Biochar gasification and pyrolysis are two distinct thermal conversion processes used to transform biomass into valuable products, but they differ significantly in their operating conditions, mechanisms, and outputs. Pyrolysis occurs in the absence of oxygen, producing bio-oil, biochar, and syngas, while gasification involves limited oxygen or steam to primarily produce combustible gases like syngas. The key differences lie in the presence of oxygen, the nature of the chemical reactions, and the composition of the end products. Understanding these differences is crucial for selecting the appropriate process based on the desired outputs and applications.
Key Points Explained:
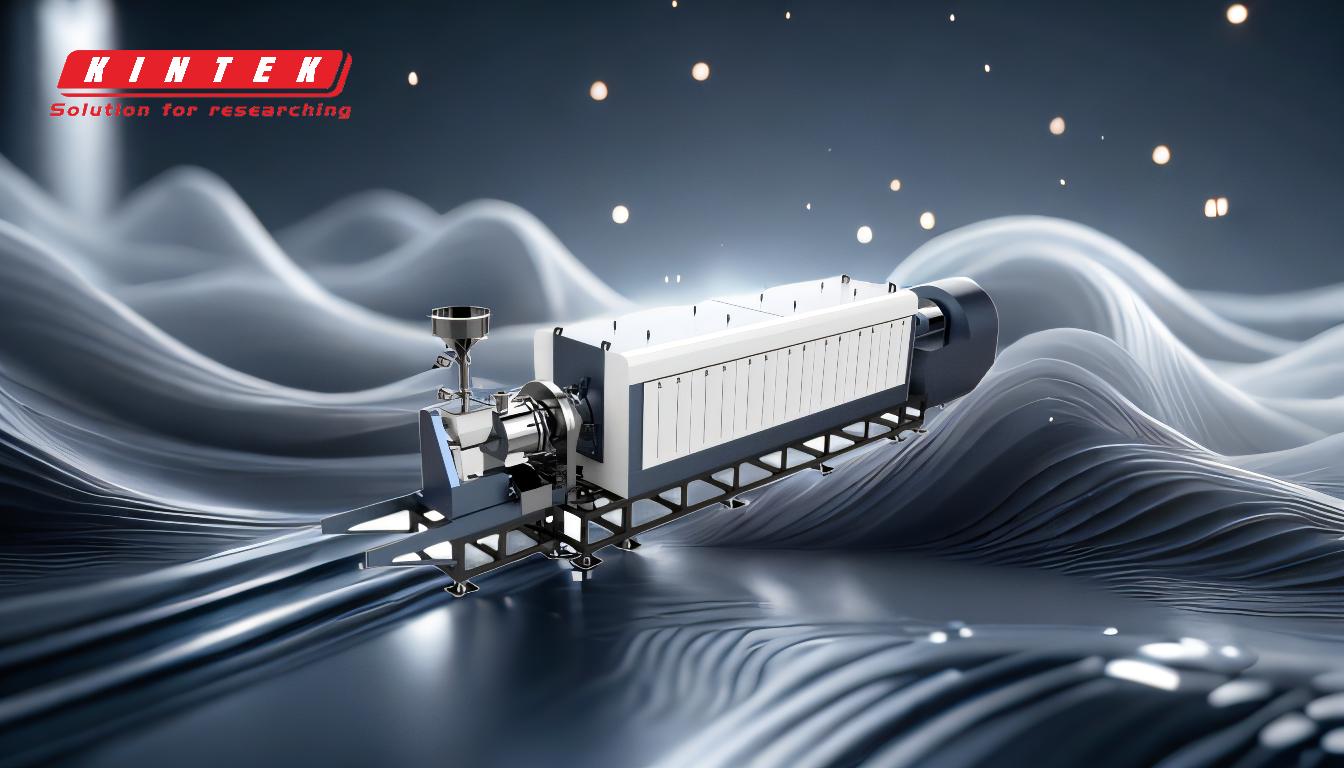
-
Presence of Oxygen:
- Pyrolysis: Occurs in the complete absence of oxygen or with a very limited supply that prevents gasification. This anaerobic environment ensures that thermal decomposition happens without significant oxidation.
