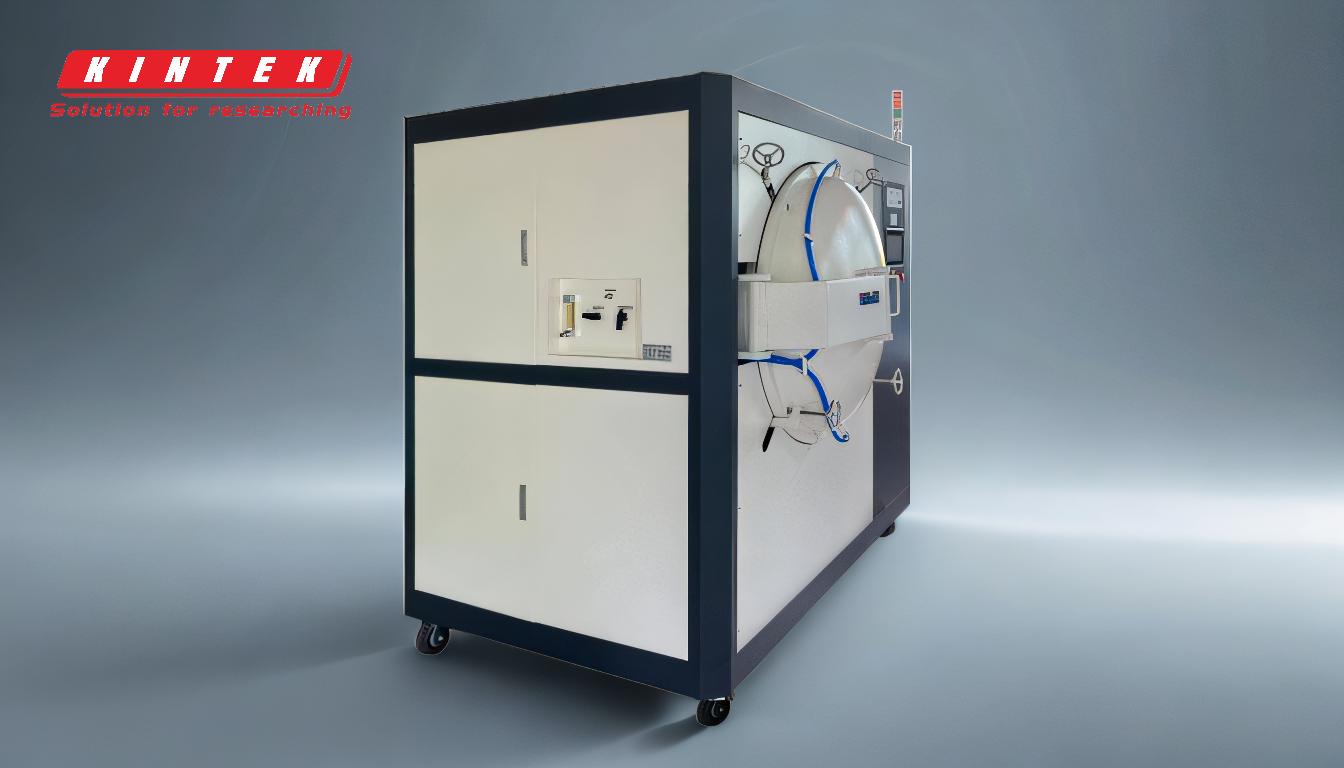
-
Heating Mechanism:
- Induction Furnace: Heat is generated directly within the molten metal using electromagnetic induction. This method ensures efficient and uniform heating, as the energy is transferred directly to the metal without intermediate steps.
- Arc Furnace: Heat is generated by an electric arc between electrodes and the metal. The heat is then transferred to the molten metal through slag, which acts as an intermediary. This indirect heating process is less efficient.
-
Thermal Efficiency:
- Induction Furnace: Offers higher thermal efficiency because the heat is produced directly in the metal, minimizing energy losses. This makes it ideal for processes requiring precise temperature control and rapid heating.
- Arc Furnace: Suffers from lower thermal efficiency due to heat loss through the furnace cover, walls, and the indirect transfer of heat via slag. This makes it less energy-efficient compared to induction furnaces.
-
Heat Loss:
- Induction Furnace: Minimal heat loss occurs because the heat is generated within the metal itself, and the furnace design typically includes insulation to retain heat.
- Arc Furnace: Experiences significant heat loss through the furnace structure, including the cover and walls. This further reduces its overall efficiency.
-
Applications:
- Induction Furnace: Commonly used in applications requiring precise temperature control, such as melting and refining of non-ferrous metals, steel, and alloys. It is also favored for small to medium-scale operations.
- Arc Furnace: Primarily used in large-scale steelmaking and recycling processes, where high temperatures and large volumes of metal are required. It is less suitable for applications needing precise temperature control.
-
Technology Advancements:
- Induction Furnace: Modern induction furnaces often utilize advanced technologies like IGBT induction furnace systems, which improve energy efficiency, control, and reliability. These systems are particularly beneficial for high-precision applications.
- Arc Furnace: While arc furnaces have also seen technological improvements, they remain less efficient than induction furnaces due to their inherent design limitations.
-
Environmental Impact:
- Induction Furnace: Generally considered more environmentally friendly due to higher efficiency and lower emissions. The direct heating process reduces energy waste and associated emissions.
- Arc Furnace: Tends to have a higher environmental impact due to lower efficiency and greater heat loss, which results in higher energy consumption and emissions.
In summary, the choice between an induction furnace and an arc furnace depends on the specific requirements of the application, including the scale of operation, desired efficiency, and precision needed. Induction furnaces excel in efficiency and precision, while arc furnaces are better suited for large-scale, high-temperature processes.
Summary Table:
Feature | Induction Furnace | Arc Furnace |
---|---|---|
Heating Mechanism | Direct heating via electromagnetic induction | Indirect heating via electric arc and slag |
Thermal Efficiency | High efficiency due to direct heating | Lower efficiency due to heat loss and indirect heating |
Heat Loss | Minimal heat loss | Significant heat loss through furnace structure |
Applications | Precision temperature control, small to medium-scale operations | Large-scale steelmaking and recycling |
Technology Advancements | Advanced systems like IGBT induction furnaces improve efficiency and control | Limited improvements due to design constraints |
Environmental Impact | Lower emissions and energy waste | Higher emissions and energy consumption |
Still unsure which furnace suits your needs? Contact our experts today for personalized advice!