Centrifugation and filtration are two widely used separation techniques in laboratories and industrial processes, each relying on different principles and forces to achieve separation. Centrifugation utilizes centrifugal force to separate components based on their density differences, while filtration relies on a pressure gradient to separate particles based on size. Centrifugation is particularly effective for separating fine particles or immiscible liquids, whereas filtration is ideal for removing larger particles from a fluid. The choice between these methods depends on the nature of the mixture, the desired outcome, and the scale of operation. Below, we delve into the key differences between these techniques, focusing on the forces involved and their applications.
Key Points Explained:
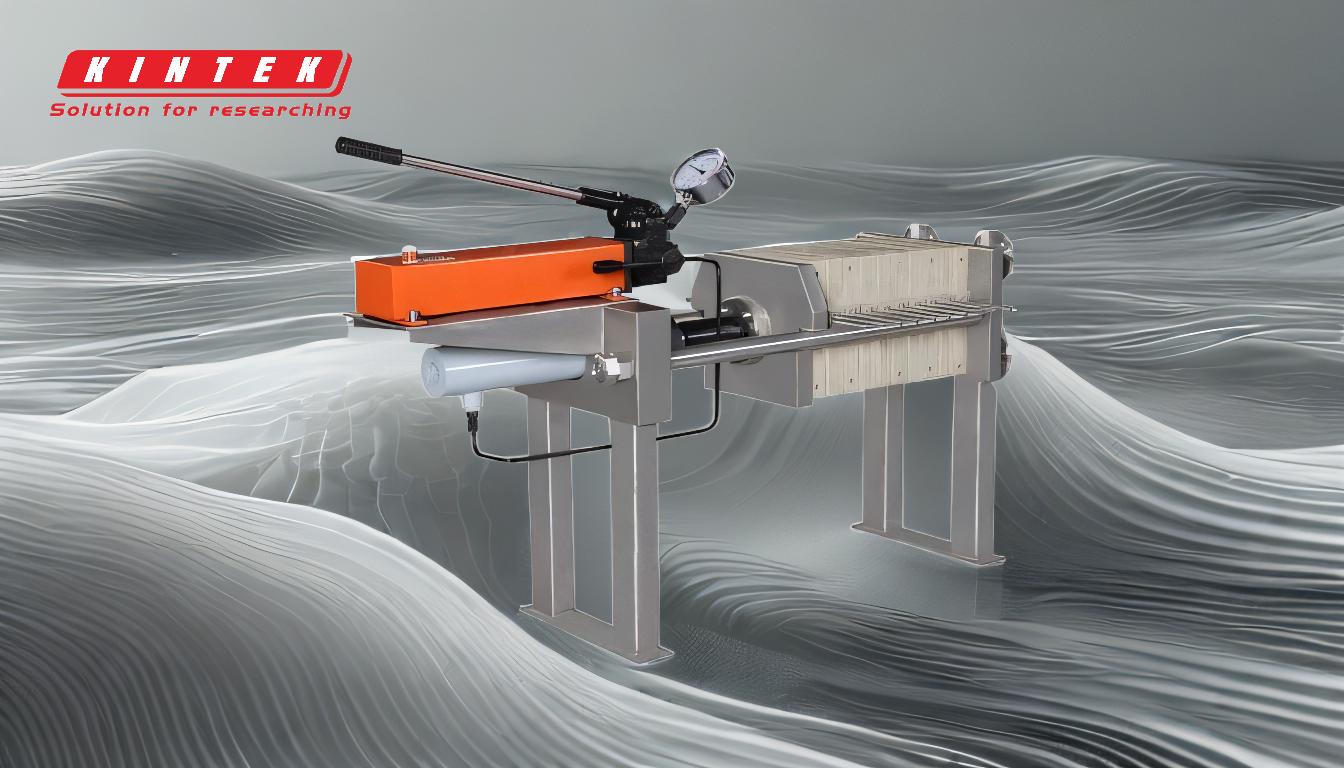
-
Principle of Separation:
- Centrifugation: This technique uses centrifugal force, which is generated by spinning a sample at high speeds. The force causes denser components to move outward and settle at the bottom, while less dense components remain closer to the center. This method is particularly effective for separating components with small density differences, such as cells, proteins, or immiscible liquids.