- Gasification: Involves the introduction of limited oxygen or steam, which allows partial oxidation of the biomass. This controlled oxidation is essential for converting solid carbonaceous materials into gaseous fuels.
-
Chemical Reactions:
- Pyrolysis: Primarily involves thermal decomposition (thermolysis) of biomass into smaller molecules. The absence of oxygen prevents combustion, leading to the formation of bio-oil, biochar, and syngas.
- Gasification: Combines pyrolysis with partial oxidation and reforming reactions. The presence of oxygen or steam facilitates the conversion of residual carbon solids into combustible gases, primarily syngas (a mixture of hydrogen, carbon monoxide, and methane).
-
Output Products:
-
Pyrolysis: Produces three main outputs:
- Bio-oil: A liquid fuel that can be further refined.
- Biochar: A solid carbon-rich material used for soil amendment or carbon sequestration.
- Syngas: A mixture of hydrogen, carbon monoxide, and other hydrocarbons, often requiring additional reforming for clean syngas production.
- Gasification: Primarily produces syngas, which is a cleaner and more energy-dense gas mixture compared to pyrolysis syngas. The process minimizes solid and liquid byproducts, focusing on maximizing gaseous output.
-
Pyrolysis: Produces three main outputs:
-
Process Conditions:
- Pyrolysis: Typically operates at moderate temperatures (400–600°C) and atmospheric pressure. The absence of oxygen allows for slower, more controlled decomposition.
- Gasification: Operates at higher temperatures (700–1,200°C) and may involve higher pressures. The addition of oxygen or steam accelerates the conversion of solids into gases.
-
Applications:
- Pyrolysis: Suitable for applications requiring biochar (e.g., agriculture, carbon sequestration) or bio-oil (e.g., biofuel production). It is also used when a mix of solid, liquid, and gaseous products is desired.
- Gasification: Ideal for energy generation and syngas production, particularly in industrial settings where clean and efficient fuel is needed. It is also used in combined heat and power (CHP) systems.
-
Energy Efficiency and Byproducts:
- Pyrolysis: Less energy-intensive but produces a broader range of byproducts, which may require additional processing or refining.
- Gasification: More energy-efficient in terms of converting biomass into usable fuel, with fewer byproducts. However, it requires careful control of oxygen and steam levels to avoid complete combustion.
-
Environmental Impact:
- Pyrolysis: Produces biochar, which can be used to improve soil health and sequester carbon, making it environmentally beneficial. However, the syngas produced may contain impurities that require further treatment.
- Gasification: Produces cleaner syngas with fewer impurities, reducing the need for additional processing. However, the process may release more carbon dioxide if not properly managed.
By understanding these differences, stakeholders can choose the most suitable process based on their specific needs, whether it is for energy production, soil enhancement, or carbon sequestration.
Summary Table:
Aspect | Pyrolysis | Gasification |
---|---|---|
Presence of Oxygen | Absence of oxygen | Limited oxygen or steam |
Chemical Reactions | Thermal decomposition (thermolysis) | Pyrolysis + partial oxidation and reforming |
Output Products | Bio-oil, biochar, syngas | Primarily syngas |
Process Conditions | Moderate temperatures (400–600°C), atmospheric pressure | Higher temperatures (700–1,200°C), higher pressures |
Applications | Biochar (agriculture, carbon sequestration), bio-oil (biofuel production) | Energy generation, syngas production (industrial, CHP systems) |
Energy Efficiency | Less energy-intensive, broader byproducts | More energy-efficient, fewer byproducts |
Environmental Impact | Biochar for soil health, carbon sequestration; syngas may need refining | Cleaner syngas, fewer impurities; potential CO2 release if not managed |
Need help choosing between biochar gasification and pyrolysis? Contact our experts today for tailored solutions!