Chemical Vapor Deposition (CVD) and Atomic Layer Deposition (ALD) are both techniques used to deposit thin films onto substrates, but they differ significantly in their mechanisms, precision, and applications. CVD involves the use of gaseous precursors that chemically react on the substrate surface to form a solid film, typically at high temperatures. ALD, on the other hand, is a more precise method within the CVD family that deposits materials in a layer-by-layer fashion using sequential, self-limiting reactions. This results in highly uniform and conformal films, even on complex geometries, and operates at lower temperatures compared to CVD.
Key Points Explained:
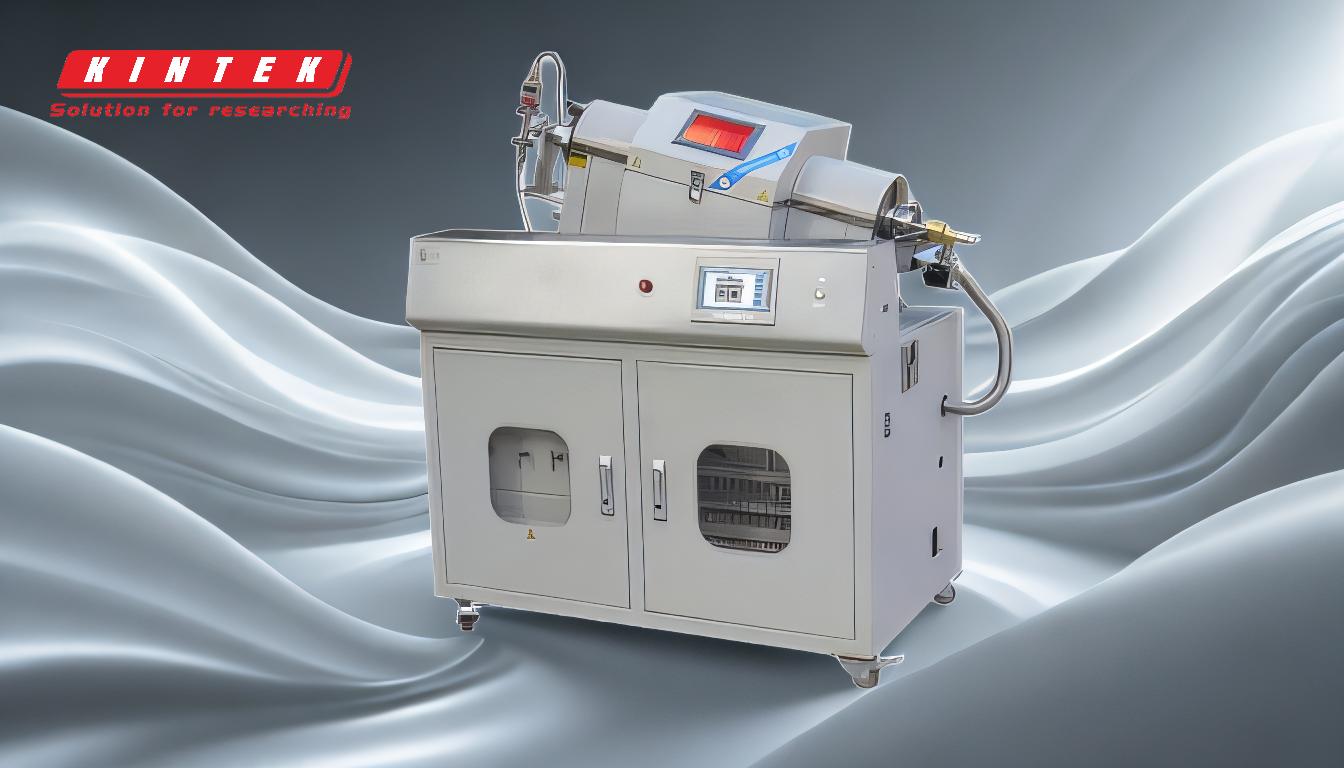
-
Mechanism of Deposition:
- CVD: In CVD, gaseous precursors are introduced into the reaction chamber simultaneously, where they react on the substrate surface to form a solid film. The process is continuous and can occur at high temperatures, leading to rapid film growth.
- ALD: ALD breaks down the deposition process into discrete steps. Precursors are introduced sequentially, one at a time, and each precursor reacts with the surface in a self-limiting manner, forming a single atomic layer. This ensures precise control over film thickness and uniformity.
-
Precursor Delivery:
- CVD: Precursors are delivered together in a continuous flow, leading to simultaneous reactions on the substrate surface.
- ALD: Precursors are delivered in separate pulses, with a purge step in between to remove any excess precursor and by-products. This sequential delivery ensures that only one atomic layer is deposited at a time.
-
Film Uniformity and Conformality:
- CVD: While CVD can produce uniform films, it may struggle with conformality on complex or high-aspect-ratio structures due to the continuous nature of the process.
- ALD: ALD excels in producing highly uniform and conformal films, even on intricate geometries, because of its layer-by-layer approach and self-limiting reactions.
-
Temperature Requirements:
- CVD: Typically requires high temperatures to facilitate the chemical reactions necessary for film deposition.
- ALD: Operates at lower temperatures, making it suitable for temperature-sensitive substrates. The controlled temperature range also contributes to the precision of the deposition process.
-
Applications:
- CVD: Widely used in the semiconductor industry for depositing a variety of materials, including silicon dioxide, silicon nitride, and polysilicon. It is also used in coating applications where high deposition rates are required.
- ALD: Preferred for applications requiring ultra-thin, highly uniform films, such as in advanced semiconductor devices, MEMS, and nanotechnology. ALD is also used for depositing multi-layer films with precise thickness control.
-
Reaction Chamber Environment:
- CVD: The reaction chamber contains all precursors simultaneously, leading to a more dynamic and potentially less controlled environment.
- ALD: The reaction chamber is purged between precursor pulses, ensuring that only one precursor is present at any given time. This results in a more controlled and stable environment, reducing the risk of unwanted reactions.
-
Scalability and Throughput:
- CVD: Generally offers higher throughput due to its continuous nature, making it more suitable for large-scale production.
- ALD: While ALD is slower due to its sequential nature, it is highly scalable for applications requiring precise control over film thickness and uniformity, such as in the production of advanced electronic components.
In summary, while both CVD and ALD are used for thin film deposition, ALD offers superior precision, uniformity, and conformality, making it ideal for applications requiring ultra-thin, high-quality films. CVD, on the other hand, is better suited for applications where higher deposition rates and scalability are more critical.
Summary Table:
Aspect | CVD | ALD |
---|---|---|
Mechanism | Continuous deposition with simultaneous precursor reactions | Sequential, layer-by-layer deposition with self-limiting reactions |
Precursor Delivery | Continuous flow of precursors | Separate pulses with purge steps in between |
Film Uniformity | Uniform films but struggles with complex geometries | Highly uniform and conformal films, even on intricate structures |
Temperature | High temperatures required | Operates at lower temperatures, suitable for sensitive substrates |
Applications | Semiconductor industry, high deposition rates | Advanced semiconductors, MEMS, nanotechnology, ultra-thin films |
Reaction Chamber | Dynamic environment with simultaneous precursors | Controlled environment with sequential precursor pulses |
Scalability | High throughput, suitable for large-scale production | Slower but scalable for precision applications |
Need help choosing between CVD and ALD for your application? Contact our experts today for tailored advice!