- Filtration: Filtration relies on a pressure gradient to force a fluid through a filter medium, which retains particles larger than the pore size of the filter. The driving force can be gravity, vacuum, or applied pressure. Filtration is suitable for separating larger particles, such as precipitates or debris, from a liquid.
-
Forces Involved:
- Centrifugation: The primary force is centrifugal force, which is a pseudo-force that appears to act outward on a mass in a rotating frame of reference. This force is proportional to the mass of the particles, the square of the angular velocity, and the radius of rotation. The formula for centrifugal force is ( F = m \cdot \omega^2 \cdot r ), where ( m ) is the mass, ( \omega ) is the angular velocity, and ( r ) is the radius.
- Filtration: The driving force is the pressure difference across the filter medium. This can be achieved through gravity (gravity filtration), vacuum (vacuum filtration), or applied pressure (pressure filtration). The force required depends on the viscosity of the fluid, the size of the particles, and the pore size of the filter.
-
Applications:
- Centrifugation: Commonly used in biological and chemical laboratories for separating cell components, isolating DNA, purifying proteins, and separating immiscible liquids like oil and water. Industrial applications include wastewater treatment and the separation of cream from milk.
- Filtration: Widely used in both laboratory and industrial settings for clarifying liquids, sterilizing solutions, and removing particulate matter. Examples include air filtration, water purification, and the separation of solids from liquids in chemical processes.
-
Equipment:
- Centrifugation: Requires a centrifuge, which consists of a rotor to hold the sample tubes and a motor to spin the rotor at high speeds. Different types of centrifuges include benchtop centrifuges, ultracentrifuges, and refrigerated centrifuges, each suited for specific applications.
- Filtration: Involves a filter medium (such as filter paper, membrane filters, or sintered glass) and a filtration apparatus (like a Büchner funnel, filter flask, or syringe filter). The choice of equipment depends on the scale and nature of the separation.
-
Advantages and Limitations:
-
Centrifugation:
- Advantages: High separation efficiency, ability to handle small particles, and suitability for both small-scale and large-scale operations.
- Limitations: Requires specialized equipment, can generate heat, and may not be suitable for heat-sensitive samples.
-
Filtration:
- Advantages: Simple and cost-effective, suitable for a wide range of particle sizes, and can be used for both small-scale and large-scale operations.
- Limitations: May clog with fine particles, requires frequent replacement of filter media, and is less effective for separating components with similar sizes.
-
Centrifugation:
-
Operational Considerations:
- Centrifugation: Speed, time, and temperature are critical parameters. Over-centrifugation can damage samples, while insufficient centrifugation may result in incomplete separation.
- Filtration: The choice of filter medium, pore size, and pressure gradient are crucial. Clogging and filter integrity must be monitored to ensure efficient separation.
In summary, centrifugation and filtration are complementary techniques, each with its own strengths and limitations. The choice between them depends on the specific requirements of the separation process, including the nature of the mixture, the desired purity, and the scale of operation. Understanding the forces involved and the operational considerations is essential for selecting the most appropriate method.
Summary Table:
Aspect | Centrifugation | Filtration |
---|---|---|
Principle of Separation | Uses centrifugal force to separate components based on density differences. | Relies on a pressure gradient to separate particles based on size. |
Forces Involved | Centrifugal force (( F = m \cdot \omega^2 \cdot r )). | Pressure difference (gravity, vacuum, or applied pressure). |
Applications | Separates fine particles, immiscible liquids, cells, DNA, and proteins. | Removes larger particles, clarifies liquids, and sterilizes solutions. |
Equipment | Centrifuge (rotor, motor). | Filter medium (filter paper, membrane filters) and filtration apparatus. |
Advantages | High efficiency, handles small particles, scalable. | Simple, cost-effective, wide particle size range. |
Limitations | Requires specialized equipment, generates heat, not ideal for heat-sensitive samples. | May clog, frequent filter replacement, less effective for similar-sized particles. |
Need help choosing the right separation technique for your lab? Contact our experts today for personalized advice!